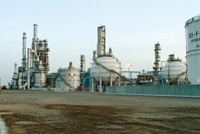
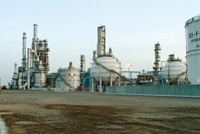
JUBAIL and Yanbu, which contribute 11.5 per cent of Saudi Arabia’s nonoil GDP, have attracted investments worth SR780 billion ($208 billion) so far, a sparkling example of a Gulf country diversifying its economy away from oil production.
Jubail, on the Arabian Gulf and Yanbu, on the Red Sea have driven the industrialisation of the kingdom since 1975, and it is here where the current surge in local and foreign investment in the non-oil economy is most evident. While Sadara, the multi-billion-dollar petrochemical development in Jubail, moves towards creating huge capacity and the world’s largest complex of its kind in the world, other investments in Jubail and Yanbu are also moving ahead for expansions.
The Kingdom of Saudi Arabia established the Royal Commission for Jubail and Yanbu (RCJY) about 35 years ago for the purpose of creating major industrial hubs. During the initial stage, these two industrial cities’ developments were oil-based.
Today, investment and development sector priorities have been diverted to petrochemical, gas, and downstream areas and the results are staggering. “Evidence of the Royal Commission’s success in building the integrated Global Petrochemicals Hub can be seen in the presence of about 300 petrochemicals and related companies in the region, creating precious jobs,” says Dr Alaa Nassif, executive president of Royal Commission for Jubail and Yanbu.
![]() |
Sadara ... creating huge capacity |
The $20 billion Sadara complex, comprising 26 manufacturing units, is designed to produce more than 3 million tonnes of high-value performance plastics and speciality chemical products.
Markets in Asia and beyond are awaiting the completion of Sadara’s first production facilities in 2015, and all of its facilities a year later, in preparation for which Sadara’s owners signed a marketing agreement recently under which The Dow Chemical Co, an equal owner with Saudi Aramco, will market most of Sadara’s products.
Anticipating the start of successful commercial operations at Sadara and aware of a global appetite to consume the products the complex will produce, the French have been encouraged to consider assembling large-scale investments of their own in the Royal Commission’s cities though it is unlikely their size will be anything near what is invested in the Saudi Aramco-Dow joint venture. Executives of 35 French companies led by Total Oil Co, met with officials of the Royal Commission of Jubail & Yanbu to discuss manufacturing opportunities in a range of industrial projects including petrochemicals.
Total is no stranger to Saudi Arabia and is a partner with Saudi Aramco in Satorp, the Saudi Aramco Total Refining and Petrochemical Company, whose production facilities are nearly complete in Jubail Industrial City 2. Total holds 37.5 per cent of the sharehoding with the Saudi powerhouse holding the remainder. If new French investments materialise it will mean the era of big investments in the kingdom is well and continuing. New French investments will be on top of mega projects approved by the Royal Commission in recent months and set to proceed. One of the deals is with Al Jubail Petrochemical Company (Kemya), a joint venture between Sabic and ExxonMobil for constructing a $3.2 billion facility for making ethylene propylene diene monomer, rubber and black carbon.
Jubail Chemical Industries Company (Jana) is setting up a chemicals plant of annual capacity of 600,000 tonnes with an investment outlay of $800 million. Sipchem is spending $750 million for producing ethylene vinyl acetate and low-density polyethylene and National Industrialisation Company or Tasnee is constructing a plant worth $373 million to produce super-absorbent polymers. Safco will undergo an expansion to raise urea capacity to 3.67 million tonnes per year at a cost of $533 million.
Even as plans are made to set up industries in Jubail, and as the Sadara complex still has several years to come on line, the talking point in energy circles is the SR50 billion Satorp which will have its commercial start-up soon. The ambitious plant will produce low sulphur transportation fuels, petrochemicals such as paraxylene, benzene and propylene and other products including petroleum coke and sulphur.
![]() |
Sabic ... strong presence in the twin cities |
Sabic has made progress in several domestic projects while one key unit to produce distilled alcohol products is set for completion in a year’s time. The 50,000 tonnes per year distilled alcohols plant will become operational in the second half of 2013 at Saudi Kayan, a Sabic affiliate. China’s Sinopec is constructing the plant.
Sabic has announced plans for a polyacetal (also known as polyoxymethylene or POM) facility at its affiliate Ibn Sina (National Methanol Co) in Jubail. Currently Ibn Sina produces MTBE (methyl tertiary butyl ether). The new plant will have annual capacity of 50,000 tonnes. Sabic has signed an agreement with Celanese, its partner at Ibn Sina, to develop the project.
Sabic affiliate Jubail Chemicals Storage and Services Company (JCSSC) has awarded EPC contracts for a new storage, handling and shipping terminal at King Fahd Industrial Port in Jubail to China National Chemical Engineering Corporation (CNCEC). The total investment is estimated to be $400 million. JCSSC is a joint venture in which Sabic holds 75 per cent and Vopak 25 per cent.
The first phase will consist of around 40 commodity and speciality chemical storage tanks, complete with truck handling and ship loading facilities for five berths. Joint venture partner Royal Vopak is the world’s largest independent tank storage service provider for bulk liquid chemicals, gases and oil products. Vopak operates 84 terminals with a storage capacity of nearly 30 million cu m in 31 countries.
At Sadaf, Sabic and its JV partner Shell plan to deepen their relationship locally and abroad. At Yanbu, the kingdom’s other industrial miracle, the Red Sea Refinery will see investments reaching $150 billion before all its stages are completed in early 2014. Current production is 400,000 barrels per day. Output from the refinery will keep the sea lanes busy as most of the refined oil will be exported.
