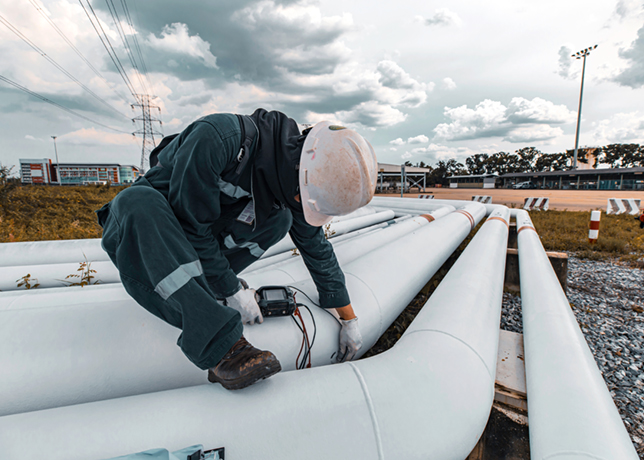
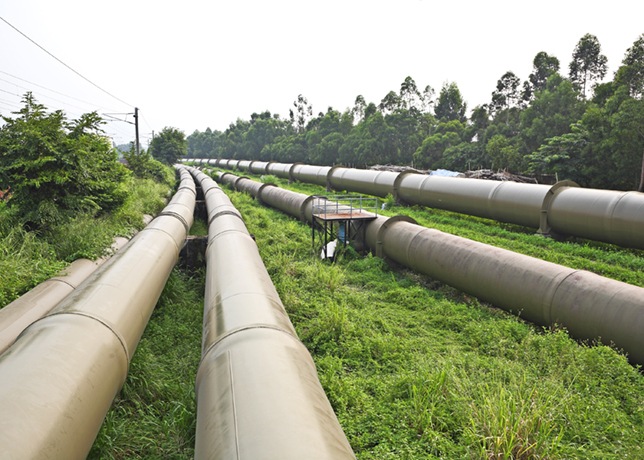
Cutting-edge computational models and experimental research, like AspenTech’s HYSYS and Tulsa Unified Model, enhance multiphase flow predictions, improving safety, cost-efficiency, and sustainability in oil and gas pipeline operations
In the intricate world of the oil and gas industry, the transport of multiphase fluids — combinations of gas, liquid, and sometimes solids — through pipelines represents a formidable engineering challenge.
This phenomenon, known as multiphase flow, is pivotal for efficient production and transportation, enabling the movement of unseparated fluid mixtures over vast distances.
From offshore rigs to onshore processing plants, accurately predicting and managing multiphase flow ensures safer, cost-effective, and environmentally sustainable operations.
A white paper by AspenTech, a leading software supplier for optimising asset performance, explores advances in computational modelling, such as those in Aspen HYSYS®, coupled with cutting-edge experimental research, are transforming how engineers tackle this complexity, addressing issues like pressure gradients, liquid hold-up, and flow regimes that dictate pipeline performance.
NAVIGATING THE COMPLEXITIES OF MULTIPHASE FLOW
Multiphase flow through pipes is defined by the simultaneous movement of multiple phases, typically gas and liquid, but occasionally including water or solids.
Unlike single-phase flow, where fluid properties are uniform, multiphase flow exhibits varied spatial arrangements, or flow regimes, such as stratified, slug, annular, or bubbly flow.
These regimes depend on factors like pipe geometry, fluid properties, and flow velocities. For instance, in horizontal pipes, gas may travel atop a liquid layer in stratified flow, while vertical pipes might see gas bubbles dispersed in a liquid matrix.
Each regime influences critical parameters: The pressure gradient (pressure drop per unit length), liquid hold-up (the fraction of liquid in the pipe), and frictional losses, all of which are essential for designing robust pipelines.
The significance of multiphase flow lies in its economic and operational impact. By transporting unseparated fluids, industries avoid costly separation facilities at production sites.
![]() |
Flow assurance ... innovations in chemical inhibitors prevent blockages in subsea pipelines |
A notable example is Vietnam’s Con Nam Son field, where a 420-km flowline transports gas and oil to a processing site with minimal preprocessing, slashing infrastructure costs.
