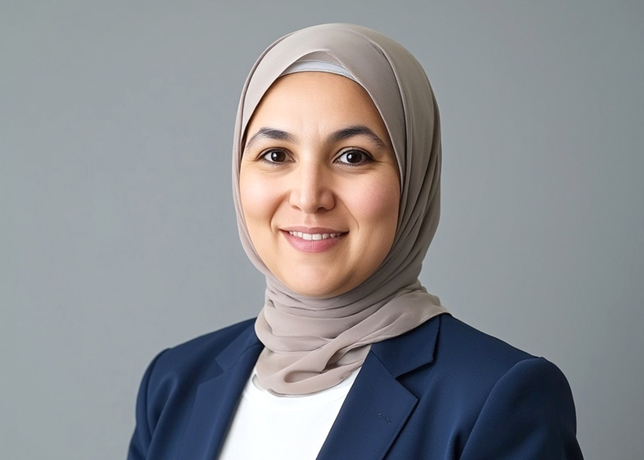

STATS Group completes complex hot tapping and BISEP® line stopping for OQGN’s 48-inch gas pipeline in Oman, ensuring safe, sustainable integration of Sur gas supply station extension, Mark Gault, Vice President Middle East, STATS Group, tells OGN
STATS Group was contracted to perform hot tapping and line stopping operations for the OQ Gas Networks (OQGN) on its 48-inch gas pipeline in Sur, Sultanate of Oman.
This complex project involved deploying dual STATS BISEP® line stop tools to achieve a leak-tight double block and bleed isolation of a 150-m pipeline section, ensuring the safe and efficient integration of a new extension of Sur gas supply station.
The gas flow was maintained continuously through an integrated bypass operating at 75 bar, the operation eliminated the need to shut down and purge the entire 65-km pipeline, significantly reducing greenhouse gas emissions by preventing large-scale venting and flaring.
The integration of the extended gas supply station into the existing 48-inch pipeline was successfully completed without disrupting service to OQGN customers.
By isolating the pipeline section and employing advanced hot tap and BISEP isolation technologies, the project team enabled safe, controlled modifications on a live system, ensuring uninterrupted gas supply and maintaining consistent pressure throughout the operation.
To support the project, STATS provided two 48-inch BISEPs each with a slab valve, split tee fitting and completion plug, rated to class 600.
ADVANCED ISOLATION TECHNOLOGY ENSURES SAFETY
In addition, STATS supplied SureTap® hot tap machines and personnel for 48-inch and 2-inch tapping operations.
STATS BISEP technology provides operators with pioneering hot tap installed line stopping capabilities to enable the safe and effective repair and modification of pressurised pipeline infrastructure.
![]() |
Mark Gault, Vice-President Middle East, STATS Group |
The patented BISEP provides a fail-safe double block and bleed isolation deployed through a single full bore hot tap intervention and is the only DNV Type Approved line stop tool.
This verifies that the design criteria satisfy the requirements for pipeline isolation plugs to provide dual seal and isolation in accordance with DNV-OS-F101 (Submarine Pipeline Systems) and recommended Practices; DNV-RP-F113 (Subsea Pipeline Repair); and in compliance with code ASME BPVC Section VIII, Division 2.
Prior to mobilisation to the worksite, all STATS supplied equipment undertook a client witnessed Factory Acceptance Test (FAT) at STATS operational facility in Abu Dhabi.
All equipment was tested at maximum isolation pressure to meet operational requirements and ensure full compliance with safety and operational standards.
The work scope began with the excavation of a 150-m straight pipe section on the 48-inch pipeline, parallel to the new extension of Sur gas supply station.
![]() |
A dual BISEP deployment with an integrated bypass |
Once the excavation was completed, two split tee fittings were welded onto the 48-inch pipeline, one at each tie-in location and hydrotested to verify the integrity of the welded joints.
Following successful testing of the fittings, STATS 48-inch slab valves and SureTap hot tap machine were installed.
