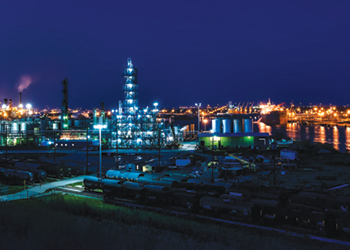
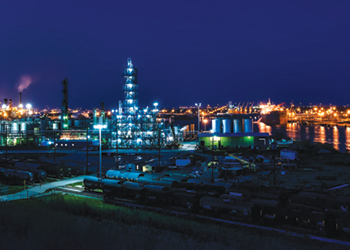
Hybrid models are making it easier to create and run large models for refinery-wide assets, integrated oil to chemicals processes, large petrochemical facilities and more, Gerardo Munoz from AspenTech, tells OGN
Many organisations wait until technology is mature before they adopt it. Yet, across the asset-intensive industries, waiting is no longer an option. Faced with market disruption and intense competition, operators must today seek out technology that offers them the opportunity to drive business agility and enhanced profitability and ultimately competitive edge. They simply can’t afford to delay.
'In this context, the highly competitive oil and gas sector is a case in point. Any operator working in this arena needs to achieve fast time to insight and rapid results. Oil and gas companies are facing growing pressure to be more agile and increase productivity. And engineers that work across the industry need tools to perform accurate calculations more quickly. Examples would include accounting for operations, allocating gas to various sources of production and updating production planning models used in refining operations,' Gerardo Munoz, Senior Product Specialist, AspenTech, tells Abdulaziz Khattak of OGN.
RANGE OF APPLICATIONS
![]() |
AI and machine learning can greatly accelerate the ability to employ plant data |
These complex and deep-seated challenges that the oil and gas sector is facing today can be effectively addressed through a concept known as hybrid modelling, which combines first principles models and domain expertise with AI and machine learning.
First principles models, which draw on decades of use and experience from industry, researchers, and scientists, together with their domain expertise, are well established for their accurate processing of oil and gas industry processes.
To get the final several percentage points of accuracy out of these models, currently plant data is employed to calibrate these first principles models to observed plant conditions and performance, a procedure which also requires considerable time, expertise and experience.
AI and machine learning are rapidly emerging as tools that can greatly accelerate the ability to employ plant data both to calibrate first principles models and to create data-based models of phenomena and processes quickly.
AI can expand the capabilities of experts and has the potential of lowering the expertise bar towards modelling process systems, but it must be combined with domain expertise to create the real-world guard-rails that make it work safely, reliably and intuitively.
Hybrid models combine AI, first principles and domain expertise to deliver a comprehensive, accurate model more quickly without requiring significant expertise.
Machine learning is used to create the model, leveraging simulation, plant or pilot plant data, while using domain knowledge including first principles and engineering constraints to build an enriched model without requiring the user to have deep process expertise or be an AI expert. This next generation of solutions democratises the application of AI within hybrid models to optimally design, operate and maintain assets – deploying them online and at the edge.
AI and machine learning allow us to build a model analysing a broader set of data while leveraging advanced data science techniques for model prediction. When combined with engineering principles and domain expertise, the models can be built and maintained with less time and effort than traditional methods.
In oil and gas, there are a range of exciting applications for this innovative new approach.
PLANT DIGITAL TWINS—DEPLOYING HYBRID MODELS ONLINE
Online hybrid models offer a great advantage in solving time and robustness, while maintaining the same accuracy as a rigorous model. Added to this, they are essential in today’s work environment. Models can represent plants and equipment or can be created for specific properties and KPIs such as compressor power, air cooler fouling, heat exchanger duty, etc.
When combined with data from plant instrumentation, different stakeholders can make more informed strategic decisions for operating the plant and respond to today’s market changes quickly and efficiently.
SIMULATING D-TO-MODEL UNITS
When we combine first principles and AI through hybrid models, it is possible to use data from different sources to easily create models of complex and custom processes and unit operations.
Process data can be leveraged to predict performance of specialised columns, separation equipment such as membranes, or some specialised refinery reactors and processes.
Laboratory data can be used to improve property estimations in existing models.
Coupled with this, pilot plant data can be utilised to create models of new technologies, accelerating proof of scale up economics and commercial viability. These are just a few examples of the many out there in the market today.
HYBRID MODELS AT LARGE SCALE
With the flexibility to model diverse process in the manufacturing industry, hybrid models have multiple value applications. However, scaling these models to large applications can really help with longer-term business objectives, such as monitoring asset-wide emissions or reducing site-wide energy use. Hybrid models are pushing the boundaries of what is possible, and making it easier to create and run large models for refinery-wide assets, integrated oil to chemicals processes, large petrochemical facilities and more.
REAPING THE REWARDS
With a hybrid modelling approach, energy companies can develop accurate models of their processes. These models solve problems much faster than the original ones and are easier to understand, so multiple staff across upstream operators can use them for faster gas allocation analysis. This benefit can be extended as models are deployed for maximised production, energy reduction and sustainability strategies.
A similar example can be applied in refining, where hybrid models can be used to update the planning models through a seamless workflow, saving almost 50 per cent of the time typically used, delivering accurate models that are valid over a wider range of conditions and, conservatively, creating benefits over $10 million per year for a typical 200,000 barrels of oil equivalent per day (BOED) refinery.
While the technology is still developing, we have already seen cases where, combined with plant data, hybrid models have helped plant operators increase yield (by 1-5 per cent), throughput (by 5-10 per cent) or reduce energy demand (5-20 per cent), translating into cost savings and revenue gains running into millions of pounds.
Hybrid modelling is easy to access, use and share which makes it ideal for use at the current time with many oil and gas sector staff working from home. They don’t require high levels of technical understanding of simulation, for example, to adopt and they don’t have to be an AI expert to benefit from using it.
The new approach also helps oil and gas operators balance profitability and sustainability. On the one hand, it can help operators react more quickly, be more agile and make better informed strategic decisions. On the other, it can assist them in saving energy, and tracking and reporting on plant emissions online.
They can run and do an analysis of the whole plant and look at overall consumption, for example. They can drill down and create different modes for multiple assets or processes that traditionally don’t have a good simulation approach. They can create models for a bio processing plant and integrate it into the model for the refinery to achieve better planning and operations optimisation. And they can replicate separation efficiency for carbon capture and comply with emission reduction goals across the asset.
Hybrid modelling is a rapidly emerging technology. Some companies in the oil and gas sector that don’t see themselves as early adopters might see the benefits of the approach but are waiting for it to become fully mature. That would be a mistake as they would miss out on the more immediate benefits the methodology would bring them and the golden moment when technology could bring them real business advantage might easily be missed.
For many organisations, the time is now for hybrid modelling. They can’t afford to let it pass them by.