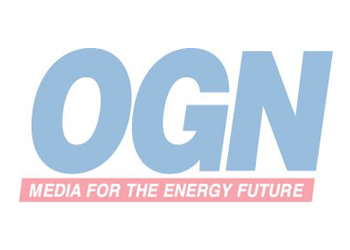

Alkhorayef Industries Co is the industrial arm of the Alkhorayef Group of Companies which has been in business since 1957.
Alkhorayef Industries Co, along with the other companies, that comprise the Alkhorayef Group, have been significant contributors to the unparalleled growth and modernisation of the Kingdom's industrial and agricultural sectors. Alkhorayef Industries Co is a highly diversified and vertically integrated metal-working business, producing a wide range of industrial products, in several ISO 9000 Certified manufacturing facilities:
Mechanised Irrigation Systems Factory
Among the three largest mechanised irrigation systems manufacturers in the world, producing centre pivot irrigation systems and linear irrigation systems, which are sold internationally under the name brand Western(r).
Polyethylene Lining Systems Factory
Utilises a unique patented process produce irrigation pipes with an integral High Density Polyethylene lining, which is sold under the name brand Per-mapipe(r) and offers the best available solution to solve corrosion problems.
Vertical and Horizontal Centrifugal Pump Factory
Manufactures complete lines of Vertical Turbine Pumps, Submersible Pumps, and Horizontal Centrifugal Pumps sold under the name brand Western(r), for use in municipal, industrial, commercial and agricultural applications.
This factory also produces Right-Angle Gear Drives, under the internationally recognised name brand Randolph(r), which range in size from 20 Hp to 1500 Hp.
Custom Engineered Products Division
Combines the engineering skills and manufacturing capabilities of the various Alkhorayef Industries Co factories, to design (employ reverse engineer where necessary) and produce custom metal parts for industry, petroleum businesses and other sectors.
Alkhorayef ERW Steel Pipe Factory
The Alkhorayef Pipe Factory, in production since 1990, is the leading Kingdom manufacturer of Electric Resistance Welded (ERW) steel pipe in sizes 21/2 " to 8 5/8" diameter and in thickness from 2mm-8.2mm with pipe lengths ranging from 13.1 ft-44.2 ft. The factory has an annual capacity of 42,000 MT.
Alkhorayef Pipe Factory utilises the latest in automated pipe manufacturing technology to provide its customers with the best quality it's the lowest price available. The pipe is produced in an ISO 9000 certified factory, to the most popular world standards for ERW steel pipe, including:
• API 5L Gr. A & B.
• ASTM A53 Gr. A & B.
• BS 1378
The factory is equipped with a pipe mill manufactured by BAUER, a leading European manufacturer of pipe mills, utilizing the latest technology available (High Frequency Induction welding and Heat Treatment of welds on stations produced by THERMATOOL, etc).
Slitting Line
The pipe factory is equipped with a slitting line, manufactured by BRANER-USA the slitting line is capable of slitting Hot Rolled Coil (HRC) with widths up to 1550 mm and thickness up to 10 mm in up to 17 strips.
The line has an annual slitting capacity of 90,000 MT, which is more than required for the pipe factory, and contract slitting service is available to other manufacturers.
ERW Pipe Production
The manufacture of electric resistance welded (ERW) steel pipe commences with the slitting of a large master coil of hot rolled steel produced by a steel rolling mill to: a) remove rolling imperfections from the master coil edges and to provide a precise master coil width and b) to cut the master coil into several narrower pipe coils with precise width's designed to produce a specific pipe diameter when rolled formed into a pipe and with good coil edges to facilitate quality pipe welding.
The pipe coils are fed into a pipe mill and through a set of form rolls to designed to procure the desired circular shape and size.
The rolled steel form then feeds through a High Frequency Induction welding station for the ERW welding process which begins with the converging edges of the of the rolled steel pipe being heated to a glowing red plastic state and then is fed through a forging process utilizing squeeze rolls.
The welded pipe is then fed through a station where the under side of the weld bead is removed by means of a scarfing tool maintaining a uniform pipe wall thickness and an unobstructed flow path.
To insure a quality weld is maintained and that pipes meet all applicable standards, welded pipe is fed through an annealing station in the pipe mill where the welded zone of the pipe is slowly heated to 900 degrees centigrade using low frequency induction heat following welding in order to restore grain size, to reduce internal stresses and counter act martensite inclusions.
Marketing Plan
To take advantage of new opportunities developing in the Saudi Arabian oil and gas sectors, Alkhorayef Industries, Co is focusing on taking advantage of our unique marketing advantage in the Kingdom of being the only manufacturer in the Kingdom for ERW carbon steel API 5L sizes 4" & 5".
Alkhorayef Industries, Co has not only been successful with its product in the Kingdom and the Middle East, but has also been successful in penetrating new global markets including the US, Europe, Australia, New Zealand, China, Middle East and North Africa.
Product application of Alkhorayef Industries, Co
Include: Oil And Gas Pipes, Irrigation Pipes, Column Pipes, Casing Pipes, Fire fighting Network Pipes, Water cooling System Pipes, Structutal Pipes
Alkhorayef Quality
The Alkhorayef Industries, Co factory is ISO 9001:2000 certified; The QA system not only addresses quality issues, but also addresses safety and environmental issues with particular emphasis on customer satisfaction.
The pipe factory facility has testing facilities for maintaining quality of its products:
• Physical inspection prior to slitting.
• Tensile test: test characteristics regarding yield, tensile strengths and elongation.
• WIP Testing: Eddy current test: for detection of defects at weld seam with reference to a predetermined control limits
• Flattening test: to check the integrity of weld, where the sample shall be flattened cold between parallel plates up to 2/3 OD. The weld shall be placed at 0 and 90 degrees from the direction of the applied force, or as the standard specify.
• Hydrostatic Testing: at specified duration and pressure according to standards to reveal the undetected seam weld defects.
• Finished Goods Testing:
Finished products are visually inspected for external defects prior to shipment (mainly, material handling defects: dents and other damages).