Hot tapping was performed at each location and the pipe coupon recovered, allowing the hot tap machine to be removed providing full bore access for the BISEP isolation tool.
With access points created, the 48-inch BISEPs were installed on the slab valves, and a 50-m temporary bypass line was constructed and attached to the BISEP deployment launcher, ensuring continued gas flow once the BISEPs were deployed into the flowing pipeline.
The BISEPs were hydraulically deployed into the pipeline and activated, each plugging head features dual elastomer seals that are compressed to radially expand against the inside of the pipe wall.
Hydraulic activation allows for high integrity sealing, even in pipelines with internal corrosion, pitting or ovality issues.
The BISEP offers significant safety advantages over lip seal technologies, with the hydraulically activated dual seals providing leak-tight isolation of pressurised pipelines.
Once deployed each BISEP is subject to a test regime to independently test both the primary and secondary seals with full pipeline pressure (75 bar).
ENSURING OPERATIONAL AND ENVIRONMENTAL INTEGRITY
Each seal is tested in the correct direction and the pressure between the seals is vented, creating a zero-energy zone.
![]() |
A SureTap machine with a 48-inch completion plug |
The zero-energy zone between the seals is monitored throughout the workscope, confirming the isolation integrity with zero leakage, a crucial factor in the energy industry where any compromise in integrity can have severe consequences.
In addition, the line pressure acting against the BISEP pressure head offers a fail-safe feature by providing actuation independent of the hydraulic system.
Once the test regime was complete, an isolation certificate was issued to notify all parties of the safe isolation of the 50-m pipe section.
To enable the isolated section to be vented and purged, STATS supplied a mechanical strap clamp with a 2-inch branched off-take.
Once installed to the 48-inch pipeline, a hot tap machine and valve were installed and the pipeline drilled to provide a vent point.
The isolated pipeline section was then safely flared, and nitrogen-purged to eliminate any residual gas.
Once gas-free conditions were confirmed, a cold cutting machine was used to remove short sections of pipe spools, and the redundant pipeline section was safely removed.
A tie-in pipeline bend spool was precisely positioned and welded into place to provide connection to the Sur gas supply station.
![]() |
BISEPs deployed, isolating the 48-inch pipeline allowing a section to be removed and gas supply maintained through integrated bypass (80 bar) |
Upon completing the tie-in at both locations and commissioning the extension of Sur gas supply station by introducing gas, the isolation certificate was withdrawn.
The BISEPs were then gradually unset and retracted into the deployment launcher, and the slab valves were closed, allowing the recovery of the BISEPs and temporary bypass.
The hot tap machine was then reinstalled onto the slab valves and used to install 48-inch completion plugs into the flanges of the welded split tee fittings, ensuring secure and permanent blinding of the system.
The successful completion of this project highlights the exceptional execution, strong collaboration, and seamless communication between all stakeholders.
By leveraging advanced BISEP isolation technology, STATS ensured a safe and efficient operation without any safety incidents or disruptions to gas supply.
The ability to maintain uninterrupted production while preventing large-scale venting significantly reduced greenhouse gas emissions, reinforcing the project’s environmental benefits.
This achievement not only underscores the expertise and reliability of STATS technology but also sets a benchmark for safe, sustainable, and innovative pipeline intervention solutions in the industry.
OQGN holds a natural monopoly over critical gas transportation infrastructure in Oman as the exclusive owner and operator of the Natural Gas Transmission Network (NGTN).
It aims to champion the management and development of the NGTN through innovative and sustainable solutions.
OQGN prioritises maintaining high standards of operation and maintenance, which is reflected in the OQGN’s operational track-record, having delivered 99.99 per cent gas availability over the last 10 years and recorded no gas supply interruptions in 2023.
Its health, safety and environment record is also testament to its commitment to applicable occupational health and safety standards.
OQGN actively considers the interests of society at large and the economic development of Oman in the course of its operations and strives to maximise its engagement in and contribution to the Omani communities and supporting the government’s efforts towards environmental sustainability.