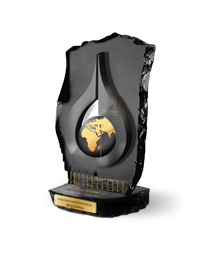
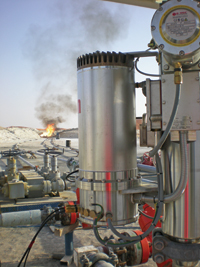
IN 2006, the Norwegian technology company Multi Phase Meters (MPM) developed and qualified the first true combined multiphase and wetgas flowmeter. The technology uses electromagnetic tomography techniques to provide high accuracy and high frequency measurements of oil, gas and water production without the need for physical separation.
Initial development took place through a Joint Industrial Project (JIP) in partnership with Statoil, Shell, Total, ConocoPhillips and ENI. Since then, more than 220 MPM meters have been sold to subsea and topside projects worldwide.
A third JIP started in 2010 to further develop the advanced software functionalities in the MPM meter and which have focused on development of an integrated in-situ verification system.
After a MPM meter has been successfully installed in the field, the purpose of the in-situ verification system is to provide the user with documentation of the integrity of the measurements from the meter and to further improve the robustness and accuracy of the measurements.
The in-situ verification system is based on redundant measurements from the MPM meter; using additional equations and statistics to verify that the sensors in the meter are working fine and that the measured values, the system configuration, fluid properties and process, voltage and temperature (PVT) parameters are correct. Parts of the system are accessible to the user through the Graphical User Interface (GUI), whereas others are managed by MPM.
In-situ verification can either be done at the well site, or preferably remotely from the MPM Operations Support Centre located in Stavanger, Norway. However, remote surveys require that the MPM meter is “online” and accessible to MPM through a secure IP network.
The in-situ verification system and the associated reports can be used for documenting the MPM meter´s performance internally and towards MPM, third party and the authorities. Should there ever be an issue with the MPM meter; the system will also assist the user (and MPM) to identify the cause of the issue before even sending someone to the field for troubleshooting.
MPM meters can be delivered with an integrated diagnostics software tool for analysing the integrity of the various sensor components in the meter. All the main parameters (several bounded variables) involved in the routines for flow calculation can be analysed in separate interface windows where instantaneous values in addition to statistical parameters, such as average, minimum, maximum and standard deviation, are displayed.
The in-situ verification system allows verification of the hardware sensors but also the configuration data entered in the MPM meter, and it will suggest corrections for PVT properties input if these will prove to be different from the measured PVT properties.
Having exact knowledge of the actual gas density and the actual gas permittivity is very important in order to eliminate distorting effects of uncertainty in the configuration data for the gas. The measured PVT properties can be used for validation of the general PVT data or as a reference if such data do not exist or is outdated. The MPM meter can also be configured to automatically update the input gas PVT data based on the in-situ measured gas parameters and consequently be a tool for improving the all over measurement robustness and accuracy.
The result of the in-situ verification routines serves several purposes such as:
• Document measurement integrity and PVT configuration data;
• Document meter performance which can be used towards partners and authorities;
• Reporting of faulty conditions and abnormal behaviour of a meter;
• Detection of erosion and scale/wax build-up and possible compensation for this effect on the measurements;
• In-situ analysis of the PVT input configuration data and automatic update if any changes in the parameters of the well fluids;
• Document the measurement effect of recommended corrective actions or upgrades of the meter software and configuration; and
• Reduce sensitivity to uncertainty in fluid properties and therefore improve the quality of the measurements.
The system has full traceability. Each time a change is made in the meter configuration it is recorded as an event in an event log. A configuration report can be retrieved from the meter at any time which lists in detail the configuration parameters and the software versions installed on the MPM meter and the MPM terminal computer. The configuration report can be stored as an xml file and option for automatic distribution at selective frequency to e-mail or to a network printer.
Some of the in-situ verification routines can be fully automated and the result is stored on the MPM meter and/or the MPM terminal computer. Other routines require manual interaction with the meter by MPM.