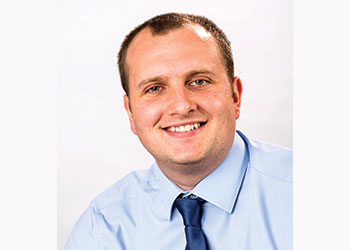
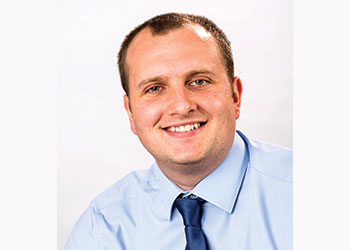
EOR is vital for maximising recovery but understanding the sources of error can help end users of related projects and measurement technologies to mitigate and reduce them, Dr Craig Marshall tells OGN
Enhanced Oil Recovery (EOR) is a method used in oil and gas production to increase the recovery factor of producing oil and gas wells. It involves the use of methods to increase and sustain hydrocarbon production for longer periods through injection of fluids, thermal energy (heat) or chemicals.
Conventional oil and gas production typically relies on reservoir pressure to help drive fluids up the well bore during production. This natural pressure-driven process usually allows for years of production.
But as more and more fluids are produced, the pressure in the reservoir decreases. This reduces the natural driving force and results in lower production rates over time.
This eventually leads to the reservoir pressure dropping below the minimum required to overcome the pressure loss of the production infrastructure and no more hydrocarbons flow.
Depending on the reservoir starting conditions, this could result in substantial hydrocarbons left in the well compared with the original contents, that is, a low recovery factor.
Furthermore, the produced fluids themselves may be partially immobile and require some form of energy to aid production. An example can be seen in heavy oil and bitumen production in Canada.
The in situ hydrocarbons are extremely viscous and steam is used to heat the fluids and reduce its resistance to flow by lowering the viscosity. Chemicals can be used in place of heat in some locations.
Regardless, by increasing pressure through fluid injection or mobility through heat or chemicals, the effect is to have an enhanced recovery of the quantity of hydrocarbons produced over the lifetime of the field.
MEASUREMENT CHALLENGES
![]() |
EOR plays a huge role in extending field life and helping to realise the potential |
The use of EOR techniques can be expensive and it's important to fully quantify the effectiveness of a technique for an application, from both an overall cost perspective and also to ensure it is being utilised optimally.
Accurate flow and physical property measurements of the production and EOR fluids are vital to obtain this information and make correct decisions on production rates.
Common fluids injected to increase reservoir pressure are water, carbon dioxide (CO2), nitrogen and natural gas.
Water can be straightforward to measure and its physical properties are well known over a wide range of temperatures and pressures.
The other fluids are gases and can easily be measured as single phases. Equations of state can be used to calculate physical properties at operating conditions and although they won’t be as accurate as water physical properties, they will still deliver an overall low uncertainty for those fluids.
However, often it’s not as straightforward as that and consideration must be given to where these fluids will come from.
The fluids injected in EOR are typically recycled from the production process and, therefore, are never a pure process stream.
The impurities have a couple of major effects on measurements as they affect the physical properties used for some measurement technologies and calculations, and the phase behaviour at the measurement point or reservoir conditions.
This could include the presence of a second fluid phase, which brings inaccuracies into measurements and also changes in the expected way the EOR method works within the reservoir.
In thermal EOR, the main heat transfer mechanism is injected steam, which increases the mobility of hydrocarbons in the reservoir through reduction of the fluid viscosity. This can be completed as a continuous operation or through cyclic steam injection where hot steam is injected periodically.
The steam is generated on site through boiling water and is typically very pure. However, the quantity of steam is not the only important measured parameter here as the quality of the steam (that is, is it wet or dry steam) can also greatly impact the process efficiency.
Steam can transfer energy to the reservoir through its temperature change (sensible heat) but also its phase change (latent heat).
If some of the steam has already condensed because of the long distance from the central generation point, poor insulation, or some other factor, then there is less energy available to transfer to the reservoir fluids.
This not only makes the whole process less efficient, that is more wet steam is required to do the same work as dry steam, but the presence of a second phase (condensed water) at the measurement point can impact the measurement accuracy. Again, this adds to the poor data collection, which is used to base important decisions on.
Finally, in chemical EOR, various chemicals are injected into the well typically in diluted form to provide a chemical means of improved production. An example is using chemicals that mix with naturally occurring species in the hydrocarbons to produce surfactants that increase mobility.
Another one is injecting polymers with water into the reservoir to produce a high viscosity fluid able to ‘push’ bulk hydrocarbons ahead of it, where regular water would simply mix or break through the reservoir fluids.
The challenge here for measurement is the effect of low Reynolds numbers on measurements and the potential changing physical properties of the polymer mix. These can lead to inaccurate measurements if they are not considered and corrected for.
The chemicals themselves are not recycled from the production process like other fluids and have to be sent to site. They can be very expensive and, therefore, it’s vitally important to ensure they are being used optimally in any EOR process.
In summary, EOR is a vital process to help deliver on maximising economic recovery from any oil and gas well.
Currently, it plays a huge role in extending field life and helping to realise the potential in harder to produce unconventional resources.
Like any application though, the fluids, physical properties and operating conditions must be measured accurately in order to better understand, optimise and control the process and to ensure it is cost-effective.
However, measurements are not without their challenges but understanding where the sources of error can be found will help end users of the EOR projects and measurement technologies to mitigate and reduce them.
* Dr Craig Marshall is a Consultant Engineer at TÜV SÜD National Engineering Laboratory, a world-class provider of technical consultancy, research, testing and programme management services. Part of the TÜV SÜD Group, the company is also a global centre of excellence for flow measurement and fluid flow systems, and is the UK’s National Measurement Institute for Flow Measurement.