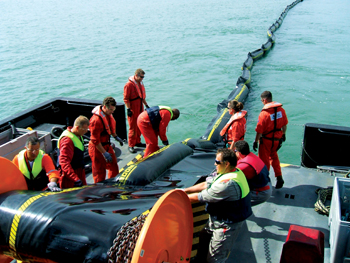
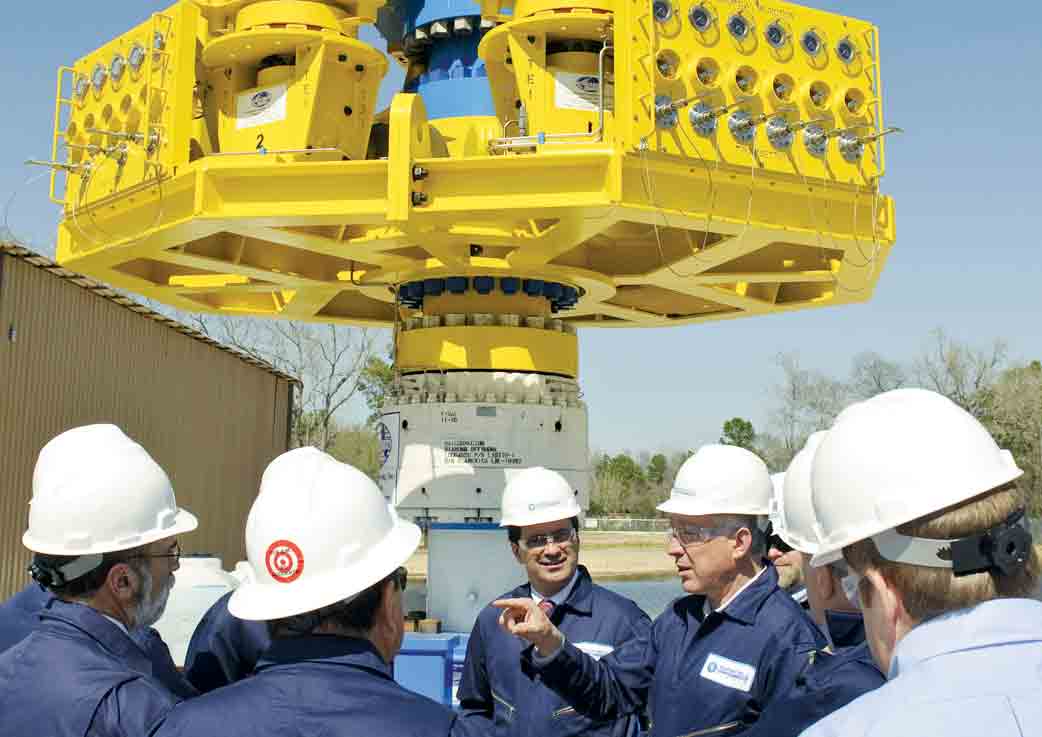
The oil and gas industry has moved past the Macondo tragedy equipped with better technologies to bring ever-deeper discoveries on stream amid much merger and acquisition activity.
The ecological, financial and emotional fall-out from the Macondo catastrophe was enormous. But learning and healing are well underway five years later. Regulatory agencies have been overhauled to better monitor industry activity. New technologies have come to the fore that make deepwater drilling safer. Consortia have been formed to develop spill response and containment strategies.
And studies are underway to measure the impact of the spill on the environment and suggest procedures going forward. Perhaps the most exciting news is the response of E&P companies who tolerated a drilling moratorium and a lengthy permitting process and are now exploring and developing this world-class province with a vengeance.
OILSPILL RESPONSE TOOLKIT
When it comes to oil spills, prevention is the obvious key for the energy sector. But when operations go wrong, preparation and having proper procedures, people and equipment ready are critical.
The Deepwater Horizon tragedy ushered in a new era for oil spill response preparedness. In the five years since the gas release and explosion, industry players have stepped up response efforts, deploying new technology such as an expanded containment system, enhanced capping stacks and remote sensing surveillance.
Still, challenges remain, as operators move farther and deeper into the GoM and HP/HT environments, creating the need for equipment capable of handling emergencies in such conditions.
“Nobody ever wants to make that phone call to us because something has gone wrong,” says Judith Roos, vice president for marketing, customer services and corporate relations for Marine Spill Response Corp (MSRC). “But it is so important to be prepared for response just like you take preventive measures at home to make sure you’re safe. When you do have to call your local fire department, it’s a great comfort to know that they have the right tools in their toolkit.”
MSRC was the largest surface response contractor for BP during Deepwater Horizon, providing 12 responder-class vessels, Roos says during an event in Houston. With conventional response capabilities that include open-ocean mechanical recovery, controlled burning and aerial dispersants, MSRC’s oil response toolkit includes responder-class oil spill response vessels (OSRVs), dual-purpose oil spill response barges and fast-advancing encounter systems in addition to skimming systems and containment booms. The 15 responder-class OSRVs now have dual-option recovery systems.
The MWCC containment system combines equipment from the company’s previous Interim Containment System and the Expanded Containment System. The system includes two modular capture vessels; enhanced subsea umbilicals, risers and flowline equipment; three capping stacks; and ancillary equipment.
