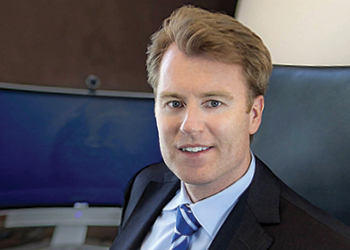
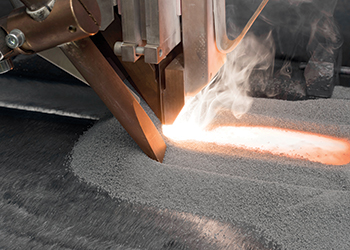
Focused on filler metals, voestalpine Böhler Welding offers extensive technical consultation and individual solutions for industrial welding, cladding, hardfacing and brazing applications in demanding industries such as oil and gas upstream and downstream.
With three specialised and dedicated brands – Böhler Welding focusing on joint welding, UTP maintenance on repair and maintenance and Fontargen Brazing on brazing consumables -- it is excellently poised to satisfy the requirements of its customers and partners in over 150 countries.
The company’s application technicians and welding engineers render valuable onsite support to customers around the globe. This outstanding service includes product and technical consultation, process optimisation advice and training courses for customers in all branches of industry, says a company spokesman.
This customer focus is also reflected in research and development, which is driven by industry and customer requirements. For the oil and gas upstream segment a complete range of best-in-class consumables tailored to industry-specific requirements is available, he says.
The product range covers the strength and impact requirements, including CTOD, for ABS structural offshore steel grades up to ABS EQ70 and comparable qualities used for offshore structures, such as fixed platforms, jack-up rigs, SPARs, semi-submersibles, FPSOs, FPOs and FPUs.
An example is the range of filler metals with <1 per cent nickel in their all-weld metal composition to comply with the NACE MR0175 requirement for SSC safe service in sour environments. Consumables for hydrogen-critical applications fall in AWS-class H4, and are protected by special moisture-tight packaging to prevent hydrogen-induced/hydrogen-assisted cracking. A highlight in this product range are Böhler Welding’s seamless cored wires, offering the best protection against hydrogen reabsorption in flux-cored arc welding (FCAW).
The company’s product programme covers all materials used for subsea production equipment, such as drilling strings, casings, BOPs, Christmas trees, manifolds and risers, and for pumping, compression and separation of raw oil and gas.
These include stainless steels (austenitic, martensitic, duplex and super duplex), Ni-base alloys, non-ferrous materials (copper, nickel, aluminium, titanium), weld cladding with corrosion and wear-resistant alloys using all main welding processes (SMAW, GTAW, FCAW, SAW and ESW), as well as finishing chemicals for the maintenance of stainless steels.
Meanwhile, voestalpine Böhler Welding is involved in the LNG industry with advanced products and welding procedures for the safe and efficient construction of LNG transport, storage and handling installations.
The range of LNG welding consumables covers all main arc-welding processes and construction materials commonly used in the fabrication of LNG installations, such as 5–9 per cent nickel low-temperature steel, austenitic stainless steel, dissimilar joints, nickel-base alloys and aluminium.
PIPELINES
Pipeline construction material specifications play a crucial role in the success and integrity of on and offshore pipeline construction, especially in low-temperature and sour-service applications.
Voestalpine Böhler Welding offers a full range of cellulosic and basic vertical-down and vertical-up electrodes, as well as solid, flux and metal-cored wires for semi-automatic and fully mechanised welding, self-shielded flux-cored wires, and submerged arc wires and fluxes for steel grades up to X100.
Consumables for martensitic, austenitic, duplex and corrosion-resistant alloys (CRA) are readily available. NACE and CTOD tests have been carried out with a wide range of its products.
The company’s global quality and HSEE function ensures the implementation and maintenance of a multisite management system comprising ISO 9001, ISO 14001 and ISO 45001.