However, this efficiency comes with challenges. Slug flow, where alternating pockets of liquid and gas cause pressure fluctuations, can damage pipelines or disrupt downstream equipment.
Flow assurance, preventing issues like hydrate formation, wax deposition, or corrosion, remains a priority, especially in deepwater operations where long flowlines and harsh conditions amplify risks.
To predict these behaviours, engineers rely on correlations—mathematical models that estimate flow attributes.
Aspen HYSYS, a leading process simulation software, offers a suite of such correlations, ranging from empirical models like Beggs and Brill to mechanistic ones like the Tulsa Unified Model.
Empirical models, derived from experimental data, are simpler but limited to specific conditions, often failing when applied to untested scenarios.
Mechanistic models, grounded in first principles, offer broader applicability but require complex closure relationships, sometimes introducing convergence issues in numerical simulations.
A study by AspenTech compared these correlations against experimental data from the Tulsa University Fluid Flow Project (TUFFP), a 35-year research initiative.
The Tulsa Unified Model excelled in predicting flow regimes, liquid hold-up, and pressure gradients across horizontal, inclined, and vertical geometries, outperforming empirical models like Beggs and Brill, which overpredicted pressure gradients in horizontal flows.
The TUFFP database, comprising over 1,100 data points from experiments with air-water, air-oil, and air-kerosene systems, revealed key insights.
For horizontal pipelines, the Tulsa Unified and HTFS models accurately predicted pressure gradients, though HTFS struggled with liquid hold-up.
In vertical flows, the empirical Aziz et al. model, tailored for gas-condensate systems, outperformed others, highlighting the importance of matching correlations to specific conditions.
However, the study noted limitations: Experiments used lab-scale pipes and non-hydrocarbon fluids, raising questions about scalability to field conditions.
This underscores a persistent challenge in multiphase flow modelling, bridging the gap for real-world applications.
Recent advancements have addressed these limitations. A 2024 article in the Petroleum Science journal highlighted improvements in mechanistic models, incorporating machine learning to refine closure relationships and enhance prediction accuracy across diverse flow conditions.
These hybrid models, trained on expansive datasets, adapt dynamically to new data, reducing reliance on empirical tuning.
For instance, computational fluid dynamics (CFD) tools now simulate three-dimensional flow patterns, offering granular insights into phase interactions.
Companies like SLB have integrated CFD with real-time monitoring systems, using sensors to track flow regimes and adjust operations dynamically, minimising risks like slugging or blockages.
Flow assurance remains a critical focus. Innovations in chemical inhibitors, such as anti-agglomerate hydrate inhibitors, prevent blockages in subsea pipelines, while advanced coatings reduce corrosion.
A 2025 report from Offshore Technology detailed how digital twins (virtual pipeline replicas) enable predictive maintenance by simulating multiphase flow under varying conditions.
These tools, combined with IoT sensors, allow operators to optimise flow rates, detect anomalies, and extend asset lifespans.
For example, Equinor’s Johan Sverdrup field in Norway uses digital twins to manage multiphase flow, achieving a 20 per cent reduction in downtime.
Despite progress, challenges persist. Three-phase flows (gas, oil, water) are less understood due to limited experimental data, as noted in the AspenTech study.
Scaling lab results to field conditions remains problematic, particularly for long pipelines with varying inclinations.
Environmental regulations also demand greener solutions, pushing research towards low-carbon flow assurance strategies.
Electrification of subsea systems, as trialled by TotalEnergies, reduces emissions while maintaining flow stability.
Meanwhile, open-source platforms like OLGA, a mechanistic model, are gaining traction for their transparency and adaptability, fostering collaborative research.
Looking ahead, the industry is poised for transformation. AI-driven models promise to revolutionise flow prediction by learning from real-time data, while collaborative efforts like TUFFP continue to expand experimental databases. Standardisation of correlations, as advocated in a 2025 Journal of Petroleum Science and Engineering study, could streamline model selection, enhancing reliability.
As pipelines extend into deeper waters and harsher environments, mastering multiphase flow will remain a cornerstone of energy innovation, balancing efficiency, safety, and sustainability.