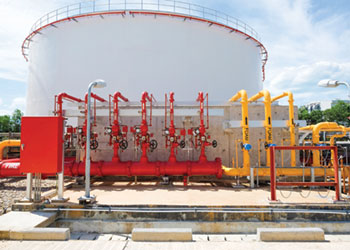
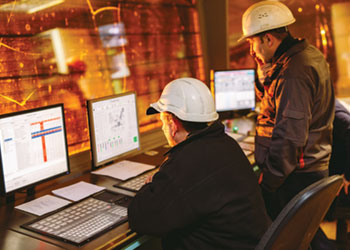
Designing an effective monitoring system is a complex process but by using LOPA, plant safety teams can determine the proper gas and flame detection systems needed to reduce the risks down to an acceptable level
Safety is a top priority in the world of hydrocarbon refining, where the potential hazards of toxic and combustible gases, as well as the risk of open flames, require constant attention and precautionary measures.
To ensure efficient and cost-effective operations, these facilities rely on complex processes and equipment that often operate at extreme temperatures and pressures while maintaining a high-volume throughput.
Despite the challenges, maintaining a strong culture of safety remains paramount.
However, these risks can be further compounded in areas near flammable storage tank farms, pipelines, or offloading docks, where an incident can quickly escalate and cause widespread damage.
The consequences of such an accident can be catastrophic, leading to the loss of life, extensive damage to equipment and facilities, and even affecting the surrounding community.
Thus, it is crucial for these facilities to prioritise safety measures and prevention strategies to mitigate these risks and ensure the safety of both their employees and the environment.
![]() |
Figure 1: The elements of a gas and flame monitoring system |
Advanced gas and flame detection systems offer a dependable and intelligent solution to prevent gas and flame-related incidents. With high communication and intelligence capabilities, these systems aim to be reliable, low-maintenance, and cost-effective.
Under the best of circumstances, gas and flame detection is complex. Refineries and processing plants are typically large and often have high-density layouts of tightly placed equipment, piping, and tanks.
Processing areas that require gas and flame detection are often partially or fully exposed to the outdoors, subjecting gas monitors to heat, humidity, fog, rain, and wind.
For these reasons, no single gas or flame sensing technology is appropriate for all applications or situations or geographic location.
Depending on the individual plant site, the surrounding environment and the nature of the leak source, a gas or flame sensing technology that is appropriate in one place may not be appropriate in another.
Detecting gases and flames is a complex task due to the varying chemistry of gases and other factors that can influence their movement and behaviour.
Factors such as differences in gas density and the movement of gas clouds in the wind require a comprehensive approach to gas detection.
Flame detection can also be complicated by reflected light off shiny surfaces, leading to false alarms. The design of gas and flame systems must account for these and other factors to ensure accurate and reliable detection.
Let’s start by reviewing the elements of a gas and flame monitoring system (Figure 1). These systems continuously provide protection against life-safety hazards and abnormal situations in processing and other plants.
![]() |
Figure 2: Layered fire gas protection |
The hazards include fires, combustible gas leaks, and toxic gas releases. They also monitor related information, such as manually initiated alarms, wind direction, and system operational status (maintenance alerts).
They detect flames, fires, gases, smoke, heat, and other device-initiating signals. Their operational logic is typically defined within a cause/effect matrix.
Once a programmed gas or flame parameter is detected, the fire and gas system initiates alarm warning systems and hazard mitigation equipment including fire suppression.
It could be argued that the most critical elements in configuring a gas and flame monitoring system are the detectors themselves and the system controller.
The various gas sensing technologies provide different coverage profiles and capabilities. Some are designed for point localised monitoring, others protect a wider area and still others are suitable for perimeter monitoring of larger areas.
For example, catalytic bead, infrared (IR), and electrochemical sensors are designed for point monitoring while ultrasonic acoustic gas detectors provide area monitoring and open path monitors are used in perimeter monitoring. Some point H2S/CO sensors offer TruCal technology, which provides higher levels of safety.
There are multiple flame detector technologies as well, which can be categorised as point, area, and perimeter monitors. The most popular systems use optical methods to detect flames.
They detect the absorption of light at specific wavelengths. Two common optical flame detector types are; combination ultraviolet/infrared (UV/IR), and multi-spectrum infrared (MSIR).
These devices are sensitive to more than one band on the energy spectrum and, therefore, are less likely to produce a false alarm. Both technologies function well either indoors or outdoors and provide a reasonably fast response time.
The management of gas and flame detectors requires a specialised safety monitoring systems module. This system element requires a specially designed rugged industry standard programmable logic controller (PLC) that acts as a flame and gas logic solver.
Most plant safety teams will want a scalable system that is expandable linking multiple local gas and fire alarm panels over a wide network.
They will also want to be sure to choose a system that integrates easily with third party auxiliary devices such as horns, beacons, and fire suppression systems.
Designing an effective fire and gas monitoring system is best accomplished through a ‘layers of protection analysis’ (LOPA). The LOPA process begins with a five-step accident scenario process to:
• Identify possible accident scenarios.
Select a most likely accident scenario.
• Identify the initiating event(s) and frequency.
• Determine the independent protection layers (IPL) required and estimate the probability of failure on demand.
• Estimate the total risk with frequency and consequence of each event using baseline IPLs.
By comparing the most likely accident event scenario risk against the plant’s most tolerable risk threshold, the plant safety team can then begin to determine the proper gas and flame detection technologies and systems equipment needed to reduce risk down to an acceptable level (Figure 2).
The importance of safety cannot be overstated in the world of hydrocarbon refining. The use of advanced gas and flame detection systems can offer a dependable and intelligent solution to prevent gas and flame-related incidents.
However, designing an effective monitoring system is a complex process that requires careful consideration of various factors, including the nature of the hazard, plant layout, and geographic location.
By using LOPA, plant safety teams can determine the proper gas and flame detection technologies and systems equipment needed to reduce the risks down to an acceptable level and ensure the safety of both their employees and the environment.
In the September edition of OGN, we will take a look at MSA’s revolutionary General Monitors® S5000 detector and its H2S sensors with TruCal® technology.