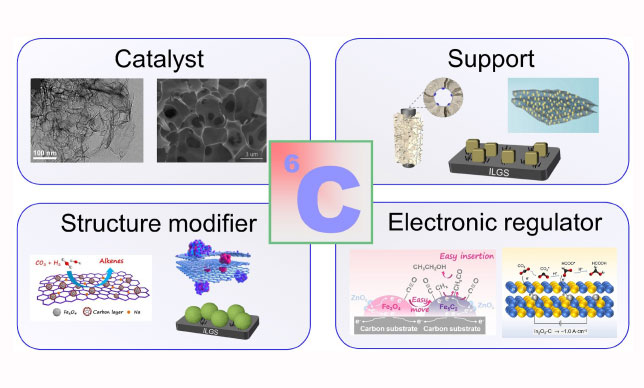
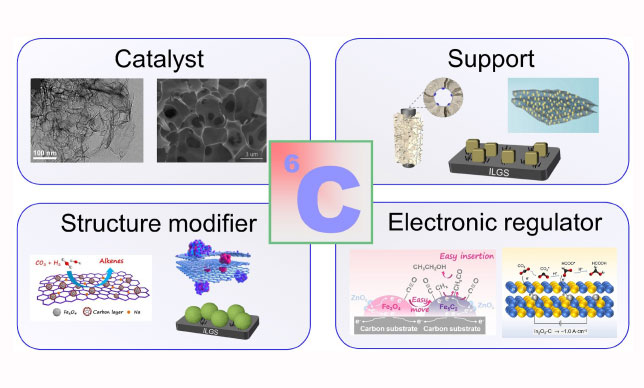
Carbon-based materials revolutionise CO2 conversion, offering sustainable pathways for reducing emissions and producing chemicals, as breakthroughs highlight electrocatalysis and thermocatalysis for scalable, efficient processes
As the global challenge of climate change intensifies, scientists are increasingly turning to innovative technologies for carbon dioxide (CO2) conversion.
Carbon-based materials have emerged as a powerful solution in the quest to transform CO2 from a greenhouse gas into a valuable resource.
Recent advancements outlined by researchers Wenhang Wang, Yang Wang, Xiangjin Kong, Hui Ning, and Mingbo Wu from China's Liaocheng University and China University of Petroleum (East China) in their paper ‘Carbon-based material for CO2 catalytic conversion applications’ reveal groundbreaking methods for utilising these materials to drive sustainable chemical processes.
THE ROLE OF CARBON IN CO2 CONVERSION
The urgency of addressing CO2 emissions cannot be overstated. With annual global emissions exceeding 35 billion tonnes and atmospheric concentrations nearing 420 ppm – well above the safe limit of 350 ppm – climate targets are under significant threat.
CO2, however, is not merely a pollutant but an untapped resource. Harnessing it through catalytic processes offers a dual benefit: reducing emissions while creating valuable chemicals and fuels.
At the forefront of this effort are carbon-based materials, which possess unique properties ideal for catalysis.
These include low cost, high stability, abundant availability, and the ability to tailor their structure and electronic properties.
In catalytic systems, carbon materials can serve as bulk catalysts, supports, or modifiers, enhancing the performance of reactions through improved stability, selectivity, and reactivity.
The study highlights two primary approaches to CO2 transformation: electrocatalysis and thermocatalysis.
Electrocatalysis leverages renewable energy sources like solar or wind power to drive the conversion of CO2 into fuels and chemicals under ambient conditions.
Thermocatalysis, on the other hand, uses high temperatures to achieve similar results, with the added advantage of industrial scalability.
Carbon materials play an integral role in both pathways, offering new possibilities for efficient and sustainable CO2 utilisation.
ELECTROCATALYSIS: A SUSTAINABLE PATHWAY
Electrocatalytic reduction of CO2 is a promising method for converting this greenhouse gas into high-value products such as carbon monoxide (CO), formate, methane, ethylene, and ethanol.
![]() |
Schematic diagram of CO2 hydrogenation to ethanol via Na-Fe@C and K-CuZnAl catalysts |
This approach utilises renewable electricity, making it a clean and sustainable strategy aligned with global decarbonisation goals. The versatility of carbon materials enables a range of applications in this domain.
For instance, the study discusses carburized indium oxide nanorods (In2O3-C) as an innovative catalyst for formate production.
