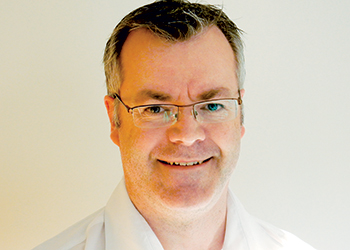
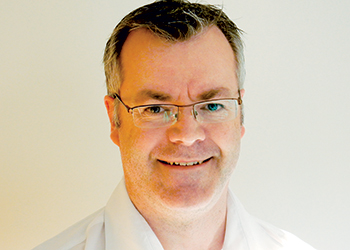
There are numerous trends affecting hydrocarbon producers who are still carrying out upstream operations while transitioning into renewable alternatives, and their concerns focus on the type of digital technology solutions that can help them achieve their goals.
They want to specifically ensure that the skills and knowledge gap is kept to a minimum, and operational challenges are overcome while reducing the environmental impact, in addition to solving the problem of the vast amount of generated data and to prevent it being inaccessible to everyone.
Despite the push toward renewables, the demand for reliable and affordable energy will not go away until renewable sources outsource traditional oil and gas. This will be the trend, at least, for the next 30 to 50 years.
TRANSFERABLE TECHNOLOGY
One way to accelerate the process of transitioning to renewables is through reusing technology and skills from one industry to another.
![]() |
Keystone Engineering leveraged their knowledge in offshore platforms |
An example is the offshore Block Island Wind Farm, one of the first commercial wind farms in the US, which began commercial operation in December 2016.
For the Block Island project, the structural design was carried out by Keystone Engineering, which had built oil and gas platforms to withstand the force of Hurricane Katrina without being damaged.
This knowledge and experience gained gave the firm a key advantage in the design of the Block Island Wind Farm foundation structure by providing a focus on constructability, fabrication efficiency, and reduced installation time.
Here the additional benefits of partnering with Bentley was twofold. Both companies had a long history of working together in the offshore oil and gas industry, as well as expertise in structural analysis for wind turbines. Without this, it would have taken the project much longer to complete without the necessary guarantees of success and resilience.
GOING DIGITAL
One of the main challenges that prevents oil and gas producers from achieving a fully digital solution is the ability to pull together information from many different data silos.
It takes too long to make accurate decisions when teams spend most of their time trying to find the right information and confirm if it is up to date and reliable.
![]() |
Going digital means always having access to reliable and up-to-date information |
The industry needs better solutions if it is to meet the immense challenge of net-zero, and digitisation is simply essential to ongoing operations, and imperative for companies to remain competitive and safe.
Incorporating analytics and machine learning techniques to reliability solutions–such as the AssetWise services that Bentley provides–enables the connectivity, interoperability, visibility, and insights that were previously hidden within these data silos.
These reliability and analytical solutions can provide a variety of use case to help reduce emissions and achieve the net zero goal.
STARTING THE JOURNEY TO NET ZERO
Oil and gas companies are increasingly looking to digital solutions like digital twins, data platforms, and other technologies to move beyond monitoring to emission controls, proving that they are taking a step in the right direction.
One of the first things that operators can do now to reduce their carbon footprint is to optimise their operations.
The first step is to prevent failures that cause equipment to run outside of optimal efficiency, or even cause shutdowns. For instance, pumps not running at their best efficiency not only use more energy, but are also less reliable, both of which lead to a higher level of emissions.
Having a robust asset performance management strategy in place is a must.
An example of how to establish an asset performance management strategy comes from OQ Upstream, an integrated energy company that operates and manages dozens of plants, thousands of assets, and over 4,500 km of pipeline across Oman.
The company digitised its asset performance management activities, and as a result recognised the impact on the reliability growth and the reduction of failures and unplanned downtime. That resulted in a growth of asset reliability while significantly reducing functional failures, unplanned work orders, and maintenance costs.
![]() |
PlantSight combines operational and asset data |
Other ways of optimising operations are monitoring and managing assets more effectively.
Since the process industry generates a tremendous amount of data, therefore, being able to access, monitor, analyse, and report on this data is crucial for achieving optimal asset performance and emission reporting and control.
An example of optimising existing assets more effectively is Cairn Vedanta in India. Using AssetWise 4D Analytics from Bentley, the company captured all well integrity and flow assurance data from over 800 onshore and offshore wells.
It aggregated data from multiple systems into one solution, and by using analytics, created a near real-time picture of asset health and performance.
Having the data helped it decide whether it should continue, retire, or make changes to the well, resulting in improvements to both emissions reduction and costs.
THE ROLE OF THE DIGITAL TWIN
These optimisation techniques, which are often offered as stand-alone solutions, can now be offered within digital twins.
A digital twin is a virtual representation of real-world entities and processes, combining engineering and design data/models, with operational and IT information.
As oil and gas operations become more digitised to improve operational performance, as well as remain competitive and more sustainable, the role of digital twin technology becomes even more important.
Gartner says that by 2024, some 90 per cent of greenfield investments will already have comprehensive digital twin models.
However, what is becoming increasingly important is how organisations keep those digital twins–the complete set of information about their assets, not just models and engineering–up to date and accurate.
How do those organisations connect to their supply chains, maintain an open choice, and collaborate effectively on a global scale? Adopting these practices will define the next five years in the oil and gas and energy industries.
New organisations entering the market will be the catalyst for this change.
The other axis of change will be connectivity between the digital twin and operational and transactional systems.
Overall, digital twins can improve asset operators’ situational awareness and optimise asset performance by modeling dynamic behaviour.
As a focal point system for asset operations, digital twins have the significant potential to improve oil and gas companies’ asset and business performance.
The oil and gas industry is already a leading adopter of digital twins, as evidenced by Shell and its Deepwater Project Delivery Digital Platform.
This project uses a digital twin created with PlantSight to aggregate data from various sources and provide a comprehensive picture of the project, leading to clarity and alignment among the diverse teams working on the project.
CONCLUSION
Technology, such as digital twins, will play a large strategic role in energy transition as it provides the visualisation, context, and the right information at the right time.
Lastly, oil and gas companies need to partner with vendors that have the expertise, domain knowledge, and technology.