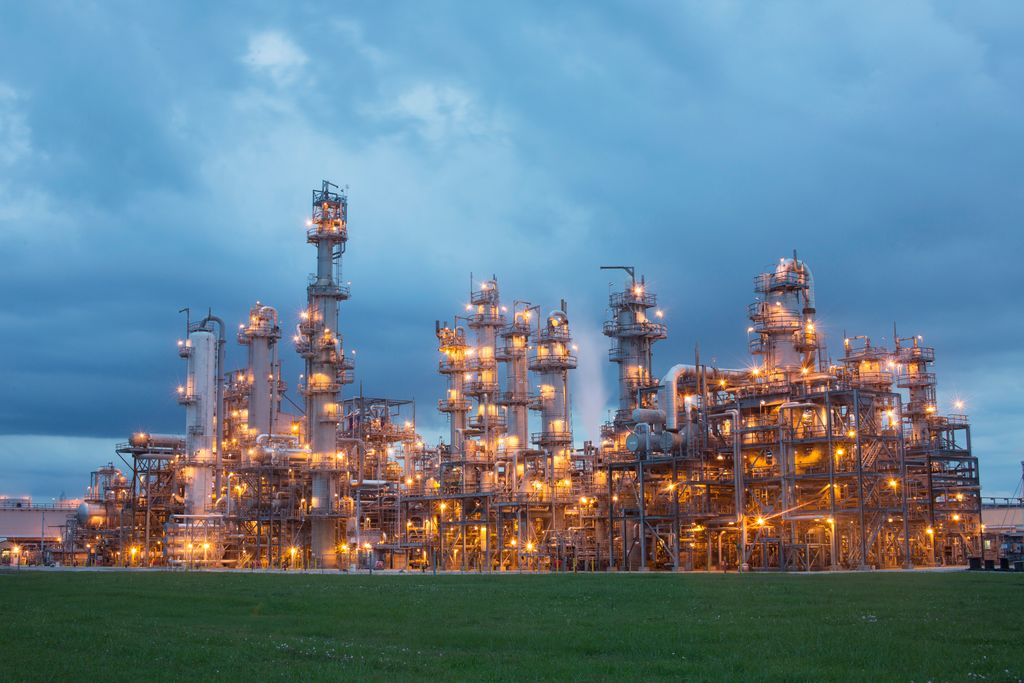
Rabigh Refining & Petrochemical Company (Petro Rabigh) has achieved an impressive 92 per cent catalyst selectivity at the start of the most recent cycle at its 600,000-t/y monoethylene glycol (MEG) production facility in Saudi Arabia.
Petro Rabigh was founded in 2005 as a joint venture between Saudi Aramco and Sumitomo Chemical. The plant produces petroleum-based products and ethylene- and propylene-based derivatives.
The plant uses the advanced Shell Omega process, which is based on the catalytic conversion of both ethylene to ethylene oxide and ethylene oxide to ethylene glycol.
Ethylene oxide catalyst selectivity is a key factor in the efficiency of MEG production: a higher selectivity means that smaller volumes of raw material are required to manufacture the product.
The cycle that started in May 2020 marked a change in catalyst from Shell Catalysts & Technologies’ S-888 (which had achieved an initial selectivity of 90.9%) to S-889 catalyst.
The resulting improvement of just over 1% will deliver significant savings and lead to higher profitability or enhanced competitiveness in what is, at present, a very challenging market.
This catalyst upgrade is expected to reduce raw materials requirements by 4,000 t/y for ethylene and 14,000 t/y for oxygen. Over a full cycle, these reductions could translate into a multimillion-dollar saving.
This outstanding performance is the result of both the improved catalyst and the way the unit is operated. The Petro Rabigh plant carried out a well-structured catalyst selection process with an emphasis on maximising performance and extending the run length.
In addition, the plant has been able to sustain very stable operations thanks to the tireless efforts of the highly skilled engineers and the relentless focus on keeping the catalyst fully optimised by careful chloride level adjustments.
The plant has been using Shell Catalysts & Technologies catalysts since 2009.