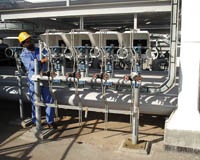
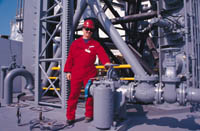
ONCE AGAIN Bahrain National Gas Company (Banagas) had what the board of directors described as a 'satisfactory' performance last year, building on 22 years of progress.
The company last year announced the operation of an advanced business information system via the Internet.
This year began with the appointment of Dr Shaikh Mohammed bin Khalifa bin Daij Al Khalifa as the company's new chief executive.
Dr Shaikh Mohammed had been with Banagas two years previously, and now oversees a company which is still playing a key role in the development of Bahrain's oil and gas industry.
Banagas operates LPG plant facilities to recover propane, butane and naphtha from associated gas and non-associated Arab Gas. The plant's production capacities are 3,600 bpd of propane, 3,000 bpd of butane and 5,000 bpd of naphtha.
The plant's two gas processing trains have a total gas feed capacity of 280 million cu ft per day.
The feed gas is collected from the Bahrain Oilfield. It is separated in gas oil separators at a controlled pressure of about 35 psig, and the separated gas is then sent to six compressor stations.
The gas is compressed to approximately 420 psig, then is cooled by air fans to 110 deg F, and dehydrated.
During this process, some gas is condensed and sent to Banagas' Central Gas Plant. But the compressed gas contains some water vapour and acidic gases such as carbon dioxide and hydrogen sulphide.
To avoid corrosion, the compressed gas is dried in a glycol dehydration unit before being pumped through gas pipelines to the Central Gas Plant.
The two trains at the Central Gas Plant are identical and use refrigerated lean oil-heavy naphtha to recover LPG from the feed gas. Each train consists of condensate, absorption, fractionation, treating and intermediate storage sections.
Condense System
Condensate from the compressor stations and from the gas separation system is distilled in a stabiliser column to remove light gas components such as methane and ethane. The stabilised condensate is fed to the depropaniser, while the light gases join the inlet associated gas.
Associated gas enters the separation section where liquids are removed. Solid residue is separated and removed.
Gas Absorption System
The gas leading the separation system is dehydrated to a dew point of -45 deg F to prevent the formation of hydrates in the subzero absorption section.
In the absorber column, the refrigerated feed gas and lean oil are mixed at a temperature of -35 deg F to allow the lean oil to absorb the LPG products of propane and heavier components from the gas and become a rich oil. The residue gas leaves the absorber to be used as fuel gas by Banagas and neighbouring industries.
The absorption of LPG is accelerated by high pressure and low temperature. Refrigeration of the feed gas and product streams is provided via a closed loop circulation of refrigerant propane using compressors at each train.
Fractionation Section
The Fractionation System separates the stabilised condensate and the rich oil still overhead into propane, butane and naphtha.
A deethaniser removes ethane and lighter components from the rich oil to maintain a maximum of two per cent ethane in propane. The overhead vapour is recycled to the Absorber System to remove any escaped propane and heavier components. The deethaniser bottoms are fed to the rich oil still column.
Depropaniser and Rebutaniser
The condensed LPG product and stabilised condensate are fed to the depropaniser column. A distillation process occurs, where the light components of propane are separated and condensed in a reflux condenser prior to sending to the treating section.
The lighter components of butane vapour are separated and condensed in a reflux condenser prior to sending to the treating section.
Treating Section
Propane and butane contain contaminants such as hydrogen sulphide, carbonyl sulphide and mercaptans.
Propane and butane are treated in a fluidised bed of solid potassium hydroxide to remove carbonyl sulphide and mercaptans. Prior to this, propane is treated by Diethanol Amine solution to remove hydrogen sulphide.
Bullets and Spheres
Treated propane and butane products are sent to four horizontal tanks (bullets). It is circulated and analysed for purity and water content, then sent to spherical tanks.
While under-specification product is returned to the Central Gas Plant, 'on-spec' product is pumped to refrigerated storage. 'On-spec' naphtha is pumped directly to the Bapco refinery for storage and export.
Refrigerated Storage
Liquid propane from the Gas Plant is received into a surge drum at 356 psig and 120 deg F. Some of the propane is used as refrigerant, first in the butane chillers and then in butane sub-coolers.
During this process butane is cooled to 25 deg F and liquid propane is flashed into vapour. The balance of the propane is flashed to its boiling point of -45 deg F into the propane storage tank.
The propane vapours from the storage tank, butane chillers and sub-coolers are compressed by reciprocating compressors. The compressed vapours are condensed and used as refrigerated propane to cool down both propane and butane products to their atmospheric boiling point of -45 deg F and 23 deg F respectively.
Each product is stored at its boiling point in separate refrigerated tanks of 200,000 barrels capacity.
Product Shipping
Shipping facilities consist of two loading pumps, each with a rated capacity of 5,000 barrels per hour, a 16" loading line and a 10" vapour return line, each of which is fitted with fully articulated arms.
Prior to the vessel's arrival, the loading line is cooled with the product to be loaded. The vapour generated is returned to its respective tank. The loading and vapour return arms are then connected to the ship and loading commences at a low rate.
As conditions in the loading system allow, the loading rate is increased to a maximum of approximately 10,000 barrels per hour.