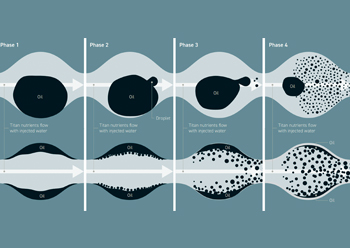
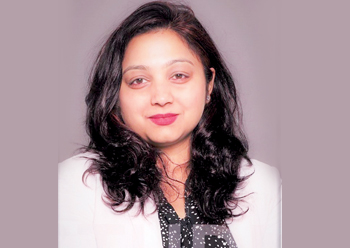
The steam flooding EOR technique becomes less efficient with time, but utilising data acquisition combined with analytics can help make holistic and well-informed decisions, thus maximising oil recovery, says Aarti Dange, MEA Business Development Manager – Digital Transformation, Emerson Automation Solutions
Brownfields often suffer from higher Opex, production decline, aging equipment, and constrained resources. This is when companies plan for enhanced oil recovery (EOR), which is best suited for the reservoir type as well as depending on available resources.
According to the US Department of Energy, there are three primary techniques for EOR: thermal recovery, gas injection, and chemical injection. The EOR aims to have a recovery of around 45 per cent OOCIP (original oil in place). However, it is challenging to have the highest possible efficiency with the changing reservoir dynamics without the use of sophisticated technologies. This article discusses the use of various digital technologies specifically for thermal recovery with applications and relevant case studies.
Thermal recovery (and specifically steam injection) is arguably the most successful technique for enhancing oil recovery implemented to date. Focusing on the Middle East, the Lower Fars Heavy Oil Development Project in Kuwait was publicised to cost $7 billion in utilising thermal recovery.
PDO in Oman collaborated with Glass Point Solar to build the largest solar thermal project. The heat energy helps in lifting the heavy oils by reducing viscosity, improving producibility substantially, and shifts rock wettability.
There are several techniques of injecting steam inside the wellbore and one of these is continuous steam injection, popularly known as steam flooding. Steam is introduced through injection wells and is driven towards oil to physically displace it while heating it to reduce viscosity. Steam floods require continuity in the formation to allow steam to drive oil toward the production well. Also, this method requires a large amount of steam to be injected than other methods.
Economic challenges are one of the limiting factors in using steam flooding. The fuel consumption per barrel of oil produced is high, making it a relatively costly method for oil extraction. When steam injection begins for the first time, one barrel of steam injected can recover up to 30 barrels of incremental oil. After some time, the efficiency of the process drops, and one barrel of steam is only able to recover about 0.2 barrels of incremental oil. The challenge here is to maintain high operational efficiency to keep the process economical yet have maximum efficiency.
The first important requisite is to understand the production volume and ratio of oil, gas, and water produced from each well in real-time. This needs to be compared and matched with what is modeled. With non-intrusive, wireless wellhead monitoring, it is possible to facilitate seamless data acquisition and communication to the control room.
Emerson’s WirelessHART and remote terminal units with ControlWave Micro technology were solutions chosen for the steam flooded oil wellhead monitoring and control. The ControlWave Micro RTU auto-detects the WirelessHART devices as they get added to the network, eliminating the need for any site survey, bringing down startup costs and time.
The non-intrusive wellhead instruments eliminate the high cost of trenching, laying conduit, and pulling cables. The wireless solution can control steam injection into the wellhead automatically without involving manpower. The field instruments collect information to help monitor and analyse the indicated work statuses and trigger maintenance notices when applicable.
The steam generation equipment involves OSTG (open-source technology group) or HRSG (heat recovery steam generator) and turbines that are susceptible to failures and requires frequent maintenance. At the same time, fuel optimisation is the key to ensure good ROI for the steam flooding process.
With Emerson’s suite of advanced analytics utilising machine learning, extensive failure modes and effects analysis (FMEA) library, mapped root cause analysis (RCA’s) and systematic online action modules can not only analyse the performance of the rotating and critical equipment but can also predict the failures before time and provide actionable insights for increasing the performance efficiency.
The energy and fuel optimised workflow is also crucial for Opex and environmental reasons. Emerson offers applications such as smart boilers that optimises the combustion for stability, response, efficiency, and use of optimised cost fuel. Hence, these workflows extend further into the mechanical, reliability, and safety space than with a conventional oilfield.
The "huff and puff" method or cyclic steam stimulation is a method of alternating injection of steam and production of oil with condensed steam from the same well or wells. Specifically, in cold regions producing heavy crude, it is a challenge to optimise the cycles and ensure that the energy induced in the reservoir is utilised to the maximum, facilitating continuous production. Because of the weather, it is important to check the temperatures at various points within the flowline to ensure the flow.
From an optimised perspective, it’s important to have process temperature data at various points from the wellhead to the manifolds and beyond. For an operator in Canada, Emerson’s non-intrusive process temperature measurement device, popularly known as X-well was utilised.
The sensor was used to measure – oil not flowing under 300 deg F, oil between 300-350 deg F, and steam bypass from the well above 400-500 deg F. This data helped to optimise the cycle time and rate of injection to the best.
The customer decided to use the X-wells due to the accuracy and as they could utilise an already existing wireless network thus transmitting the complete wellhead measurement seamlessly to the control room. The use of X-wells reduced maintenance intervals, facilitated easier maintenance utilising less labour with no process shutdowns for calibration or inspection. This brought down the operational costs increasing the convenience for process temperature measurement. By eliminating the insertion into the flowlines, the leak points get eliminated, significantly increasing the accuracy.
Another important consideration especially in thermal extraction is the integrity of the asset including equipment, flowlines, and pipelines. The produced water makes all the relevant asset components susceptible to a high corrosion rate, constraining the production from the wells due to the fear of failure.
Emerson’s complete portfolio of corrosion and erosion monitoring solutions helps in gauging the risk and the impact of corrosion, thus providing the reality check for the asset health.
Emerson’s non-intrusive, UT-based corrosion monitoring device indicates the onset of corrosion. With the analytics software added, it predicts the remaining useful life of the flowline and helps in scheduling the maintenance accordingly. This is a way of digitalising the manual inspection rounds especially in trying weather and unsafe operating conditions.
The Capex associated with these projects is greater, as is the Opex, and the risks associated with loss of containment are both higher and more varied, with greater consequences. Through the use of digital technologies, it is possible to achieve intelligent EOR processes. The data acquisition combined with analytics help in making holistic and well-informed decisions. Emerson’s digital ecosystem not only provides tools to achieve the top quartile performance but also helps build a roadmap for bringing efficiency, safety, and reliability.