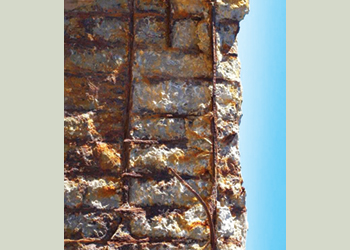
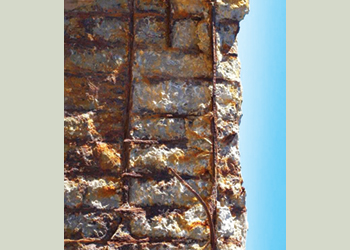
Of the two materials tested for concrete protection at Tanajib Gas Plant, MasterSeal 550 was found to have more advantages over Sigma in terms of activity duration, safety requirements and required resources, Mahmoud Elzayat, Senior Project Engineer, and Nawaf Alubaidi, Project Engineer, at Saudi Aramco tell OGN
Saudi Aramco researchers conducted comparative testing of two materials meant for protecting concrete foundations from water and chemical ingress at the company’s Tanajib Gas Plant, located on the Arabian Gulf coast.
Both Sigma and MasterSeal 550 that serve the purpose of protection were applied.
Being an essential element that holds the building structure, the concrete foundation is endangered by cracks, spalling or delamination. These types of failures could be caused by the presence of chemicals in the groundwater table.
![]() |
Figure 2 ... sulfate attack |
Also, outbreaks of chemicals, such as chloride and sulfate, present in contaminated soil can also reduce the durability of concrete foundations (Figures 1 and 2).
International standards recommend several materials to protect the concrete foundation from chemical attacks without compromising the durability or integrity of the structure.
As per Saudi Aramco Engineering Standard, SAES-Q-001, all concrete surfaces in direct contact with the earth should be coated with two coats of coal tar or bitumen coating.
• Sigma: At the Tanajib Gas Plant project, Sigma C200a (APCS-03) material was used to comply with Saudi Aramco requirements.
Supplied in premeasured units, these were mixed onsite using airless spry machines, such as Smart Blast X-Termr Series and air compressors at 10 bar.
After the curing period, the concrete foundation surface needs to be repaired in case of any defects that might have occurred due to improper formwork installation and removal.
Three layers of Sigma protection material were then applied with six hours of curing in between giving the foundations three additional days prior to backfill.
![]() |
Figure 3 ... Sequence of sigma application activates |
Once the third layer was applied and cured, an inspection walkthrough was conducted prior to giving the clearance to backfill.
The sequence of application (Figure 3) can be summarised as follows: Surface preparation, concrete surface repair, moisture test, Sigma primer (sealer) min six hours, Sigma C200a epoxy (mid-coat brown) min six hours, Sigma C200a epoxy (top-coat back) min six hours, final inspection, and immediately backfilling. These activities took a total of 17 days.
As a rough estimate and based on contractor performance, bitumen application requires around 10 manhours for a 30 sq m surface preparation, and 10 manhours for 60 sq m is required for coating application using Sigma.
Special consideration and requirement was given to safety during the application of Sigma, which is a toxic material. These included use of PPE, outdoor mixing, etc.
• MasterSeal 550: Instead of the specified requirement, the company and contractor recommended using MasterSeal 550 (from BASF) as an alternate for concrete protection at the Tanajib Gas Plant project.
![]() |
Figure 4 ... Application of MasterSeal 550 |
MasterSeal 550 is a two-component acrylic modified cementitious coating that only requires onsite mixing to form the ideal product to waterproof and resurface concrete.
According to the manufacturer, MasterSeal 550 is compatible for use on damp structures and foundation as an alternative to coat tar epoxy and bitumen as a water proofing barrier. An application thickness range of 700-1,000 microns is recommended.
MasterSeal 550 is supplied in a premeasured unit and should be mixed on site in clean containers. The powder is added slowly to the liquid and mixed using slow speed drill Texsprayer Graco RTX 5500 PX without compressor (Figure 4).
In the case of Sigma, surface preparation was made to the concrete prior to application. However, MasterSeal 550 being a cementitious material can be used as a repair material by reducing the time needed for surface preparation.
It can be also be used for newly fresh concrete after formwork removal (one day after concrete pouring) by providing the concrete a good curing as it acts as a curing compound as well.
Based on contractor performance, when using MasterSeal 550, the concrete foundation can be backfilled three days after application in the summers and after seven days in other seasons.
![]() |
Figure 5 ... Sequence of MasterSeal 550 application activates |
This helps boost the activity duration by allowing the contractor to be ahead of schedule in concrete coating and backfilling.
The only consideration during the application is that the applied slurry should be shaded or otherwise protected from direct sunlight and windy condition for a period of 24 hours.
The sequence (Figure 5) of MasterSeal 550’s application can be summarised as follows: Surface preparation, concrete surface repair, MasterSeal 550 (primer) interval time 30 min, MasterSeal 550 (mid-coat) interval time 30 min, MasterSeal 550 (top-coat) interval time 30 min, and final inspection.
Unlike Sigma material, no additional safety requirements are required for MasterSeal 550 application, apart from regular personal protective equipment (PPE) like disposal coveralls, respiratory masks, and rubber gloves.
CONCLUSION
During construction, engineers always look for ways to meet deadlines without compromising on quality and safety by implementing different materials and techniques, especially for projects that need to be expedited.
Of both materials tested for concrete protection at Tanajib Gas Plant, MasterSeal 550 has more advantages over Sigma when it comes to activity duration, safety requirements, and required resources. No special PPE is required for the operator when working with the non-toxic MasterSeal 550.
Additionally, concrete foundations can be backfilled after 3-7 days from MasterSeal 550 material application compared with Sigma, which may take up to 17 days based on contractor performance.
Nawaf Alubaidi is a project engineer working for Saudi Aramco Project Management Team for the past two years. He has executed major oil and gas projects during his experience as a project engineer. Alubaidi has a bachelor’s degree is in civil engineering from Prince Mohammed bin Fahad University, Saudi Arabia.