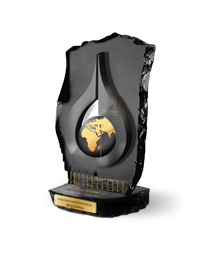
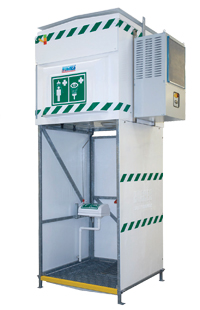
FOR effective decontamination, the internationally accepted American ANSI Z 358.1 2009 standard states that emergency safety showers should maintain a minimum flow rate of 76 litres a minute for at least 15 minutes. It also recommends the use of tepid water – 16-deg C to 38-deg C. If water is too hot or too cold, casualties are unlikely to remain under the shower long enough to ensure effective decontamination.
For showers operating in hot climates maintaining a safe water temperature is essential, particularly as ambient temperatures can rise to over 100-deg C. Self-draining showers are one solution, allowing water to drain from the standpipe and therefore avoid being heated by solar radiation. Together with thermal insulation, this may be sufficient. Where a reliable mains water supply is unavailable, many operators in the oil, gas and petrochemical industries use tank showers. In addition to providing a water supply independent of the mains, they also incorporate ancillary equipment to control the temperature of the stored water.
A recent tank shower supplied by Hughes for use in the Middle East highlights the features of a specialist hot climate shower.
This particular unit has a 1,200 litre capacity, sufficient to meet the water flow and duration specified in the ANSI standard even if the mains supply is disconnected.
Other sizes are available but smaller capacity tank showers must be plumbed into the mains supply to ensure they meet the minimum requirements. Regardless of size, the main consideration is temperature control.
High thermal resistance polyurethane insulation a sun shield on the top of the tank reduce the effect of solar heating. In addition, a compact and highly efficient chiller unit is attached to the outside of the tank. Water constantly circulates through the chiller and when the temperature starts to rise, the unit switches on to keep it within the specified safe limits. The chiller, which can be retrofitted to existing tank showers, can also be supplied suitable for zone 1 hazardous areas.
Where high temperatures during the day are followed by cold nights it may also be necessary to fit an immersion heater in the tank.
If a large number of showers are to be installed in a hazardous area, fitting a zone 1 compliant chiller to each one can add significantly to the cost.
An alternative, developed by Hughes, is to cool water in a centralised chiller unit installed outside the Zone 1 area and then circulate it to the showers through an insulated ring main.
Most safety showers are fitted with an alarm to summon help once the shower is activated. This may be initiated using a proximity switch on the shower or a flow switch in the pipework.
Safety showers and eyewash units should be tested every week to ensure they are working properly. Routine maintenance is also crucial and can be carried out in-house or by an experienced service provider. Whoever is responsible the aim should be to minimise unit downtime to ensure that your investment in safety is always ready for action.