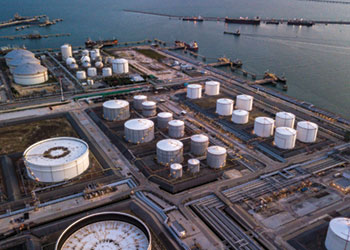
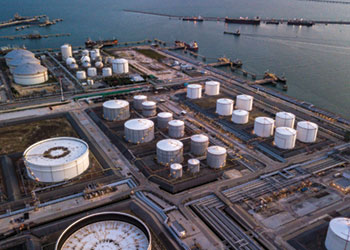
Tecam's environmental technology was able to reduce pollutants by 99.9 per cent at Koole terminals in the port of Rotterdam, the Netherlands, using customised Regenerative Thermal Oxidiser (RTO) as the most optimal solution taking into account the volume, nature and characteristics of the emitted vapours.
A regenerative thermal oxidiser (RTO) is a type of combustion engine that breaks down hazardous air pollutants (HAPs), volatile organic compounds (VOCs), and odours into CO2 and H2O before releasing them into the atmosphere.
Using high-temperature combustion, RTO technology converts air pollutants from industrial exhaust streams into CO2 and H2O before releasing them into the atmosphere.
The RTO's ceramic media heat exchanger, which retains heat from the previous combustion cycle to warm the airstream polluted with pollutants for the subsequent cycle, is where the term 'regenerative' originates from.
Koole Tankstorage Minerals (KTM), an international storage company providing logistics solutions, needed to eliminate the vapours and odour generated while barge and ship offloading for tank farm filling purposes with fuel oil, vacuum gasoil and class-3 blend components. These vapours contain highly polluting particles, mainly VOC, CO, SOx, NOx, MVP2 and PM10.
The project included 103 storage tanks spread over 1.1 million sq m area.
Tecam needed to take in mind the characteristics and difficulties of the emissions to be treated, including the fact that the vapour flow and VOC content are not consistent.
Also, depending on the product transfer taking place and the kind of product being stored, both flow rate and VOC load are subject to rapid fluctuations.
Additionally, KTM draws off a continuous base flow from its storage tanks. This base flow is mainly ambient air at its origin. On top of this base flow, vapours are generated by manipulations (pumping into storage tanks, barges and sea going vessels).
Benefits of the RTO solution include its adaptability to varying air fluxes, including low, medium, and high, it is possible to treat and eliminate a variety of pollutants. With low operating and maintenance costs and no waste production, high thermal efficiency is possible.
The result was the elimination of pollutants and emissions far below of the limits required:
• VOC: 20 mg/Nm3.
• CO: 50 mg/Nm3.
• SOx: 50 mg/Nm3 (thermal SOx).
• NOx: 50 mg/Nm3 (thermal NOx).
• MVP 2: (*) 1 mg/Nm3.
• PM10: 5 mg/Nm3.
Additionally, the solution guaranteed thermal efficiency of a minimum of 97 per cent. The vapours are collected in a vapour collection system and pre-treated in a pre-treatment train, obtaining very high efficiency.
A functional performance of 99 per cent was also guaranteed during stable and permanent uptime operation, excluding annual planned maintenance.
The analysis and design work of Tecam engineers have allowed Koole to count on an efficient installation, perfectly adapted to their needs, while the assembly and commissioning process was carried out within nine weeks without interrupting the terminal operability at any time.
In addition, the equipment guarantees the customer a lifecycle without any installation problems for more than 20 years.
Commenting on the project, Arjen Schneiders, Manager Strategic Projects at Koole Terminals, says: 'We are very satisfied with the correct functioning of the Vent Gas Treatment System for Tank Storage Terminals that Tecam installed in our Rotterdam premises in December 2018. Thanks to Tecam RTO we have successfully reduced VOC emissions since the equipment was installed. We also appreciate the reliable technical assistance provided by Tecam so far and are happy to count them as our environmental technology supplier. We have ordered a second RTO from them for our plant expansion.'