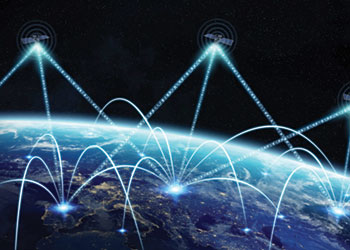
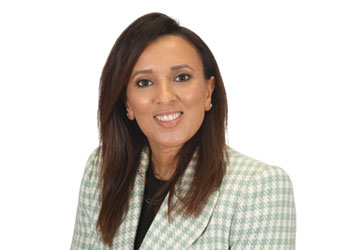
The Stami Digital portfolio of digital services has a proven track record of effectively improving plant load and reducing energy consumption, Malika Nait Oukhedou from Stamicarbon tells OGN
AS chemical plants grow not only in size but in complexity, the concept of the ‘digital plant’ is emerging as a game-changer, reshaping how technology empowers a connected workforce, driving efficiency, and fostering innovation.
In this interview with Malika Nait Oukhedou, Business Development Manager of Stamicarbon, the nitrogen technology licensor of the MAIRE engineering group, the OGN energy magazine discussed the pivotal role of digital transformation in the fertiliser industry.
How does the digital evolution transform the approach of fertiliser producers? Why are digital solutions important for minimising environmental impact and improving safety?
Historically, the chemical industry has continually strived to enhance productivity through intelligent and innovative approaches.
The goal has always been to increase outcomes with optimal effort and cost, a principle that remains unchanged in the digital age.
However, when it comes to the digital evolution rapidly transforming our world, fertiliser producers have been more conservative compared to other heavy industries.
One of the reasons behind that is the complexity of the underlying chemical reactions and mechanisms, which make creating a plant model a complex task requiring a fundamental understanding of the process thermodynamics and reactions phenomenon, including the kinetics and equilibria.
Despite this conservative approach and challenges, it’s quite evident that digital solutions are capable of not only creating additional revenue streams but also making strides toward minimising environmental impact and improving safety. Both considerations are crucial in today’s quest for a sustainable future.
This evolution mirrors the core principles of Industry 4.0, where the synergy of people, processes, and technology plays a pivotal role.
The transparency of information, coupled with the necessity for real-time insights, is reshaping the way decisions are made, favouring a data-driven approach.
What types of plant models are fertiliser producers turning to for comprehensive process insights?
To gain comprehensive process insights, fertiliser producers are increasingly turning to virtual plant models, both in offline and online applications.
These models can be knowledge-driven (first principle models), requiring a thorough understanding of underlying mechanisms.
Alternatively, these models can be data-driven and rely on experimental data for situations with a limited understanding of the physical process.
A third type, the gray-box model, merges simplified first principles with data-driven elements for an efficient balance.
The Stami Digital Process Monitor’s plant model is purely knowledge-driven, boasting high predictive accuracy.
It encompasses a complex mathematical framework including mass and heat transfer equations, reaction kinetics, and more, encapsulating the plant’s entirety with over 5,000 equations.
A specially developed equation-oriented flow sheeting program tackles these large-scale complex calculations.
How is the architecture of the Stami Digital Process Monitor tailored to customer needs?
The Monitor offers numerous features, such as real-time monitoring of key variables, reliable emissions tracking, sensor duplication, and dynamic graphical interfaces, collectively leading to significant savings and enhanced efficiency, reliability, and safety.
The architecture of the Stami Digital Process Monitor is tailored to customer needs, offering functionalities like real-time optimisation, predictive control, data reconciliation, and comprehensive monitoring systems.
As shown in Figure 1, real-time plant data is securely transmitted to the Process Monitor Engine in the cloud.
The Process Monitor feeds real-time data into the rigorous plant model, calculating key performance indicators (KPI) such as plant load, energy use, and emissions, along with soft sensor key variables that are displayed on a dashboard, making them accessible to plant operators and stakeholders.
![]() |
Figure 1 ... The Stami Digital Process Monitor architecture |
As illustrated in the diagram, where arrows indicate the direction of information flow, there is no closed-loop system-to-system communication.
