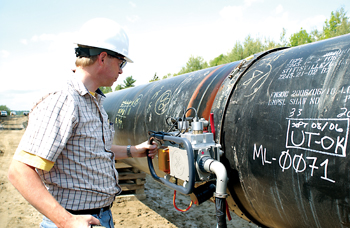
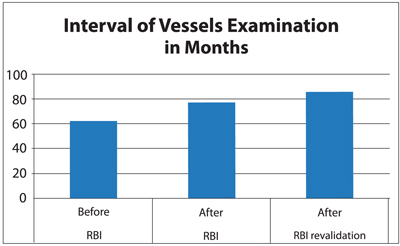
CRITICAL equipment such as pressure vessels, piping systems, and storage tanks are often subject to risk-based-inspection (RBI) to deliver optimum inspection policy and control of risk. As equipment life matures and businesses evolve, revalidation of the existing RBI’s will ensure they remain fit for purpose and evergreen.
WHAT IS RBI?
RBI is a methodical process to determine the optimum inspection scheme for industrial pressure equipment. The process involves a structured review of equipment aspects to firstly identify potential damage/deterioration mechanisms for assessment against the health, safety, environment (HSE) and business risks. An appropriate inspection policy can then be determined to deliver reduced risk and an optimised inspection regime. This often provides the added benefits of reduced costs and resources by having more focused inspections for the risks identified.
In 1996 the American Petroleum Institute (API) published API 581 (Risk Based Inspection – Base Resource Document). This documents the methodology that has become adopted worldwide as the basis for the RBI process.
WHAT IS RBI REVALIDATION
RBI reviews are generally carried out for key critical equipment at either their early life stage, or at some point in their lifecycle, often driven by integrity and/or budget considerations.
Revalidation is a process to review existing RBI’s to check the assumptions made from initial review are still valid and that nothing has changed that would adversely affect the risk. RBI is based on operational, design, inspection and maintenance data available at the time of review. More data will be added throughout the equipment life cycle which may confirm or contradict assumptions made from original RBI.
Due to the nature of risk assessment, a conservative view is often taken during initial RBI reviews, particularly those completed during early life of the equipment where there is limited operating and inspection history. As a result, initial inspection requirements can often be set on the cautious side until more history and confidence is gained.
![]() |
Figure 1: RBI and Equipment Life Cycle |
Revalidation helps to further optimise inspection schemes and ensure that risks are appropriately managed by either increasing inspection requirements where history shows evidence of deterioration and/or ageing, or reduce inspection where little or no evidence of deterioration is found. Inspection periodicity is reviewed and potential for non-invasive inspection is also considered where appropriate. This revalidation process helps keep the RBI’s evergreen and fit for purpose in an increasingly challenging regulatory and business environment.
WHEN SHOULD IT BE COMPLETED?
Ideally RBI’s should be reviewed after each main inspection to record the findings and check that the original assumptions are still valid. If there have been unexpected failures or repairs, then RBI revalidation can also be a valuable process in establishing root cause to prevent reoccurrence. As plant begins to enter its aging phase of lifecycle, RBI revalidation will ensure inspection periodicity is safely within corrosion rate allowances and any limited life restrictions that may be relevant such as creep and fatigue.
WHO SHOULD BE INVOLVED?
RBI validation should preferably be carried out by an independent person experienced in inspection and integrity to give a balanced view. Representatives from operations, maintenance, inspection and any specialist support such as materials/corrosion and functional engineers will also need to be consulted as necessary during review.
RBI REVALIDATION PROCESS
The process for carrying out RBI revalidation starts with a review of operating history to check there are no significant changes in key aspects such as process fluid composition, temperatures and pressures, steady to cyclic operation, decontamination/commissioning methods etc. Any corrosion control/monitoring programme can also be reviewed to ensure this is being completed as required and that the results are within expectations.
