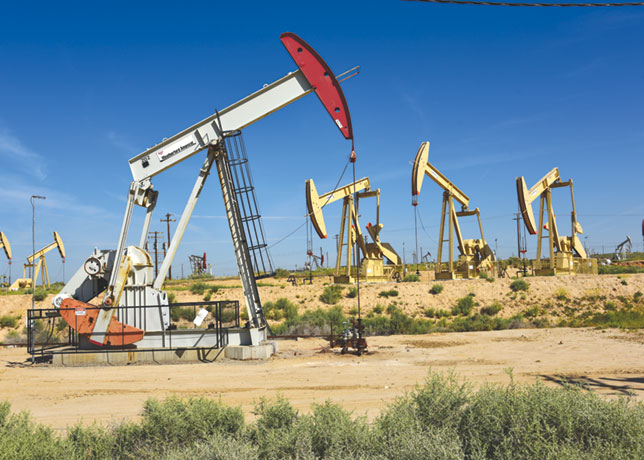
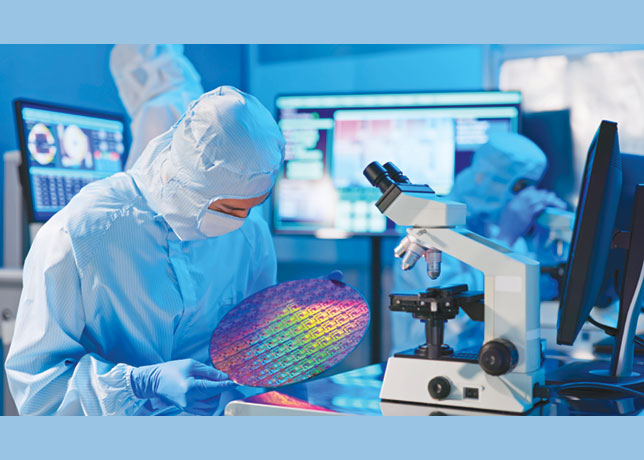
Nanotechnology enhances oil and gas operations by improving drilling fluids, equipment durability, and recovery processes, addressing long-standing challenges and boosting overall efficiency and innovation in the sector, say researchers
Nanotechnology is making waves in the oil and gas industry, driving a new era of innovation that promises to redefine drilling operations and overall efficiency.
This burgeoning field is poised to address several long-standing challenges within the sector, from well drilling to oil recovery, by leveraging the unique properties of materials at the nanoscale.
One of the most promising applications of nanotechnology is in the enhancement of drilling fluids.
Traditionally, drilling fluids are essential for successful operations, providing lubrication, stabilizing the wellbore, and regulating pH levels.
Conventional additives such as xanthan gum and carboxymethyl cellulose have been vital, but recent advancements involving nanoparticles are pushing these fluids to new heights, say researchers from the International College of Engineering and Management in Oman and University of Glasgow.
Nanoparticles are proving to enhance lubricity, thermal stability, and filtration capacities beyond what traditional additives could achieve, Alhaitham Alkalbani and Girma Chala say in their paper, ‘A Comprehensive Review of Nanotechnology Applications in Oil and Gas Well Drilling Operations’, published in the Energies journal.
This translates to reduced friction, improved wellbore stability, and increased drilling efficiency, making them a game changer in the field, they said.
ADVANCEMENTS IN DRILLING FLUID ADDITIVES
Different types of additives play crucial roles in maintaining the performance of drilling fluids under various conditions.
Filtration control additives like starch and polyanionic cellulose, along with rheology modifiers such as guar gum powder, have historically been important.
However, nanoparticles offer enhanced stability and performance, surpassing the capabilities of their traditional counterparts.
This advancement underscores the transformative impact of nanotechnology on drilling fluids, promising more reliable and efficient operations.
IMPROVEMENTS IN DRILLING EQUIPMENT
The benefits of nanotechnology extend well beyond drilling fluids. The integration of nanocomposite materials into drilling equipment has led to improvements in mechanical strength, wear resistance, and thermal stability.
These enhancements result in more durable and efficient equipment.
Additionally, advanced reservoir characterization tools employing nanoparticle tracers and nanoscale imaging techniques are aiding in the precise location of drilling sites and boosting production effectiveness.
In the realm of oil recovery, nanotechnology is proving to be a game changer. Nanofluids and nano emulsions have the ability to modify fluid mobility, reduce interfacial tension, and alter rock wettability, which can significantly enhance oil extraction processes.
Despite these advancements, challenges such as ensuring the stability and dispersion of nanoparticles, as well as addressing their potential environmental impacts, remain.
Ongoing research aims to tackle these issues, optimising the use of nanotechnology in drilling operations and enhancing overall recovery rates.
Nanotechnology, with its foundation in manipulating materials at the atomic and molecular levels, has revolutionised material science.
