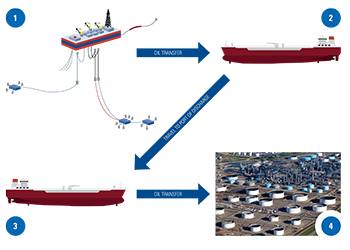
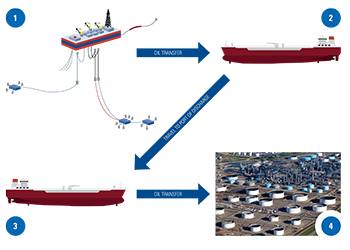
For hydrocarbon producers that offload oil to shuttle tankers, a better understanding of the offshore loading measurement chain enables more control of any losses in the process, says Craig Marshall, Flow Measurement Consultant at NEL
The point of sale for a large proportion of the world’s oil production is outside the origin country where the reservoir was produced. As such, it is measured on systems not subject to that country’s measurement regulator’s direct scrutiny. Any mis-measurement, or increased measurement uncertainty, due to point-of-sale location or the measurement techniques applied, not only impacts the sales revenue generated by the operator, but also the producing country’s government through tax revenue. Without the ability to audit such facilities, there is reliance by producing nations upon rigorous measurement principles and good operating practices being applied by third parties, typically outside of their control.
Typically, this situation is faced when crude oil is not piped back onshore via pipeline but instead is offloaded to a shuttle tanker. The tanker then has the opportunity to access alternative markets to obtain the best price for the product. This is often the case when Floating Production Storage and Offloading (FPSO) vessels are used instead of fixed installations. As of 2016, there is an estimated over 250 FPSOs in operation in the world. Many analysts believe this number will grow by at least 13 units per year even in a low oil price economy. If the oil price were to rise, this number will increase year-on-year with one estimation of 33 units ordered in 2018. Regardless of the exact number ordered it is clear that more and more crude oil will potentially have its fiscal measurement undertaken outside the country of origin.
When crude oil is offloaded from an FPSO or Floating Storage Unit (FSU) to be transported and sold at a port there are four main stages in the measurement chain. During the first stage, produced hydrocarbons are transferred from storage vessels to shuttle tankers. The liquids are measured as they leave the FPSO and then again when entering the shuttle tanker. On board the FPSO, the volume measurement is typically completed dynamically by flow measurement devices such as positive displacement, ultrasonic or Coriolis meters. This is called the Bill of Lading and the quality of the volume measurement is ultimately dependent on the time and effort placed upon it by the operator (there may be underlying drivers on this such as sales/contract agreements or regulatory requirements).
The volume is also measured onboard the shuttle tanker. This measurement is typically completed using a static method; commonly tank gauging. Dynamic measurements can also be used here and are sometimes used as a check against the static methods.
Once filled, the shuttle tanker heads for the port of discharge to unload the cargo to an onshore terminal. During this transit, the volume of oil can change in either apparent or real losses. Apparent losses are likely to be from mis-measurements whereas real losses can be from factors such as evaporation. At the terminal offload, the liquids are measured twice during this transaction; once as it leaves the shuttle tanker and again at the onshore terminal. The mechanism for volume measurement can vary from port to port but most commonly a static method is used. Some terminals operate dynamic meters as check devices for cargo offloading.
![]() |
Craig Marshall, NEL |
At these four measurement points the bulk cargo volume, that is, the quantity of the fluid transferred is measured. However, the calculation of the bulk volume of dry oil transferred also requires an assessment of the quality of the cargo. Without this measurement the levels of water and sediment cannot be quantified and the volume of dry oil in the cargo is unknown.
The most typical method for determining the quality of the cargo is by using in-line sampling equipment; either automatic or manual. This method introduces its own uncertainties such as mixing, sample probe design, number of samples; essentially the representativeness of the samples of the whole cargo.
Once taken, the samples are usually analysed in an offline laboratory where the water and sediment content are determined and the physical properties of the liquids are measured. Using these values the gross and net standard and actual volumes and mass can be calculated.