“We have the ability to use a Transrec skimmer in a J configuration with boom off the starboard side of the vessel,” she says. “We’ve also modified the vessel to be able to use Buster technology, which allows you to go through the water at a higher speed of advance (3 to 5 knots) thus encountering more oil. It’s very difficult to use this type of technology, though, in a highly debris-laden field.” So having both options available is a plus.
In the last three years MSRC has focused on remote sensing. Following Deepwater Horizon, the company conducted a study, and the key takeaway was that there were challenges with visual spotting of oil.
“You can have a very, very experienced spotter, but the human eye is only able to see so much on the water surface, with a lot of opportunity for chasing false targets,” Roos says. In response, “We have established a level ABC remote sensing system.”
Level A: Aircraft Ocean Imaging Corp, which provides wide-area spill detection, thickness interpretation and oil distribution mapping using multispectral/thermal infrared (TIR) cameras;
Level B: Balloon Maritime Robotics, which provides a battery-powered, non-wired tether with up to 12 hours of hang time using TIR and high-definition cameras; and Level C: Close-in or ship-mounted systems that use X Band radar and TIR to detect oil.
“It really helps. You’ve got somebody in the plane. They are looking not just with their eyes but also with a computer screen that helps them direct the assets to potential targets,” Roos says. “You can also track moving oil with it, another advantage because that is always part of the challenge.”
Advances also have been made below the surface. These include Marine Well Containment Co.’s (MWCC) expanded containment system.
“The new expanded system gives us capabilities to cap a well or cap and flow a well at deeper water depths,” MWCC CEO Don Armijo says. “It also gives us the capability to handle, in the event of a cap-and-flow situation, much more fluid.”
“At the end of last year, we added to our arsenal what we call the subsea containment assembly-our newest capping stack-which is part of the expanded containment system,” Armijo adds. “This particular stack allows us to cap or cap and flow a well at water depths up to 10,000 ft (3,050 m).”
The 15,000-psi capping stack, which stands about 8-m (26-ft) tall including the lifting gear and weighs 100 tonnes, can handle temperatures of 177 C at pressures up to 15,000 psi.
This technology came after MWCC introduced in June 2013 a smaller capping stack suitable for platforms with much tighter well spacing such as tension-leg platforms. The 10,000-psi capping stack is MWCC’s smallest stack. Additionally, the company has a single ram capping stack, which is rated for 15,000 psi and capable of handling fluids up to 177 C (350 F).
“A key feature of our mission is to stay current or ahead of the game with respect to requirements as our members drill deeper in the US Gulf of Mexico. As members find reservoirs that are higher pressure and higher temperature, we need to stay current with technology so we can support them with drilling permits,” Armijo says. “We’re working now on developing a 20,000-psi capping stack to handle higher pressure reservoirs.”
Work started this year for the 20,000-psi capping stack project, which has a two- to three-year development timeline.
“I’ve been in the business for 32 years. When I reflect back to Macondo and movement the industry has made with the creation of MWCC, the industry is better prepared to handle an event,” Armijo continues. “We’re more experienced now and as an industry have learned from Macando.
We’re ready with the right people, processes and equipment necessary to respond and effectively handle another incident like Macondo.”
MWCC is equipped with a reservist team of about 100 people, employees of Wood Group PSN, who are deployed to operate the modular capture vessels, which capture and process well fluids during a cap-and-flow response. Each member undergoes extensive classroom training, drills and other on-the-job training on the modular capture vessels to ensure their readiness and effectiveness during response operations.
“It’s all about being prepared and having the proper training; this includes having the right people and processes and dedicated equipment, which is being maintained and tested to ensure operability when deployment is necessary,” he adds.
The focus of the Center for Offshore Safety, formed following Deepwater Horizon like the MWCC, is on good response planning and identification of hazards as well as effectively managing change as the project unfolds, said Charlie Williams, executive director of the centre.
One of the key areas that people have focused on is finding the oil spill and getting there quickly. “There has also been a lot of work on technology that is even more effective at cleanup,” he adds. “But a lot of focus has been on this ability to find the oil spill and assess it in all kinds of weather and at night.”
Other advances since April 2010 have included bigger, more effective barges with greater boom deployment; skimmers that can remove a larger percentage of oil; and smaller, quicker response vessels, he adds.
“I think there were many people that were well prepared before Horizon,” Williams says. “BSEE has required a lot of new things, including new ways of calculating how big a response you need.” The federal agency also has become more specific on what type of equipment must be deployed and the deployment plan itself.
Companies, at times working with BSEE and the US Coast Guard, have taken part in response planning and drills in significant detail, he says, adding “I think the detail with which people understand the plan both in companies and in the government has improved.”
A key part of planning is ensuring that the workforce is correctly trained, Williams continues: “but even more than that is to ensure that they are ready to respond, respond effectively and respond in the right way. We’re really on a journey of continuous learning and improvement on how to identify hazard spill barriers and build better response and other kinds of plans.”
caption: The MWCC containment system combines equipment from the company’s previous Interim Containment System and the Expanded Containment System. The system includes two modular capture vessels; enhanced subsea umbilicals, risers and flowline equipment; three capping stacks; and ancillary equipment.