The ability to explore and exploit the unique properties of materials at the nanoscale, ranging from 1 to 100 nanometers, has enabled the development of new materials with remarkable characteristics.
Techniques like ball milling, which grind substances into nanoscale particles, are critical in this field, ensuring uniform dispersion and the formation of new materials.
This transformative impact of nanotechnology is evident across various industries, including electronics, aerospace, and medical fields.
In the oil and gas industry, nanoparticles are enhancing drilling fluids by improving their rheological properties, which helps in carrying drilling cuttings, cooling drill bits, and reducing friction.
Nanoparticles such as nano-silica are also effective in blocking pore mouths in shale formations, which improves fluid invasion control and wellbore stability.
CHALLENGES & FUTURE DIRECTIONS
However, the use of nanoparticles comes with its own set of challenges. The environmental impact of drilling fluids and the economic feasibility of high concentrations of nanoparticles need to be addressed.
Nonetheless, ongoing research continues to explore more efficient and cost-effective ways to utilise these materials, with promising results in filtration control and thermal conductivity enhancements.
The use of cellulose nanofibers (CNFs) and nanocellulose derivatives in drilling fluids represents another significant advancement.
Research has demonstrated that functionalising nanocellulose can improve temperature tolerance and fluid stability in water-based muds, outperforming traditional polymers like guar gum and xanthan.
The interaction between CNFs and other additives like polyanionic cellulose enhances yield points and fluid stability, though CNFs and cellulose nanocrystals (CNCs) still lag behind other nanoparticles such as iron oxide and graphene oxide in filtration control.
Nanoparticles are also being explored for their electrical and thermal conductivity properties, crucial for efficient heat removal from drill bits and wellbore visualisation.
Nanomaterials with high surface area-to-volume ratios, such as nano-sized tin oxide and copper/zinc oxide, have shown significant improvements in thermal conductivity.
Zinc oxide nanoparticles have been effective in enhancing electrical conductivity, while functionalised nanomagnetic particles demonstrate efficiency in removing pollutants like cadmium from drilling fluids, addressing environmental concerns.
In the domain of cementing, nanoparticles are enhancing oil well cementing practices. Nano silica accelerates the transition from slurry to solid phase, improving cement strength and reducing porosity.
This advancement addresses issues related to cement integrity and wellbore stability, further highlighting the role of nanotechnology in improving drilling operations.
The Shale Membrane Tester (SMT) has revealed the effectiveness of silica nanoparticles in blocking shale pores, thereby maintaining low pressure and permeability even after prolonged flushing with brine.
This suggests that functional nanoparticles can significantly enhance drilling fluids by stabilising emulsions and improving efficiency.
Challenges associated with drilling in extreme environments, such as deepwater or high-pressure zones, have been addressed through the incorporation of nanoparticles.
These materials help mitigate issues like fluid loss, rheological changes, and wellbore instability by creating less permeable filter cakes and enhancing sealing.
The development of high-strength steel and the use of nanoparticles for polishing and smoothing surfaces further exemplify the advancements driven by nanotechnology.
Nanotechnology is also making strides in cement technology, with innovations such as viscosity enhancers, self-healing additives, and nano sensors.
These advancements contribute to improved well integrity and durability, with self-healing additives and nano sensors offering valuable insights into cement consistency and performance.
In the broader context of oil industry practices, nanoparticles are addressing challenges related to heat loss and fluid management in deep wells.
High-viscosity, high-temperature insulating packer fluids and surface treatments utilising nanoparticles offer benefits like reduced abrasion, corrosion, and enhanced separation efficiency. Nanotechnology is proving to be a versatile tool in advancing oil and gas extraction technologies.
Nanofiltration (NF) technology, which removes multivalent cations and submicron-sized organic matter, is gaining traction in various industrial applications.
Ceramic NF membranes, despite challenges with fouling, are increasingly used for water purification and extraction of valuable substances from oil and gas reservoirs.
Research is also exploring NF's role in removing harmful gases like hydrogen sulfide and carbon dioxide from natural gas streams.
The challenges of drilling geothermal wells are similar to those in oil drilling, with high costs and technical complexities posing significant barriers.
Nanotechnology offers potential solutions by enhancing drilling fluids, equipment durability, and real-time monitoring.
While scaling up nanotechnology presents challenges such as cost and environmental impact, ongoing research aims to overcome these obstacles.
Collaborative efforts between regulatory bodies, industry stakeholders, and academia will be crucial in realising the full potential of nanotechnology in both geothermal and oil sectors.
Overall, nanotechnology is reshaping the oil and gas industry by addressing complex challenges, improving efficiency, and paving the way for future innovations.
Its transformative impact is evident across various applications, from enhancing drilling fluids and equipment to advancing cementing practices and environmental stewardship.
As research continues, nanotechnology promises to drive further advancements, marking a significant leap forward in the field.
By ZAINAB AL TAITOON