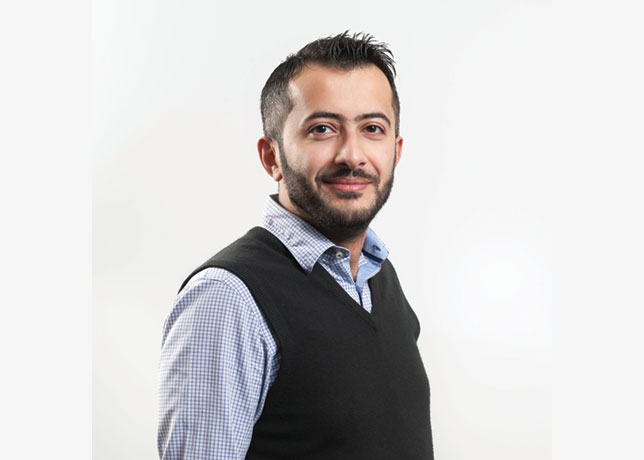
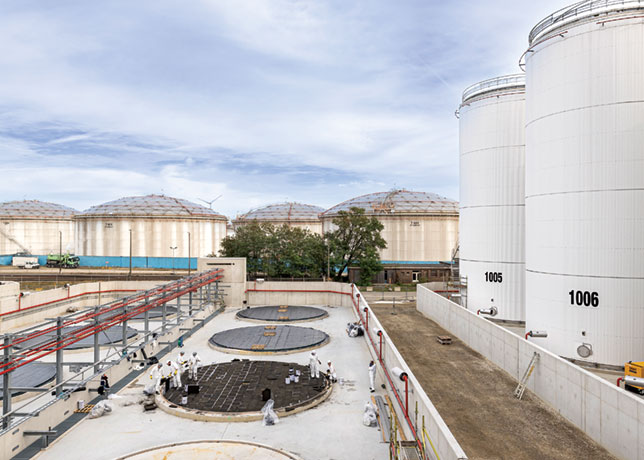
Owens Corning’s FOAMGLAS® insulation system lowers energy losses through the tank bottom by 90 per cent and reduces the overall carbon emissions of a heated tank
Storage tanks are used to hold a variety of organic liquids or gases including raw materials, intermediates, final products or, usable byproducts.
Although mainly used in the oil and gas industry, other industries often rely on upright storage tanks to temporarily store liquids, for example, the food and fertiliser industries.
Tanks can vary in design, and the properties of the products being stored determine the storage temperature, and if additional heating is necessary to maintain a certain temperature inside.
In the case of heated storage tanks, this often has to do with preserving the quality of the stored product and preventing solidification of the hot liquid.
WHY DOES ENERGY EFFICIENCY MATTER?
The growing worldwide demand for chemical products and proper storage and handling makes energy efficiency of storage tanks a key requirement.
This, combined with the all-time high energy prices, forces terminals and processing facilities to rationalise their energy consumption and improve the efficient use of energy sources.
Each year, large amounts of energy are wasted due to storage tanks not having proper insulation systems in place.
This used to be negligible but the current economic environment is demanding facilities to rethink the way energy is wasted.
ENERGY LOSS IN HEATED STORAGE TANKS
When tanks operate above ambient conditions, the tank walls and roofs are often viewed as the main sources of energy loss.
However, the heat loss at tank walls and roof will fluctuate when the liquid level increases or decreases but the heat loss through the bottom will always remain constant.
Depending on the storage temperature and tank size, heat loss through the tank bottom can run up to over 250 W/sq m (80 BTU/h•sq ft) leading to large yearly energy losses that would accumulate to hundreds of thousands of dollars over the lifetime of the tank.
TACKLING CARBON EMISSIONS
Globally, heat accounts for nearly half of energy-related carbon emissions. Therefore, losing large amounts of heat leads to high amounts of unnecessary carbon emissions for a facility.
In times when processing facilities and terminals are focussing on reducing their overall carbon footprint, it is inevitable that every opportunity to reduce heat losses and corresponding emissions should be grasped fully.
