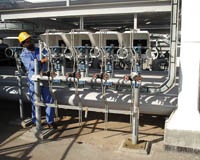
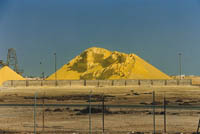
Since 1936 state-owned Bahrain Petroleum Company (Bapco) has been an integral part of the country's hydrocarbons industry.
Bahrain's only refinery processes 250,000 barrels per day (bpd) of crude, with five per cent of production consumed locally and 95 per cent exported to India .
The refinery is now undergoing a major strategic investment programme, the largest ever at the plant, aimed at improving profitability through modernisation and expansion, as well as meeting new environmental standards.
The $800 million project is, according to officials, critical to the refinery's future as a strategically-important plant in the Gulf region.
It comprises both installation of new facilities and the upgrading of several existing units.
The main element of the programme is the estimated $580 million low sulphur diesel production (LSDP) project, which aims to meet more stringent diesel sulphur specifications now common throughout the world.
A detailed feasibility study was carried out in 1997, the objective of which was to review potential future diesel specifications and to calculate the most economic refinery configuration to meet these product requirements.
The environmental acceptability of diesel is reflected in three specifications, namely sulphur content, the cetane number and aromatics content.
The current average sulphur content of the refinery's diesel product is 0.75 wt%, higher than the expected specification of most countries in the near future. Thus, the LSDP will reduce sulphur content to 0.05wt% to satisfy Bapco's traditional markets, and 0.005wt% for European customers.
A new Heavy Vacuum Gas Oil hydrocracker, with associated hydrogen production and sulphur recovery facilities, is being installed, while some existing units in the refinery, including the mild hydrocracker, will be put into diesel hydrotreating service.
Last November, a $12 million technology licence agreement was signed with the US' Chevron Lummus Global for the main 40,000 bpd high conversion hydrocracker. The company joined four other US licensors already working on the project: UOP for the 70,000 bpd diesel hydrotreater; Kinetics Technology International (KTI) for the hydrogen plant; TPA for the sulphur recovery and sour water treatment facilities; and Mobil, Akzo Kellogg (MAK) for the hydrocracker revamp.
With the US' Bechtel due to complete the front end engineering and design (FEED) package in June, Bapco is gearing up for the launch of the engineering, procurement and construction (EPC) tender, and hopes to bring the new plant onstream by 2004.
While the LSDP project is still only in the design phase, other packages in the upgrade programme are nearer completion.
The $66 million in-line blending project, which is expected to earn Bapco an additional $17.5 million a year, was commissioned last summer.
Prior to the project, blending operations were based on manually-controlled sequential batch blending of all products.
The new facilities enable Bapco to redistribute blending pools for increased production of higher value finished products, minimise give away on product specifications and improve safety. In-line blending also provides a more profitable use of blending components, offers flexibility to respond to market conditions and reduces inventory requirements.
The project consists of three automated in-line blenders, for diesel, gasoline and fuel oil. An advanced computer control system enables the blending of components to exact client specifications.
Construction of a new $27 million keromerox plant by JGC Corporation of Japan is scheduled to start later this year or early next year. Japan's JGC Corporation was awarded the EPC contract for the project which, unlike other packages, was driven more by environmental considerations than profit.
''The existing jet fuel production methods were fairly obsolete and had adverse environmental effects,'' said one Bapco official.
Indeed, Bapco's kerosene treatment facilities used a lead sulphide-based process which posed environmental risks.
The new 50,000 bpd two-line treatment plant will eliminate the need to use lead in the treatment process and improve jet fuel production efficiency.
In the presence of the proprietary 'merox' catalyst, sodium hydroxide and air, mercaptans (ringed sulphur compounds) in kerosene will be converted to disulphides. The reactor effluent will be processed to remove entrained caustic water and then filtered to improve the product characteristic.
A $31 million EPC contract was awarded to France's Alstom last year for instrumentation and process control facilities at the refinery for low sulphur fuel oil and fluid catalytic cracking complexes. The Instrumentation Modernisation Project would include the construction of a blast-resistant control room.
The revamp of instrumentation facilities is expected to increase profitability and revenue for Bapco.
Last year, Bapco launched unleaded gasoline production for both domestic and export markets. The Platformer Unit was modified to manufacture a higher octane gasoline blending component, with methyl tertiary butyl ether (MTBE) added as an octane supplement.
The unleaded gasoline project cost $7 million.
Other projects as part of the Bapco upgrade are a $22 million wet gas compressors replacement project, under which Bapco is installing a new single centrifugal compressor driven by a condensing steam turbine
Product yield from the refinery's largest vacuum column will also be enhanced when Bapco installs a new three-stage vacuum ejector system which will result in improved operation and unit profitability.
Finally, shipping facilities are being upgraded at Sitra, including the consolidation of lines and shipping pumps.