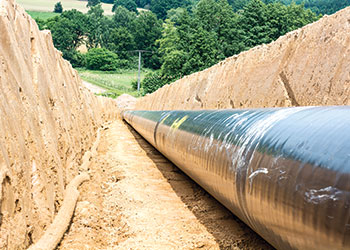
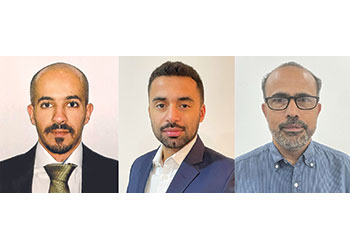
Abdulaziz Alsuayyid, Rashid Alrashid and Mahmoud Elzayat, Project Engineers at Saudi Aramco tell OGN they have outlined best practices to enhance the process of hydrotesting and reinstatement for aboveground metallic piping systems, resulting in optimising project constraints while maintain quality
Process and non-process piping systems in oil and gas mega projects usually make up around 30 per cent of the overall project scope of work.
These systems, which include but are not limited to pipes, fittings and valves, go through a number of tests and preparation activities during construction and pre-commissioning stages, which require detailed planning, cross-checked preparation, and precise execution to have a fully integrated piping system that is ready for startup.
The tests include hydrotesting and reinstatement, considered crucial activities in the construction/pre-commissioning phases that can be a bottleneck for any mega oil and gas projects.
Hydrotesting is a process of pressure testing by filling constructed pipes with water to examine the integrity of welded joints, whereas reinstatement is a sequential activity for process piping system as a preparation prior to commissioning.
Planning for hydrotesting and reinstatement should start in the early stages of the project design to ensure its smooth execution. The meticulous planning process includes system identification, piping packages identification, model package, material availability, testing procedures, interface coordination, and a hydrotesting and reinstatement centre.
CONSTRUCTION
During the construction phase, a well-structured plan is required to complete the hydrotesting and reinstatement activities in an efficient way.
![]() |
Figure 1 … planned activities throughout the piping package stages |
A dynamic approach for manpower utilisation needs to be applied such as shifting from one area to another, to accommodate changes required during construction.
Some key elements that need to be considered to have a positive impact on each stage of the package lifecycle and to minimise the lagging period include:
• Punch-listing awareness: This activity is considered as the gate that will allow the piping packages to move from one phase to another. Usually, this is conducted jointly by project stakeholders. Hence, a proper acceptance criteria needs be developed and agreed among those stakeholders.
Punches can be categorised into types A and B, where A is an activity that it is mandatory to be completed prior to carrying on with hydrotesting, such as; pipes/valves welding, primary supports. And B can be completed post hydrotesting and can be considered part of the reinstatement processes completions.
A way to align the understanding is to develop a punch-listing procedure, which outlines the agreed-on definitions and the punch-listing requirement during the walkthrough.
• Constructing for reinstatement: From a construction point of view, piping construction activities should be completed to be ready for punch-listing verification resulting in minimum punch items.
In another way, all activities required prior to hydrotesting and reinstatement need to be completed to expedite the package preparation, and minimise the period of punch-listing and verification.
• Manpower: Proper manpower planning should be considered to execute the work-related pipe fit-up, welding, erecting, and hydrotesting activities with respect to the size of the scope of work.
In addition, quality has to be monitored and controlled, because poor quality could impose high risk leading to hydrotesting failures, rework, and a subsequently negative impact.
![]() |
Figure 2 … categorisation of piping packages |
Keeping in view these essentials, the construction company needs to specify quality personnel according to the magnitude of work in regard to hydrotesting or reinstatement; for instance, estimating the magnitude of work with correlation to the number of isometrics per package.
This is usually done through identifying the number of isometrics that can be inspected per day, allowing to predict the number of quality control supervisors and inspectors required.
Usually, it is a challenge for construction companies to allocate the exact required number of inspectors due to the approval requirement and process for the quality personnel.
Therefore, construction agencies should conduct walkthroughs for punch-listing and punch verification over a large scattered construction area due to the size of the packages.
These are to be handed to the construction team for rectification as part of the remaining construction work.
Thus it is recommended to utilise part of the construction team, such as line checkers, to confirm the completion of the construction work prior to offering the package to quality inspectors.
This practice avoids rework, enhances productivity, and optimises resources when completing the construction work.
• Isometrics versus volume: Based on the number of piping packages identified, work can be expedited and prioritised by correlating the number of isometrics and water volume required to conduct the hydrotesting for each package.
For example, the packages with a high number of isometrics are likely to take more time and manpower to close and verify the punches, not to mention the fact that large bore sizes consume higher quantity of water during filling and disposal, which extends the lagging period.
Piping packages are categorised based on volume versus the number of isometrics as illustrated in Figure 2 to indicate the package complexity, where the construction company may prioritise and distribute the workload based on the complexity category. Relying only on the numbers of the packages can mislead the work activity estimation.
![]() |
Table 1 … daily tracking using a whiteboard |
As a rule of thumb, around the 20 per cent of packages (high complexity) require the same efforts and man-hours of the remaining 80 per cent.
• Monitor and control: Monitoring and controlling hydrotesting and reinstatement is vital to deliver a complex piping scope of work within the required parameters.
Monitoring and controlling should not be limited to the construction activities, but it also needs to be extended to material, manpower, daily productivity, and addressing conflicts, which all might need adjustment, and the primary venue for monitoring and controlling this task is in the hydrotest centre.
• Digital platform: The communication method among project stakeholders is the key success factor that can reduce the lagging period and increase the productivity and expedite executing the activity.
This digital platform can be presented as a tool to exchange information or retrieve the required project data anytime and anywhere.
A digital platform has to be accessed from different locations to serve all stakeholders where the following information is available for any given piping package: piping package tag/number; tracking of the piping package through the piping package lifecycle; complete bill of material for piping packages; material delivery tracker for piping packages; and record for quality documents (material receiving, witnessing activities and violation).
• Daily tracking: A daily tracking tool needs to be fixed at the hydrotesting centre and should be clear to all entities working to identify where the bottlenecks are within the process so that rectification can be implemented in a timely manner to achieve the daily target of completion.
Table 1 is an example of how a whiteboard can be utilised for this purpose. The whiteboard is updated twice a day, where the first update will give the chance to measure and adjust the focus, and the second update is to reflect the overall daily progress.
CONCLUSION
A successful piping hydrotesting and reinstatement would include:
• Identifying packages during the detail design (60 per cent and 90 per cent deliverables).
• Correlating first priority piping packages with material delivery and pipes prefabrication.
• Completing pipe welding and erection to be done with respect to a full package and full isometrics to start hydrotest activities at the early stage of construction.
• Capitalising on enough personnel of the line checker team to ensure construction completeness of the packages prior to offering the packages to inspection. This minimises issues and findings and thus reducing rework and improving productivity.
• Having a hydrotest centre at site for running the hydrotesting and reinstatement activities. The centre will host all involved entities from both construction agency and client in one place to smoothen the communication processes, particularly for the review and approval processes.
This will not only increase the ownership and countability across the hydrotest centre, but will also reflect efforts of all parties for completing the work in terms of scope, quality, and schedule.