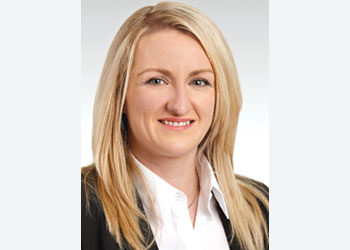
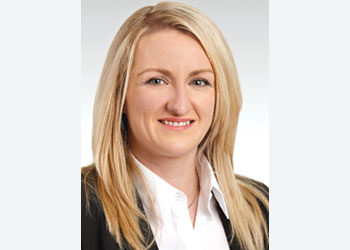
Rupture discs can be used as a cost-effective and efficient way to create a leak-tight process and reduce emissions, whether on their own or in combination with a safety valve, Claire Lloyd, Team Leader, Process Safety Business Expansion, REMBE Safety+Control, tells OGN
For many years, emissions were an unavoidable consequence of industrial development. An increase in awareness of environmental issues combined with subsequent legislation means that major oil and gas companies are under pressure to cut their greenhouse gas emissions, and several have responded by setting reduction targets over the coming decades.
There are several ways in which operators can work towards emissions reductions and our focus is on the impact the use of various safety devices can have on this target.
The first point of consideration in this regard should be the safety valves in use.
Valves are an obvious place to start as no valve is 100 per cent leak-tight, and this decreases every time there is an activation and the valve re-seats.
In the building of new plants, it is a fairly simple solution to specify within the design of the plant a valve with a lower leak rate. However, existing plants are looking at substantial investments to replace older designs with newer technologies. Not a viable economical solution in most cases.
While there have been significant increases in the capabilities of safety valves, they are still not the ideal product when considering future net-zero targets. Safety valves struggle to meet the exacting requirements of the legislators, and an alternative solution is needed.
RUPTURE DISCS OFFER LEAK AND EMISSIONS REDUCTION
![]() |
A safety valve and rupture disc offer an ideal combination |
Although rupture discs have been around for decades, they are often considered only as secondary relief, and should to be used where there is a possibility of safety valve failure.
There is a lack of understanding amongst engineers in industry and a number of myths surrounding the use of rupture discs exists.
A rupture disc is a non-reclosing device and, therefore, must be completely replaced when there is an activation.
Frequent disc rupturing leads to downtown and this nuisance leads many operators to associate rupture discs with a problem with the process.
Many operators still don’t realise that when the disc performs correctly, it is not the problem but the solution.
But how can a rupture disc help get improved performance from a safety valve?
Rupture discs are 100 per cent leak-tight. By installing a rupture disc in front of a safety valve, you get double protection and a solution, which can meet emission requirements.
There is no more leakage through the safety valve in normal operation and where there is an over-pressure activation, the valve reseats to seal the process once the pressure is vented.
The belief that this arrangement adds more cost to a project has been proven to be false, and in fact it is the opposite.
A correctly engineered rupture disc will help lower operating costs and increase the uptime for any plant.
In processes where there is a high concentration of corrosive media, increased temperatures and an operating pressure close to the safety valve set pressure, safety valves are pushed to their limits. Poor performance is common-place.
High maintenance costs are needed to keep the valve as close to the original specifications as possible; there is increased production downtime due to routine valve servicing and/or repairs; and higher manpower costs to cover the work scopes.
![]() |
A rupture disc for isolating safety valves |
The solution from safety valve manufacturers includes a higher specification valve, more exotic materials with higher capex costs as well as increased cost of spares to maintain the valves.
Thus if you consider a typical petrochemical plant with several hundred safety valves, the capital expenditure is significant.
A rupture disc fitted upstream of the safety valve completely isolates the valve from the process. This protects the safety valve from the process, which in turn reduces maintenance requirements.
There is also the possibility of reducing capex costs by sourcing a rupture disc and holder in an exotic material and a standard safety valve.
The costs of a discs and holder are usually significantly lower than having to source a high specification safety valve, which is compatible with the process media.
The protection of safety valves with rupture discs has become increasingly common in recent years across several industries. However, many operators miss the opportunity to fully protect the safety valve by also isolating the valve from potential corrosion issues on the outlet of the valve.
In many cases, the valve outlet is not a separate discharge line to but it is connected to other parts of the plant via a manifold, which allows process gases/vapour to enter the outlet of the valve.
If there is a risk that the process media can damage the valve via the inlet, this is also the case downstream.
A rupture disc can also be used to isolate the safety valve outlet and prevent any contact with the process media.
The rupture disc will also block any back pressure from entering the safety valve and remove those concerns during valve selection.
With burst sensors installed, both upstream and downstream rupture discs can be monitored and connected back to the control room for system reporting across the plant. So operators instantly know which valves and discs are in a green or red state.
Another myth surrounding rupture discs is that they can leak.
If the disc is to be installed as the primary safety device, that’s to say, without a safety valve behind it, this can be a concern for operators looking to reduce emissions.
The majority of leakages via rupture discs are caused by corrosion or damage during installation by mishandling or incorrect torquing.
Rupture disc technology has improved significantly over the years to ensure that damages caused by corrosion or incorrect handling are all but eliminated.
Today’s modern rupture discs no longer use mechanical scoring techniques—which can lead to works hardening and corrosion over time—during manufacturing.
Advanced manufacturing technologies have resulted in robust rupture discs, which are no longer sensitive to torque and virtually immune to damage during installation.
Most unwanted failures from rupture discs can be avoided by working together with the disc manufacturer to select the ideal rupture disc for the process conditions.
Overall, rupture discs can be used as a cost-effective and efficient way to create a leak-tight process and reduce emissions, whether on their own or in combination with a safety valve.
REMBE Safety+Control is a specialist for explosion safety and explosion venting worldwide. The company offers customers cross-industry safety concepts for plants and equipment. Its customers include market leaders in various industries, including the food, timber, chemical and pharmaceutical industries.
All REMBE products are manufactured in Germany and meet the requirements of national and international regulations.
The company’s engineering expertise is based on 50 years of application and project experience.
As an independent, owner-managed family business, REMBE combines expertise with the highest quality standards and is involved in various specialist committees worldwide.
Short coordination paths allow for quick reactions and customer-specific solutions for all applications, from standard products to high-tech special designs.
REMBE Safety+Control has 340 employees worldwide and is headquartered in Brilon (Hochsauerland, Germany) with numerous subsidiaries worldwide, including in Italy, Finland, Brazil, the US, China, Dubai, Singapore, South Africa, and Japan.
In addition to REMBE Safety+Control, there are four other companies under the REMBE umbrella brand: REMBE Research+Technology Center; REMBE Advanced Services+Solutions; REMBE Kersting; and REMBE FibreForce.