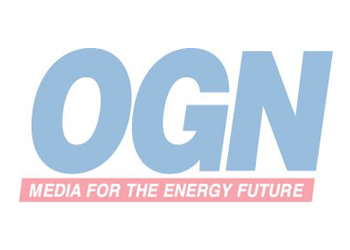

At a time when operators are seeking to minimise or postpone shutdowns, yet the effects of neglecting vital maintenance are all too evident, services that allow pipelines, platforms and refineries to remain operating and earning while maintenance work is carried out are of high value.
Services such as hot tapping and line stopping, and on-line pressure leak-sealing, as well as on-line valve testing all have a key role to play here, according to Furmanite, the technical services company geared to maximising asset uptime.
On-line leak sealing, for example, to repair or reinforce a leaking pipeline or a line suffering wall thinning that could lead to leakage is now widely accepted and proven, the company says.
Referring to Furmanite’s contracts to supply leak sealing and composite repair services to Algerian wet gas project In Amenas Operations (IA) and to the In Salah Gas project, business manager Paul Smith points out that these services can provide a temporary or permanent repair, and can be applied on-line while production continues.
A project for another operator, for example, saw shutdown of a crude oil trunkline avoided after wall thinning on an elbow was discovered in a remote desert location, in this case thanks to an on-line non-intrusive repair using a bespoke self-sealing FurmaSeal clamp.
FurmaSeal clamps offer repair and reinforcement, onshore, offshore and subsea, without requiring sealing compound, Smith points out.
“The split sleeve fittings are deployed with flouro-elastomer seals which are compressed and loaded by bolting around each end of the clamp and between the two clamp halves to produce a high integrity seal,” he explains.
“Held as a contingency measure, these enable repairs to be undertaken quickly and efficiently with no disruption to operation. Moreover, the latest cross-asset clamps can now be held as a contingency for a number of different lines, being able (through a system of interchangeable inserts and seals) to accommodate outside diameter variations of more than 30mm.”
The company has been awarded two contracts in the Caspian (where it is able to store contingency clamps locally at its Baku workshop and warehouse facility) to supply subsea repair clamps for oil, gas, condensate and water injection lines between the Central Azeri and Chirag platforms and Central Azeri and the Sangachal Terminal, and the Shah Deniz and Azeri in-field lines.
Elsewhere, Furmanite general manager Colin Bickerstaff points out, a leading Australian operator recently ordered a number of FurmaSeal clamps for subsea oil lines, and Furmanite Australia holds some 50 clamps of various sizes and classes for companies in the oil, gas and refining industries, in case of emergencies.
Moreover, leak sealing clamps need not be used solely to seal a leak, but to reinforce a weakened area to prevent one.
In one instance a major operator contracted Furmanite to design bespoke subsea sealing clamps to strengthen a 26 inch crude oil line suffering from wall-thinning caused by internal corrosion, thereby removing any leakage risks.The 1.2 metre clamps in this case were designed to encapsulate and seal three affected areas next to radial butt welds so that even in the event of continued wall thinning during the clamps’ 25 year design life, no leakage would occur.
“Even the move into deepwater beyond the reach of divers – while presenting greater challenges – does not preclude on-line leak-sealing options,” Smith points out.
“For instance, we successfully repaired one leaking seabed flanged connection at 500 metres depth, to enable oil production to continue at capacity. The bespoke clamp was installed on the 10 inch line (at the base of a water injection riser), and the specially formulated sealing compound mixed and injected, all by ROV.”
On-line maintenance and modifications
Services such as hot tapping and line stopping, on the other hand, can isolate a section of pipeline or piping systems to enable repairs (emergency or planned) to be undertaken, change out a malfunctioning valve or instrument, install instrumentation, add branch connections or even re-route the line, all while operation continues uninterrupted.
Bickerstaff cites a number of examples, ranging from a double 20 inch subsea line stop with 12 inch bypass on a high pressure gas line in over 200 metres of water, to a project involving installation of six high pressure subsea self-sealing hot tap tee clamps to allow solvent injection into a main crude oil pipeline on the seabed, to dissolve a build-up of deposits and release the restriction they were causing.
“In one instance, Furmanite used its hot tapping and self-sealing clamp expertise to install new in-line ultrasonic flare line monitoring equipment with no downtime,” he adds.
“The hot tap in this case (and in another instance where a 12 inch branch line was tied in to a 20 inch flare line) had to be performed at 45 degree angle, which means using extended pilot drills and cutters to accommodate the elliptical coupon produced, as well as measures to prevent deflection of the cutter assembly.”
Smith cites a further example in the Middle East in which hot tapping and line stopping enabled 12 block valve stations suffering from corrosion to be removed and replaced along a 200km section of a critical 1500km large diameter main crude export line, carrying 900,000 barrels a day, with no disruption to production, representing massive savings.
The prime benefits of these services is that even maintenance work traditionally undertaken during shutdown can now be done while operation continues, allowing operators to keep assets earning and extend intervals between shutdowns or reduce shutdown scopes without compromising maintenance.
A further such service lies in Trevitest on-line valve testing, which can allow valves to be recertified without shutdown.
A trial at one refinery saw 106 valves tested on-line under normal operating parameters, identifying these as needing no further work, while 60 more (originally designated as requiring shutdown to undergo standard PSV bench testing) were recertified in-situ and removed from the shutdown workscope.
Time savings were estimated at some 90 per cent per valve, enabling shutdown duration to be significantly reduced.
“These are just some of the wide range of on-line services available, allowing vital maintenance work or modifications to be undertaken without shutdown or where a shutdown is postponed,” Bickerstaff points out.
“In the current economic climate, when a number of operators are seeking to delay shutdowns or reduce scheduled outages, services such as these will help to minimise the impact by enabling necessary work to be undertaken while operation continues, to maximise asset uptime.”