Inspection findings are then reviewed against assumptions from original RBI. Have unexpected deterioration mechanisms occurred that are not accounted for? Are deterioration rates and location(s) as per expected? Corrosion rates between inspections should not be greater than 50 per cent of corrosion allowance. Or is the corrosion rate much less than expected?
The original RBI may have made assumptions about the maintenance program when deciding upon likelihood of failure scenarios, for example, cathodic protection system fully functional and adequately maintained, vibration monitoring takes place for adjacent rotating equipment which would detect potential for imparted vibration. These should be audited to confirm they are as stated in the RBI. Maintenance history may include failures or repairs not included in inspection reports or any maintenance work carried out as a result of “one-off” process excursions.
HSE and business consequences can change over time. Changes in personnel occupancy levels, new equipment installed nearby containing toxic/flammables, change to single stream operation, reduced stock capacity on site. These are all examples that may affect the overall risk and warrant change to the inspection regime.
RBI is often used to establish an appropriate inspection programme before equipment enters service. If for a new application (process or materials), the original RBI may have recommended “one-off” inspections to confirm the possibility of very low likelihood deterioration mechanisms occurring. This requirement can be removed from the inspection programme if no issues are found at inspections. The outcomes of RBI revalidation can be either, the RBI and inspection programme are still appropriate, minor changes are required to the RBI and inspection programme, or the RBI is no longer valid and needs major revision to produce a new inspection programme.
RBI AND EQUIPMENT LIFECYCLE
The potential degradation of plant and equipment due to age related mechanisms such as corrosion, erosion and fatigue is a key issue for industry. The Health and Safety Executive have recognised asset integrity management and the issue of ageing plant as key topics to address in their inspection programmes. (HSE Research Report RR823, Managing Ageing Plant).
Later Life can be defined as after 80 per cent of design life, which may be based on corrosion rate/allowance, number of operating cycles or creep life. As additional aging mechanisms become relevant in later life a thorough review of the RBI is recommended. Combining the RBI review with a Fitness for Service assessment is often used to determine if the operational life can be extended (see Figure 1)
RBI REVALIDATION, NII STRATEGIES
RBI may determine that a non-invasive inspection (NII) strategy is appropriate. The decision for NII suitability is dependent on the operating conditions being well understood and controlled such that any degradation can be adequately identified and monitored via a non-invasive inspection strategy and that the consequences of failure are not significantly high. For these cases, it is particularly important that RBI revalidation takes place and is essential when the equipment enters its later life phase.
CASE STUDY
ABB undertook RBI studies with an oil and gas customer with facilities onshore and offshore, the project included over 1,000 items including vessels, storage tanks and 15 km of piping systems. The study team included operations, process, maintenance and inspection representatives and used a qualitative RBI approach. Following the next examination, RBI revalidation was undertaken to check the assumptions made during the study and the results of one-off examinations to provide evidence of deterioration mechanisms that were thought to be low likelihood. A key focus was identifying whether the examination could be undertaken via NII. Following the initial RBI over 50 per cent of the vessels were moved to NII and the RBI revalidation verified this approach.
Figure 2 shows the average interval between examinations and this change to the average following the initial RBI and after RBI revalidation. The customer saved over £2.2 million ($3.42 million) in inspection costs, but the great benefit was the reduction in downtime of the equipment and the lower risk profile due to understanding of the specific deterioration mechanisms.
ADDITIONAL BENEFITS OF RBI REVALIDATION
Independent RBI revalidation can also verify that the inspection programme defined is suitable to detect the deterioration mechanisms listed and that it is being completed as specified by the RBI.
SUMMARY
RBI’s and inspection programmes should be ‘live’ documents subject to regular revalidation. Revalidation will identify if major changes are needed and will allow the inspection programme to be optimised.
RBI revalidation does not need to be expensive or time consuming, in most cases each review takes less time and resources than the original review. An independent person with experience in inspection and RBI should be considered to perform RBI revalidations.