In order to maintain confidence in the measured values, common methods are in place that can be applied across the measurement chain. In the upstream oil and gas industry, it is common place to have measurement technology calibrated or verified on a regular basis against a traceable standard, complete independent audits over the measurement system in order to highlight any non-compliance, and finally have a constantly evolving calculation of the estimate of measurement uncertainty.
Dynamic flow meters are regularly taken out of service and sent to an accredited laboratory for calibration. This provides traceability through physical measurement standards and through written standards and guidelines. In general, the techniques for laboratory calibrations for dynamic flowmeters are well known and understood. However, as holders of the UK National Standard for flow measurement NEL can offer advice and technical expertise in this area.
NEL is a world-class provider of technical consultancy, research, testing, and flow measurement services to the energy and oil and gas industries, as well as government. NEL, part of the TÜV SÜD Group, is a global centre of excellence for flow measurement and fluid flow systems and is the custodian of the UK’s National Flow Measurement Standards. It provides services in key areas including measurement consultancy, meter development and calibration, erosion, environmental, CFD modelling, training and knowledge transfer.
Sometimes meters are calibrated in situ in a process known as proving. This is where a pipe prover or similar is used in operation to validate the meters performance under operating conditions. A second dynamic flowmeter can also be used in proving. This is called a master meter and is typically positioned in series with the duty meter but is not exposed to the flow during normal operations – reducing flow induced errors (common mode) as far as reasonably practicable.
Commonly, calibrations/verifications can be witnessed by independent third parties to add additional independence and impartiality to calibration results. This adds further confidence to measurement results during service.
Audits of measurement systems are also conducted where an independent company reviews company processes and procedures both in operation and electronically to look for errors or where improvements can be made. An audit can be completed over a few days and are often completed once a year. They add confidence to the entire process, not just the meter performance but the associated calculations, conversions, analysis and data storage and transfer mechanisms.
Calibrations and audits go a long way provide evidence for numbers found in uncertainty budgets for measurement systems. These uncertainty budgets combine the perceived sources of uncertainty for the system and provide an estimation of the confidence in the measured result. These budgets show how the different measurements are combined to provide the final measurement uncertainty of the system and provide a good assessment of the expected performance of the measurement devices. However, this is only true if the values for sources of uncertainty found in the budgets are realistic. Calibration and audit data can provide these realistic numbers and show how a combination of the three techniques provides additional confidence in the final measured value reported.
These processes add confidence to the measured result and can provide the hard evidence to back up any mis-measurement challenges made. In particular, the calculation of uncertainty is extremely valuable in assessing any measurement discrepancies found as if it is not comparable to the other measurements then the confidence in the result will be low. For instance, for a single cargo offload of 100,000 cubic m, an increase in uncertainty of 0.5 per cent could be worth as much as over $200,000 in financial
exposure alone.
The quantity and quality of the cargo transferred are measured at each stage in the measurement chain resulting in multiple measurements of volume, water content and physical properties of the fluids to be compared and any losses calculated. This allows for monitoring of the cargo at each stage of the process.
Any significant changes between subsequent measurements can be spotted in this way and the appropriate action taken. For instance, a discrepancy in water content between transfers potentially indicates a problem with sampling of the cargo. However, this depends on the quality and confidence of the measurements made and relates back to calibrations, auditing and uncertainty budgets. An example of some loss terms and locations can be found in the table.
Loss control is important to the producer/operator as it allows for the volume tracking of bulk crude oil across the transport chain and provides evidence to challenge any sales values at the Outturn found at the port of discharge if they are suspected to be inaccurate. Without accurate measurement at the preceding stages in the measurement chain, particularly at the Bill of Lading, the operator would not be able to say if or when any major losses occurred.
It is, therefore, in the best interests of the operator, and the government, that the Bill of Lading measurement uncertainty is of equal or better uncertainty than can be expected from
the Outturn.
It is important to stress that there is no specific measurement error when the point of sale of crude oil is outside of the origin country, only a reliance on third party measurements that do not fall under the origin country’s scrutiny. Operators then rely on good measurement practice and similar measurement regulations to be in place.
A better understanding of the whole measurement chain will enable more effective control of any losses in the individual stages in the process and will result in greater confidence in the value of hydrocarbons produced both for the operator and taxation authorities.