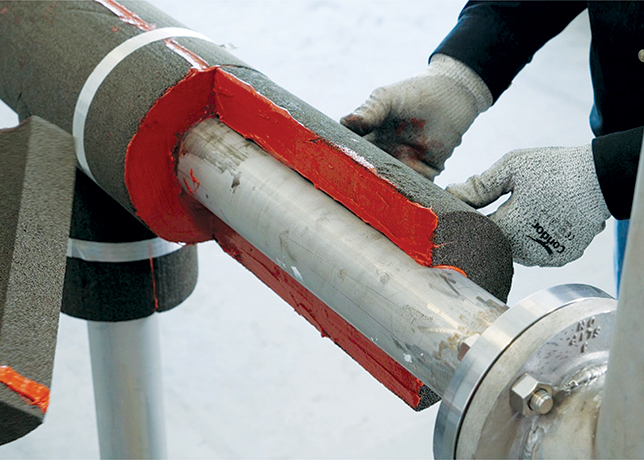
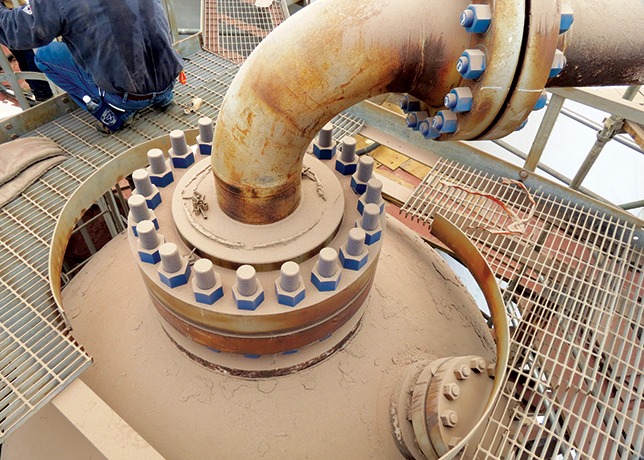
Corrosion in the oil and gas industry demands robust management strategies to mitigate significant financial and environmental impacts, ensuring the longevity and integrity of critical infrastructure
The oil and gas industry plays a pivotal role in global energy supply, yet it grapples with a persistent adversary–corrosion.
A study by the National Association of Corrosion Engineers (Nace) reveals that corrosion costs the industry a staggering $1.372 billion annually. This significant financial burden is broken down into $589 million for surface pipeline and facility costs, $463 million for yearly downhole tubing expenses, and an additional $320 million for capital expenditures related to corrosion.
The financial and environmental implications of corrosion in the oil and gas sector are expected to escalate. As the industry ventures into more challenging environments, including deeper reservoirs with higher temperatures, pressures, and greater concentrations of acid gases, the susceptibility to corrosion increases.
This necessitates a robust corrosion management strategy to mitigate these growing challenges and reduce operational costs over the long term.
Repairing corrosion is not only expensive but also poses significant risks to workers and the environment. Additionally, it leads to the wastage of valuable time and materials, making corrosion prevention critically important.
THE UBIQUITY OF CORROSION
Corrosion is a relentless force that can compromise the integrity and longevity of structures, equipment, and systems across various industries.
Whether affecting pipelines in the energy sector, bridges in transportation, offshore platforms in marine environments, or port infrastructure, the impact of corrosion is widespread.
As industries evolve and infrastructures expand, ensuring the integrity of critical assets becomes increasingly complex.
In asset management, integrity and inspection are pillars of reliability and safety. These practices delve deep into the core of asset health, identifying subtle signs of degradation that could compromise safety.
Rigorous inspection protocols and cutting-edge technologies enable businesses to fortify their assets against corrosive forces threatening their structural integrity.
Effective corrosion management within the oil and gas industry contributes to achieving various benefits, including statutory or corporate compliance with safety, health, and environmental policies, reduction in leaks, increased plant availability, and reduction in unplanned maintenance and deferment costs.
CORROSION'S APPEARANCE & IMPACT
In pipes, corrosion can begin with damage to the inner structure or the outer surface coating. As the coating fades, the pipe looks dull, affecting external audits.
Gas and oil fields use large amounts of steel and iron pipe, pumps, valves, sucker rods, and tubing. Leaks result in gas and soil loss and allow salt and water infiltration, exacerbating corrosion damage. Corrosion occurs inside and outside casing in gas and oil wells, where sulfides and saline water are prevalent.
In refineries, corrosion is often caused by inorganics such as carbon dioxide, water, sodium chloride, and sulfuric acid, rather than the organics themselves.
Corrosive agents present in crude oil or feedstock and those associated with control or processes contribute to the problem. Water, usually present in crude oils, is difficult to remove completely. Carbon dioxide has recently been recognised as a significant corrosive agent, especially in gas operations.
Moisture in compressed air leads to corrosion as pipe coatings wear out, causing gradual pitting corrosion and leaks. In high-pressure flowing wells producing pipeline oil, corrosion is common. Coated tubing, alloys, and inhibitors can combat this issue.
Sour oil wells, which handle high-sulfur oil, present a more corrosive environment. Continuous injection of inhibitors significantly reduces corrosion. Offshore structures, supported by beam piles driven into the ocean, are highly susceptible to rapid corrosion, which is mitigated through cathodic protection, inhibitors, and paints.
Corroded pipes with irregular inner surfaces and high leak rates can cause unacceptable pressure drops, indirectly reducing business profits.
Slurries and other abrasive media lead to interior wall corrosion, resulting in scaling, which increases pressure drop and constricts fluid flow.
Rust generated by corrosion, after reacting with oxygen, flows in steel pipes with compressed air, attacking piping accessories and instruments like dryers, pressure gauges, and filters.
Poor filtration and internally rusted pipes can bring rust particles into the end product, leading to quality loss.
Compressed air becomes contaminated as it passes through rusty pipes, introducing dust particles and hydrogen ions. This contaminated air is unsuitable for many processes and machines.
Furthermore, petroleum products are transported by pipelines, tank trucks, tankers, and railway tank cars. Gasoline-carrying tankers face severe internal corrosion problems because gasoline keeps metal clean.
The primary cause of internal corrosion in storage tanks is water, which settles and remains on the bottom. Internal corrosion in product pipelines can be controlled using coatings and inhibitors such as nitrites and amines.
CONCLUSION
Corrosion in the oil and gas industry is a pervasive and costly challenge that demands comprehensive management strategies. By investing in advanced materials, inspection technologies, and preventive measures, the industry can mitigate the financial and environmental impacts of corrosion. As the sector continues to explore new frontiers and adopt sustainable practices, effective corrosion management will be pivotal in ensuring the longevity and integrity of critical infrastructure.
By Abdulaziz Khattak