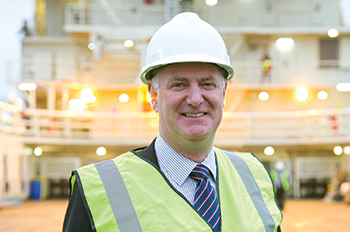
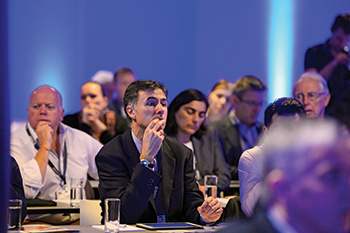
At the recently held StocExpo Conference, Paul Harrison, technical manager for Hydrocarbon Management at The Energy Institute looked at Loss Control. As a review of his talk he outlines the importance of developing measurement guidelines
The Energy Institute (EI) was formed in 2003 on the amalgamation of the Institute of Petroleum (IP) and the Institute of Energy. The institute is an independent charity, not a trade association, and can therefore act as an honest broker between the various parts of the industry, regulators, government agencies, etc.
Strategic aims of the EI are to develop knowledge, deliver skills and improve standards.
One way in which these aims are achieved is by publishing guidance covering many aspects of the energy business. The technical department produces guidelines on topics ranging from process plant safety to offshore wind farm installation to road tanker operations and includes environment and health in its remit. Hydrocarbon management (essentially quantity and quality measurement and loss control) remains a key activity.
Technical guidance – committee activities
EI guidelines are not written by a small group of EI 'experts' sitting in London. All work is initiated and developed by committees of representatives from companies closely involved with the subject being addressed. Guidance most relevant to the independent storage business is developed through two main committees; Hydrocarbon management committee (HMC-4)Oil transportation measurement and HMC-3 Petroleum measurement and cargo inspection. The first of these is our largest committee with 28 members internationally, including most of the major oil companies. The Oil Companies International Marine Forum (OCIMF), Intertanko, International Federation of Inspection Agencies (IFIA) and International Bunker Industry Association (IBIA) are also represented. HMC-3 includes individual independent inspection companies and a number of oil companies. A third committee, HMC-2 refinery and downstream measurement covers overall terminal balance and gantry metering issues.
Independent storage companies are currently not represented. This is unfortunate as much of the guidance which the committees produce is relevant to the sector.
Measurement and loss control guidelines
The majority of the measurement guidelines and standards in use today were initially developed in the late 1970s and 1980s. While many of the basic techniques remain the same, guidance needs to be regularly updated and developed to respond to changing market needs and to new developments, not only in measurement technology but also product specifications and legislation. Increased safety and environmental awareness is also having a significant impact on working practices.
Loss control involves quality as well as quantity with the emphasis now increasingly on quality as the financial loss resulting from contaminated products is now generally greater than that which might be suffered from a volumetric loss due to measurement inaccuracies. Further, increasingly tight product specifications increase the risk of contamination occurring. This has led to the development of guidance relating to cargo handling rather than basic measurement. Quality issues are seen as particularly relevant to the storage sector as terminals do not generally own the product but are liable to claims over quality issues. However, excess losses (generally greater than 0.2 per cent of throughput for a term arrangement) will also result in a claim.
Typical terminal requirements
Tank measurements: With the majority of terminals using static measurement rather than flow meters, the focus is on tank gauging systems. While modern radar gauges can provide reliable level measurement, tanks should be provided with a means to check readings manually, preferably via a second stilling well. Reliable temperature measurement is vital, with 1 deg centigrade corresponding to up to 0.1 per cent difference in volume for lighter products.
Sampling facilities: Access for taking samples from tanks, jetty lines and manifolds is important as these samples will provide the information necessary to confirm quality and, should problems occur, to determine where and how any contamination occurred.
Product handling facilities: The ability to segregate products or product groups within the terminal is more critical than ever. Typical requirements are seen as: Positive isolation of products/product groups with double block and bleed valves, spades or removable spools; manifolds designed to minimise 'dead legs'; and facilities to clear common lines by pigging or draining and the ability to account for any line fill between the jetty and the tanks.
Additive injection facilities and blending: The use of additives to improve product quality is now common and dedicated facilities to inject additives during loading are becoming increasingly important. Blending operations are also becoming more frequent and tank mixers, along with the ability to circulate product between tanks to produce a blend or to blend in a controlled manner from two tanks during loading is very useful.
While new installations should be designed with these issues in mind this is not always the case, and few old or re purposed facilities are able to meet increasingly strict requirements, increasing the risk of losses and contamination.
Storage operations
Introduction of new products: The introduction of Fatty Acid Methyl Esters (Fame), with strong backing from government in many countries, caused concerns throughout the supply chain.
The EI led work covering microbial growth and sampling together with development of a range of new laboratory test methods to determine both the quality of Fame and the Fame content of fuels. A large joint industry project was established to look into the possibility of increasing the initial 5 ppm limit on Fame in aircraft fuel and it has now been agreed to increase this to 50 ppm and then 100 ppm, following a trial period. New products continue to be introduced into the market, including hydrotreated vegetable oils and various synthetic fuels. Each need to be carefully assessed with regard to stability, potential for contamination and measurement characteristics, with guidance developed as necessary.
Safety and environmental standards: Increased safety and environmental awareness, coupled with the use of inert gas and an increased number of cargoes found to have hydrogen sulphide (H2S) in the headspaces, has led to the majority of ocean going tankers being fitted with vapor control valves such that measurement and sampling equipment can only be introduced to the tanks via a small diameter (typically 50 mm) systems which restrict vapour emission.
These systems increase the difficulty of obtaining samples which can be used to reliably determine the characteristics of the whole tank, particular where contents are not homogeneous.
Similar safety and environmental concerns apply to shore tanks, coupled with the risks associated with climbing to and from the tank roof or gauging platform, carrying measurement and sampling equipment, sample containers, etc. It seems likely that regularly climbing tanks to obtain samples will be limited at many locations in the very near future. Tank side tap samples and floating arm sample systems are not seen as ideal solutions and it seems clear that development is required in this area.
EI HMC committees continue to discuss and share possible solutions to all the issues noted above, producing and updating guidance on measurement and sampling and product handling, including tank cleaning.