Under no circumstances does the Process Monitor directly intervene in the DCS. The plant’s DCS system is exclusively controlled by plant operators and serves solely as a data source for the plant model.
This concept adheres to the highest information security standards, in compliance with Stamicarbon’s ISO 27001 certification, the global standard for Information Security Management.
What steps are involved in creating the plant model? How does the data reconciliation phase ensure the model’s accuracy?
Creating the plant model involves a consulting phase and a data reconciliation phase.
Initial steps include interviewing plant experts to harness operational insights and historical data.
This phase yields valuable insights, including sensor evaluations, plant constraints, and operation assessments.
In the data reconciliation phase, historical DCS data is collected and used to refine the model, ensuring its accuracy in representing the process.
This stage involves correcting deviations and updating model parameters, akin to a feedback process in control engineering.
An example of model validation is depicted in Figure 2, showcasing the correlation between model-predicted and actual DCS readings of reactor temperatures, a crucial variable in urea synthesis.
![]() |
Figure 2 ... Reactor temperature validation |
Post-validation, the Stami Digital Process Monitor offers real-time insights on KPIs and soft sensor key variables, aiding in maximising efficiency and boosting production.
What are soft sensor key variables, and how are they developed and adjusted to specific customer needs?
Key variables (KVs) define the technical and economic performance of the urea process.
Traditionally determined by offline laboratory analysis, process modeling aims to provide operators with real-time, accurate estimates of these KVs.
The Stami Digital Process Monitor generates these soft sensor key variables in real-time (Figure 3), facilitating advanced process monitoring and optimised control.
The soft sensors can be developed and adjusted to specific customer’s needs and constraints.
‘Soft’ as in, for example, Soft N/C meter in this case, refers to the software (the process model) that generates the N/C value.
![]() |
Figure 3 ... Soft Sensor Key Variables |
How does troubleshooting with the Digital Process Monitor contribute to plant performance optimisation? What is the value of knowledge gained from troubleshooting sessions for operational specialists?
After the introduction of Stami Digital Process Monitor on-site and the data being available for the customer, Stamicarbon will, on a regular basis, have virtual meetings with the customer.
In these meetings, as a part of the ADVANCE Consult™ service portfolio, the process data of the past period will be evaluated and discussed with the customer’s operational specialists (operators, supervisors, process and process control engineers, etc).
These sessions help operational specialists understand the meaning of the KV’s and how to use them to your benefit in optimising plant performance.
In the discussions, suggestions for improvement of the operations in terms of capacity increase, emission reduction and energy efficiency will be given.
This data will provide operational insights, such as identifying unwanted operations that may affect the lifetime of equipment.
Stamicarbon’s experience in projects across the globe has proven that these sessions have been highly valued by customers.
They have been effective in detecting measurement errors, equipment bottlenecks, and inefficiencies.
Additionally, operating strategies developed based on operational insights from the model data have proven to be very efficient in practice.
![]() |
Figure 4 ... Troubleshooting ... feed stream to the wastewater section |
![]() |
Figure 5 … Troubleshooting … compressor load offset |
With training in using the Stami Digital Process Monitor, operational specialists are equipped to identify unwanted operations that may affect the lifetime of equipment and troubleshoot.
This can, for instance, be done by comparing plant DCS (distributed control system) values with model calculations (as shown in Figures 4 and 5). This comparison helps in promptly identifying and rectifying operational issues, thereby preventing production losses.
What tangible benefits can the digital solutions provide for users?
Leveraging its extensive expertise in nitrogen technology, Stamicarbon, together with sister companies from MAIRE Group - KT and Technimont is working on developing a digital toolbox for the process industry to optimise plant operations.
The Stami Digital portfolio, comprising a suite of digital services, has a proven track record of effectively improving plant load and reducing energy consumption.
The Stami Digital Process Monitor, along with the company’s other digital solutions, has demonstrated efficiency and tangible benefits for customers in various chemical processes.
In the face of tightening regulations and evolving market demands, digital solutions have proven themselves to be crucial for optimising plant efficiency, minimising environmental impacts, and facilitating the industry’s transition to a sustainable future.