One of the easiest and most cost-effective ways to immediately tackle this issue is to install a cellular glass insulation system underneath the heated storage tank.
Insulating the tank base can immediately reduce the heat loss through the bottom by up to 90 per cent.
The insulation value of cellular glass insulation also does not change during its lifespan, thus ensuring constant and lasting energy savings.
This allows for easy calculation of the yearly energy savings, payback periods, annual financial yields and, saved emissions over the lifetime of the tank.
CALCULATED PAYBACK PERIODS AND ANNUAL YIELDS
![]() |
The FOAMGLAS tank base insulation system's return on investment can be merely months |
Tank builders and terminal owners can call on the expertise of Owens Corning’s technical services team to assist with the calculation of payback periods and annual yields of the investment in a FOAMGLAS® HLB insulation tank base insulation system.
These calculations consider all relevant factors, such as temperatures and local energy prices.
For each project, the heat lost through the base without insulation is calculated and compared with the total investment cost.
This provides the total payback period of the investment in a FOAMGLAS® tank base insulation system, which can be as short as merely months depending on the storage temperature of the contained liquid.
In addition, the total future yield of the investment is calculated for the active life of the tank with an insulated tank base.
This shows the amount of energy saved per area of insulated tank base and the total yield per year after the payback period.
WHAT ABOUT EXISTING TANKS?
This, of course, is a no-brainer when new tanks are going to be built but what about existing tanks?
Dedicated tank base insulation systems can easily be installed during scheduled tank maintenance programmes when the tank is emptied to inspect the metal tank bottom and possible metallurgic repairs are being done.
This can be done by lifting the tank and positioning it on jacks. This gives the opportunity to install a tank base insulation system onto the concrete deck before the tank is lowered again.
Another possibility is to install the insulation directly onto the metal base inside the tank and weld a new metal bottom onto the newly installed insulation system.
CASE STUDY: INSULATING FOR RELIABILITY, ENERGY EFFICIENCY AND COST-EFFECTIVENESS
The Dutch tank storage company, Standic, a member of the family-owned Hametha group, has been an established storage provider for over 60 years.
They operate three terminals in the Netherlands and Belgium and offer storage to both large industrial parties as well as niche players and specialists.
Standic opened up a brand-new, highly automated state-of-the-art terminal in the centre of the Antwerp ‘chemical hub’ to enable it to serve its chemical customers even better.
The terminal was designed to operate in the most efficient and cost-effective way and optimising energy efficiency was one of the key requirements during the design phase.
A great example of this is using residual heat to heat up the tanks and the choice to add FOAMGLAS® cellular glass insulation between the concrete foundation and the bottom of the tanks to minimise heat lost through the bottom and reduce excessive use of energy for tank heating.
The construction of the new storage terminal is taking place in a phased approach.
Phase 1 consisted of adding 95,000 cu m of capacity distributed over 79 tanks with different diameters and a height of 24 m.
The second phase of this expansion project added another 85,000 cu m of storage capacity to the terminal with 46 additional tanks.
By the end of 2025, Phase 3 will be completed and the entire terminal will be operational, and able to offer 249,000 cu m of storage capacity.
Standic was no stranger to specifying FOAMGLAS® cellular glass insulation for heated storage tanks, as cellular glass had already been installed underneath tanks at their Dordrecht terminal about a decade ago.
One of the benefits of specifying a tank base insulation system for the chemical storage tanks is that it allows tanks to be used for the storage of a wide array of products, heated or cooled.
This provides additional flexibility in operating the terminal’s assets.
Additionally, by lowering the energy losses through the tank bottom, the overall carbon emissions of a heated tank can also be reduced contributing towards operating the terminal in the most sustainable way.
The system that was specified for this particular project consisted of a single layer of FOAMGLAS® high load-bearing insulation blocks in a thickness of 50 mm.
The blocks were glued directly to the concrete foundation with one of Owens Corning’s proprietary adhesives.
Once all the phases have been completed, Owens Corning will have supplied high load-bearing tank bottom insulation systems for more than 100 heated tanks.
This will help the terminal to operate in the most flexible and, energy- and cost-efficient way to serve their chemical customers.