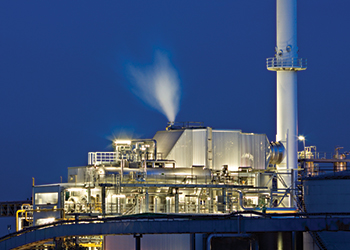
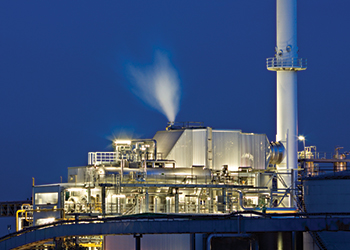
By establishing an integrated olefins optimisation process, petrochemicals companies can maximise profitability from the plant, furthering operational excellence from design through production, says Ron Beck, engineering director, AspenTech
Achieving excellence in the ethylene industry is an important strategic goal for many companies. The US is an existing net exporter of ethylene derivatives and the volume is only expected to increase significantly in the future.
With the combination of low cost Middle East producers, the chemicals industry might experience turbulence in other regions that use crude oil to produce these products. Intense competition could result in less profitable operations closing down and also lead to trade embargoes by some countries aimed at protecting locally-produced products.
The Middle East ethane production chain is predominantly centred on Saudi Arabia. Petrochemicals margins in Saudi Arabia continue to be strong and are continuing to improve. There is continued demand in external markets. The country will continue with its petrochemicals development programme, building local demand and by focusing on intermediate chemicals, including adding 75 000 tonnes per year (tpy) of ethylene glycol, 420 000 tpy of polyethylene terephthalate, 200 000 tpy of paraxylene, 100 000 tpy of linear alkyl benzene and 6,000 tpy of polysilicon.
The sector is not expected to see huge increases in basic petrochemicals capacity until the 2016 – 2018 period, when 3 million tpy of ethylene capacity, as well as substantial downstream facilities, are due to come online.
Irrespective of the US shale boom, the Saudi petrochemicals sector is upbeat due to export growth. Moreover, price stability is expected for producers in the near future as the market looks to further capacity growth longer-term.
However, there is no doubt that the shale revolution and associated addition of new ethylene capacity in the US will put both price and supply pressure on Middle East suppliers. Another key influencer on this region will be the potential for increased self-sufficiency in China and India, which is likely to result in a downward pressure on prices.
The oil and gas companies of the US are benefiting from the exploitation of shale gas, which is reducing the country’s natural gas and natural gas liquids (NGL) costs. This places the US at a natural advantage over other regions, such as Europe, where governments and businesses are yet to establish their strategy on shale.
Europe has a more limited supply of ethane. Indeed, most of its ethylene capacity is produced from naphtha (an intermediate refined form of crude oil). This is much more expensive than the Middle East ethane-butane mix and the US shale gas ethane.
For many chemicals companies, the effect of US shale gas globally has been to decrease the costs of both raw materials and energy. Sasol, ExxonMobil Chemicals, BASF and the Dow Chemical Company, for example, are all chemical giants looking to expand ethylene and downstream chemicals production through greenfield projects and to take advantage of cheap ethane, which is a preferred feedstock in ethylene manufacturing.
Industry experts estimate that the US chemicals industry will continue to invest billions of dollars in ethylene production and increase capacity significantly by over 30 per cent. These investments will yield significant returns and the US could become stronger on the global stage as it positions itself as a low cost provider of energy and feedstocks to the chemicals industry.
Beck ... the use of advanced and integrated technology is essential
to commercial success in today’s market
ETHYLENE OPTIMISATION TECHNOLOGY
The use of advanced and integrated technology is essential to commercial success in today’s market. Data collection throughout ethylene plants, for example, is vital for analytics and optimisation modelling. In terms of optimising operations, the key technologies include offline optimisation modelling, real time optimisation and advanced process control.
All of these have a very strong value proposition in ethylene and work extremely well with the level of data collection in assets across the globe. Benefits of these include energy optimisation and improved production yield and profitability.
With regards to optimising the facility, the way an ethylene plant is engineered is critical across the lifecycle. Simulation models of the entire process are used widely by leading ethylene producers to address operating inefficiencies and to debottleneck.
The interaction of heating and cooling units with crackers and other process units is also crucial and cutting-edge integrated technologies, such as AspenTech’s Activated Exchanger Design and Rating (EDR), are used by several leading ethylene producers to achieve yield improvements.
In the safety arena, dynamics analysis looks at plant upset conditions and some breakthrough pressure safety device design and rating in Aspen Plus enables fire analysis scenario calculations, which account for latent heat and temperature change and rupture disk sizing. All functionality improves chemical operators’ compliance with API 520 and 521.
Leading planning and scheduling solutions enable olefins producers to also select optimal feedstock based on operational conditions and demands, thereby extracting maximum value from the available options.
Companies deploying aspenONE Planning and Scheduling for Olefins are able to generate bottom-line benefits ranging from $6 – $13MM per year with payback in months instead of years. By running the right feedstock, operating with best practices and increasing throughput through improved asset utilisation, companies gain the competitive advantage to sustain significant economic value.
Advanced Process Control (APC) technologies enable companies to improve product quality, reduce energy and raw material usage, grow overall operational efficiency and increase throughput while maintaining safe and reliable operation.
Besides these typical benefits, companies are finding the increased agility provided by APC can also help them adjust to changing economic conditions. AspenTech’s APC solution enables companies to make the whole plant more energy efficient by ensuring that operators have enhanced control over the operation.
THE OUTLOOK FOR ETHYLENE OPTIMISATION
Ethylene producers today are among the leaders in making use of optimisation technology to achieve low cost and high yield production. Organisations such as Saudi Aramco, Dow, LG Chem and Sinopec stand out in that regard.
However, there are many new opportunities in the area of energy optimisation, where simplification of sophisticated methods will provide immediate benefits.
Other areas include broader access to advanced process control due to the introduction of 'adaptive' approaches where the system can 'repair' and update itself, additional use of scheduling solutions for olefins, optimisation of pollution control and abatement strategies and better safety systems.
The outlook for olefins producers is good, although companies must bring products to market quickly to remain competitive. Advanced software is successfully used in olefins plants and has significantly improved product quality, plant efficiency and resulted in swift payback in short time scales.
Design and operational information is now available anytime, anywhere, and is accessible to key decision-makers for greater collaborative, accurate and efficient engineering. Planners and schedulers can use the latest tools to select the optimal slate and blend of feedstocks that will enable them to maximise output while maintaining product quality to meet demand.
By establishing an integrated olefins optimisation process and utilising best-in-class process optimisation software, petrochemicals companies can maximise profitability from the plant, furthering operational excellence from design through production.