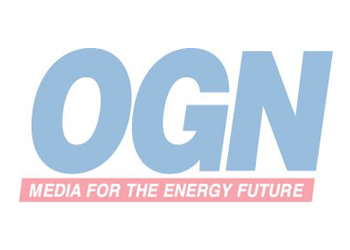
Ethane produced from the plant will be used as a feedstock for the Qatari petrochemical industry
Rasgas Company Limited (RasGas) has announced that Train 1 of its historic Barzan Gas Project (BGP), which will play a significant role in meeting Qatar’s rapidly growing domestic energy demand, is more than 95 per cent complete and is rapidly ramping up for first production of clean-burning natural gas in 2015.
Construction work on Train 2 is also progressing well with expectations to be completed in 2015. Once completed, the two processing trains will produce around 1.4 billion standard cubic feet a day (bcfd) of sales gas. Combined with RasGas’ other facilities production (LNG and sales gas), the BGP is set to make RasGas one of the largest single gas processors in the world with a production capacity of 11 bcfd.
In addition to sales gas, Barzan will produce about 22,000 barrels per day (bpd) of field condensate, 6,000 bpd of plant condensate, 34,000 bpd of ethane, 10,500 bpd of propane and 7,500 bpd of butane.
Dr Mohammed bin Saleh Al Sada, Minister of Energy and Industry says: "The Barzan Gas Project is strategically important for Qatar’s sustainable economic development, and is a powerful step forward in the country’s overall industrial and human development, in line with Qatar National Vision 2030."
The construction of this mega-project, which includes both offshore and onshore facilities, started in 2011. The offshore facilities include three offshore wellhead platforms, subsea pipelines and cables. The onshore facilities are comprised of a gas processing unit, a sulphur recovery unit to remove impurities from the natural gas, and a natural gas liquids (NGL) recovery unit, which will produce methane, ethane, propane, butane and condensate. Ethane produced from the plant will be used as a feedstock for the growing Qatari petrochemical industry. RasGas was appointed by its shareholders, Qatar Petroleum and ExxonMobil, to design, construct and operate the BGP, which is one of the largest and most technologically advanced gas projects in the region.
The project has maintained world-class safety performance and industry-leading results for the last three years through a disciplined approach to process safety and relentless focus on accident prevention and continually improving project execution practices.
Emphasising the need for continued vigilance, Hamad Rashid Al Mohannadi, RasGas’ chief executive officer, says: "The Barzan Gas Project is a prime example of RasGas’ commitment to safety and excellence in project management and execution. I am proud to note that we have already achieved an unprecedented world-class safety record of 130 million man-hours without a lost time incident (LTI). I would like to thank our shareholders, contractors, employees and workers for this outstanding achievement given the complexity of managing a multi-national workforce of more than 30,000 people at peak construction in very challenging conditions."
Al Mohannadi also cites the company’s commitment to the environment as a high priority area where RasGas has taken significant strides in ensuring that the BGP facilities are built utilising the right technology and sound engineering design to operate safely and reliably.
Various innovative technologies and controls are being implemented to minimise adverse environmental impacts. These include using the best available technology (BAT) for combustion sources, utilising innovative start-up flare minimisation strategies, and undertaking environmental projects to protect coral and marine life. The facility will also utilise ExxonMobil’s Flexsorb SE Plus for tail gas treatment of the sulfur recovery plant which will allow the facility to achieve 99.4 per cent recovery efficiency, which will be the highest recovery efficiency of any gas treatment project in Ras Laffan Industrial City. Specialised burner technology has also been installed on fired equipment and gas turbines to help minimise nitrogen oxide (NOx) emissions.
As part of RasGas’ efforts to preserve marine life and protect biodiversity in its project waters, the company relocated around 1,600 corals living along the Barzan Gas’ pipeline route prior to construction. This was done in consultation with Qatar’s Ministry of Environment.
Another first that distinguishes the project is the number of Qatari nationals working on the project. The Barzan Gas Project has the highest number of Qataris, working in almost every key discipline, of any single RasGas project, thus ensuring that maximum exposure and experience are given to national graduates to develop their career in the Qatari energy industry.
This included embedding them with the project teams in Japan and South Korea throughout the different phases of the project.
Additionally, a broad range of Qatari companies have also been involved in providing essential support in terms of manpower, materials, equipment and services.
Several contractors played a key role in the planning, engineering, procurement, construction and development of the project including JGC Corporation and its sub-contractors for the onshore facilities and Hyundai Heavy Industries for the offshore facilities.