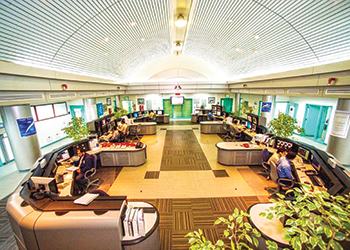
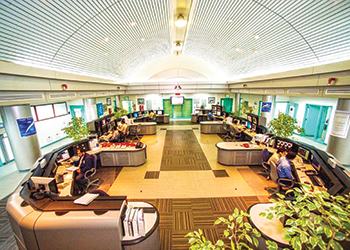
In a unique technological collaboration, Saudi Aramco and Emerson have successfully completed control system cutover at Aramco’s 7 million barrels per day Abqaiq Plants facility, the largest oil processing and crude stabilisation facility in the world
The project, which was commissioned to upgrade and migrate the plants’ existing automation system, was successfully completed with no impact on production, says Majed Al Khalis, control systems engineer in Abqaiq Plants facility, Saudi Aramco. "For a facility of this size, an involuntary shutdown would mean great losses in production and would negatively impact the company," Al Khalis says. "However, by combining planning with methods and technology, the project finished ahead of schedule and under budget. The resulting reduction in man-hours led to cut costs and gave the team more time to observe the new system and close some exception items, he adds.
With the capacity to produce over seven million barrels per day (mbpd), Saudi Aramco’s Abqaiq Plants facility is the largest oil processing and crude stabilisation facility in the world. Abqaiq is the main oil processing centre for Arabian Extra Light (AXL) and Arabian Light (AL) crude oils and produces natural gas liquids (NGL) as a bi-product for Aramco’s daily oil processing activities. To support both the oil and gas plants, Abqaiq Plants produces its own electrical power, steam, instrument air and water.
For a facility of this size, an involuntary shutdown would mean great losses in production and would negatively impact the company. In 2008, Abqaiq Plants team recognised potential challenges were on the horizon. Plants’ existing automation systems would experience obsolescence for distributed control system (DCS) controllers and emergency shutdown (ESD) processors and cards. In addition, these systems would no longer have technical support or training.
After some studies, it was determined that an upgrade and migration cutover was needed of the plants automation system. Abqaiq Plants team began to plan the process of upgrading the existing Emerson Provox DCS, Triplex Regent ESD systems, and burner management systems to the latest release of Emerson’s DeltaV DCS, SIS and BMS. The team began the project in October 2011 with a planned completion date of November, 2015. Although on-budget and on-schedule cutovers at a processing plant of this size do not happen often, the project team completed the cutover activities two months ahead of schedule by end of September, 2015.
LARGE COMPLEX PLANS FOR A HOT CUTOVER
Abqaiq Plants complex has three main divisions: oil, NGL, and utilities. As such, it operates from three control rooms: North (north oil plants), South (south oil and NGL plants), and the UCR (utilities plants). The three control rooms interconnect with several process interface buildings (PIBs) throughout the plants to monitor and control plant processes. The control rooms and PIBs represent the veins of all Abqaiq operations and consist of several networks and risk areas.
Distributed over 20 locations, the project included upgrades to 325 controllers, 105 workstations, and 42 network devices. The team divided the project into four upgrade phases: north oil plants, south oil plants, NGL plants, and utilities plants.
"Success meant not having a single interruption to plant operations, and the team had to minimise the shutdown time for some of the risk areas that have tight operations. As a result of that, a hot cutover approach was chosen," says Al Khalis .
Project team capitalised on three factors to overcome project challenges and complete the project successfully with zero operation impact: human resource development, efficient testing procedures, and streamlined technologies, he says.
HUMAN RESOURCE DEVELOPMENT
Before starting the project, Abqaiq Plants management took proactive steps to develop a qualified team that included a mix of experienced and new personnel across project disciplines including automation, process, electrical, and communication. Several engineers, technicians, and operators were sent to vendor courses to increase their knowledge of the new systems.
TEST PROCEDURES
To assure readiness and correctness of the new system and to achieve a smooth cutover, Abqaiq Plants experienced engineering and operation teams developed testing procedures.Detailed cutover sequence and contingency plan documents were developed to manage cutover critical activities and predict all possible scenarios during cutover and restoration procedures. The team also developed a plan to relocate the old DCS to a temporary cabinet and keep it running to control the plant. This approach helped to optimise the shutdown period for critical risk areas such as AXL Shippers and steam production plants from one week to two hours. It also enabled a fast fallback strategy to the old system, in case of new systems failure.
STREAMLINED TECHNOLOGIES
Project team took advantage of the upgrade project to implement current technologies in the system network, monitoring, and security. These technologies simplified the cutover, project execution, and troubleshooting. For example, zoning and subnets were used to segregate different control rooms’ networks. This segregation of networks and systems into unique areas enhanced system security. It also helped to isolate traffic and errors for easier issue tracing and network troubleshooting. In addition, a centralised management system was used to collect system events and key performance indicators.
Abqaiq Plants team came up with an innovative design to enhance the cutover period of some plant networks through installing a parallel connections to old and new systems’ networks. The innovative idea enabled the team to test the new system while maintaining old system connections. This method decreased plant downtime period from a potential 72 hours to zero and allowed for better system testing and recovery. In addition, to stabilise the plant sooner on the new system, critical loops were tuned with the help of Emerson consultants.
Project team also implemented a centralised patch management system to install security patches and antivirus updates. The centralised patch management system enabled the use of Guardian Support, which provided Emerson technology connections, and ensured project team would discover system issues if any arose. Not only did it help to mitigate Abqaiq system security and patch issues, but it also provided the team insights into what Emerson learned from other sites’ projects.
BUSINESS RESULTS AND LESSONS
By combining planning with methods and technology, the project finished ahead of schedule and under budget. The resulting reduction in man-hours led to cut costs and gave the team more time to observe the new system and close some exception items.
Saudi Aramco employees, Emerson Engineers, and contractors worked together collaboratively with support of Abqaiq Plant management as one team to achieve the goals of the project safely with not even a single negative impact on production.
In addition, the young plant employees have been empowered to lead critical activities.