By the end of 2011, $33.6 billion was invested by companies in both phases 1 and 2 of Yanbu Industrial City, globally recognised as a hub for the transshipment of crude oil and the manufacture and export of hydrocarbon and petrochemical products. At Yanbu 1 there were 85 companies in operation in the categories of primary, secondary and light industries and 44 other companies under construction or in the design or proposal stage. There was no clear indication how many of these companies have come on stream.
At the same time in Yanbu-2, there were 15 registered companies and six had begun operations including Saudi Aramco’s lube oil refinery; Cristal, which makes titanium dioxide; Al Yamamah Steel, producer of steel billets and bars, and Al Hamrani Fuchs, manufacturer of lubricants. Idea Polysilicon Company (IPC) and Centrotherm Photovoltaic have signed up to build the largest facility in the Middle East for the manufacture of high-quality polysilicon and wafers for solar panels.
Centrotherm Photovoltaic is the world’s leading technology and equipment provider for the photovoltaic industry. The plant to be built in Yanbu-2 at a cost of SR4 billion will produce high-purity polysilicon with total annual capacity of 2,500 tonnes for conversion to solar wafers. The Idea plant will be yet another enterprise toward Saudi Arabia’s industrial diversification away from oil and the hope is that in time it will diversify to produce solar cells and panels and establish solar power plants. To start with the venture is expected to generate 1,000 jobs.
China’s Sinopec Shanghai Engineering Co (SSEC) is building a new 420,000 tonnes per year polyethylene terephthalate (PET) plant in Yanbu for Arabian Industrial Fibers Co (Ibn Rushd). SSEC is a subsidiary of China’s state-owned oil and gas group Sinopec, while Ibn Rushd is an affiliate of petrochemical giant Sabic.
The plant is in the final stages of construction. Once completed, Ibn Rushd’s annual PET capacity will more than double to 750,000 tonnes from the existing 330,000 tpy.
Meanwhile, Ibn Rushd debottlenecked its aromatics and purified terephthalic acid (PTA) plants, resulting in annual aromatics production capacity more than doubling to 1.2 million tonnes from 560,000 and annual PTA capacity also more than doubling to 750,000 tonnes. Samsung Engineering of Korea has announced that it has been formally awarded the Yanbu refinery expansion project by Luberef (Saudi Aramco Lubricating Oil Refining Company). The deal is worth $871 million. And National Petrochemical Industrial (Natpet) and the US’ A Schulman plan to build a 100,000 tpy polypropylene (PP) compounding unit in Yanbu, said the Saudi firm’s parent company, Alujain.
In Yanbu, the $5.3 billion Yanbu National Petrochemicals Co (Yansab) with an annual production capacity of 4 million tonnes of petrochemicals is already in operation. Two new refineries are in the pipeline too, one each at Jubail and Yanbu.
However, much of the petrochemicals and refined crude products produced in Jubail and Yanbu is primarily destined for export. Dr Alaa says he is keen to see more value add industries move closer to the production hubs.
“The RCJY is indeed keen for more of the intermediate feedstock’s produced at Jubail and Yanbu to be used on site. The RCJY made a study on the existing products and decided that it would be economical to have more downstream industries that use the output of primary industry.
Both Jubail and Yanbu master plan review exercise has been currently undertaken and a part of this work is to review the current feedstock profile and make the needed adjustments in the industrial profile.”
He also says there was mounting interest and increasing government support for adding as much value as possible to petroleum products domestically. “The cities are set to lead the country’s industrialisation agenda for many years to come.”
“In fact, this success prompted the Royal Commission to launch Jubail 2 and Yanbu 2 in 2006 to meet projected demands in the coming decade,” Dr Alaa says.
But Saudi Arabia much like the entire Gulf region has a booming petrochemical industry owing to cheap feedstock. Ethane, when available, costs about $0.75 a million BTUs, compared with a much higher cost elsewhere in the world. There is an increased interest in alternative feedstock such as propane, butane, natural gasoline and naphtha. The cost of these products is based on international prices, but with the handling and shipping costs removed, industries still gain a reduction of about 30 per cent by being based in Saudi Arabia.
With all of these advantages, Yanbu and Jubail are unsurprisingly at the heart of petrochemical production.
“The impact of Jubail and Yanbu’s influence on the petrochemicals market will no doubt continue to grow.” Dr Alaa says. He further explains that Jubail and Yanbu being one of the world’s lowest cost production sites doesn’t hurt.
However the RCJY is not sitting complacently with the cheap feedstock, they have developed the cities infrastructure exponentially to keep the competitive edge. Comprehensive planning, engineering, design, and construction work in infrastructure development was carried out to prepare undeveloped sites for Yanbu industrial city development.
Earthmoving was the initial step in the Yanbu infrastructure development program. The land was levelled, graded and compacted to provide stable surfaces for construction. More than 80 million cu m of soil were relocated for that purpose. Yanbu’s primary and secondary industries utilise seawater to cool plant process operations. Yanbu is served by a modern airport. It also has the King Fahad Industrial Port.
This modern KFIP port extends along approximately 19 kilometres of the Red Sea coastline, and is the largest oil shipping port on the Red Sea.
“RCJY was able to move forward from developing infrastructure to be able to build industrial cities and infrastructure become part of it, and RCJY now is moving forward to build shared services for Industrial projects,” says Dr Alaa. With these infrastructure developments, the twin cities are further diversifying to become the global plastic hub.