Through a novel synthesis method, these nanorods achieved a Faradaic efficiency of 97 per cent at optimal voltages, surpassing many traditional catalysts in both performance and stability.
The incorporation of carbon into the catalyst structure was shown to regulate its electronic properties, enhancing the activity of the indium sites and facilitating the conversion process.
Another breakthrough involves hollow fibre catalysts, such as SnO2-Bi2O3/C hollow nanofibres. These structures are designed using advanced electrospinning techniques, which enable precise control over the distribution of active sites.
With efficiencies exceeding 90 per cent for CO2 reduction to formate, these fibres demonstrate the potential of nanostructured carbon materials to optimise reaction kinetics and selectivity.
Carbon materials also play a critical role in improving the performance of multi-carbon products. For example, functionalised graphite nanosheets combined with copper oxide nanoparticles have been used to produce ethylene and ethanol.
The interface between carbon and metal in these catalysts promotes C–C coupling, a key step in forming multi-carbon products.
Additionally, ionic liquid-functionalised graphite supports have proven effective in enhancing the dispersion of active metal particles, leading to significant improvements in efficiency and product yield.
These advancements underscore the versatility of carbon materials in electrocatalytic applications, where their ability to conduct electrons, stabilise active sites, and facilitate selective reactions is unparalleled.
THERMOCATALYSIS: EFFICIENCY AT SCALE
Thermocatalytic CO2 conversion offers another viable pathway, particularly for industrial applications where scalability and high throughput are critical.
By leveraging the unique properties of carbon materials, researchers have developed catalysts capable of producing a wide range of products, including light olefins, aromatics, alcohols, and even jet fuel.
A standout innovation in this area is the MOF-derived Na-Fe@C catalyst, which combines iron nanoparticles with graphene-like carbon layers.
This catalyst excels in converting CO2 into high-value aromatics through a modified Fischer–Tropsch synthesis pathway.
The carbon layer not only enhances the stability of the active sites but also prevents undesirable aggregation and deactivation during the reaction process.
When paired with acidic zeolites, the Na-Fe@C catalyst achieves remarkable selectivity and efficiency.
In one experiment, this combination produced a record-breaking space–time yield of 203.8 gCH2/kg·h for aromatics, showcasing the synergistic potential of carbon materials in hybrid catalytic systems.
Ethanol synthesis from CO2 is another area where carbon materials have made significant contributions.
By tailoring the electronic structure of catalysts through carbon buffer layers, researchers have achieved precise control over reaction pathways.
For example, a Na-ZnFe@C catalyst demonstrated a CO2 conversion rate of 39.2 per cent, with ethanol selectivity reaching 35 per cent. These results highlight the potential of carbon-modified catalysts to optimise product distribution and enhance efficiency.
Carbon materials also serve as structure modifiers, as demonstrated by the development of core–shell catalysts like Na-Fe3O4@C.
These catalysts use a carbon-coated iron oxide core to regulate carbon chain growth, enabling selective production of light olefins.
The precise design of such structures not only improves catalytic performance but also addresses challenges related to mass and heat transfer, which are crucial for maintaining efficiency in large-scale applications.
A PATH FORWARD
The advances outlined in this research underscore the transformative potential of carbon materials in CO2 conversion technologies. Their versatility and effectiveness in both electrocatalysis and thermocatalysis make them indispensable tools in the fight against climate change.
From producing renewable fuels to creating valuable chemicals, these materials offer a sustainable pathway for turning CO2 from a liability into an asset.
Despite the significant progress, challenges remain. Scaling up these technologies for industrial use, improving the durability of carbon-based catalysts, and achieving greater selectivity for multi-carbon products are critical areas for further exploration.
The study emphasises the importance of understanding the interaction between carbon materials and active metals, as well as the need for advanced characterisation techniques to unravel the mechanisms at play.
Looking ahead, the integration of renewable energy with carbon-based catalytic systems presents an exciting opportunity to decarbonise industries and achieve global climate goals.
By continuing to innovate and refine these technologies, researchers can unlock new possibilities for CO2 utilisation, paving the way for a sustainable future.
* This article was adapted from the original research paper written by Wenhang Wang et al and published in the Carbon Future journal (DOI: 10.26599/CF.2024.9200016)
By Abdulaziz Khattak