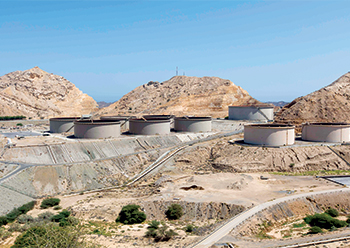
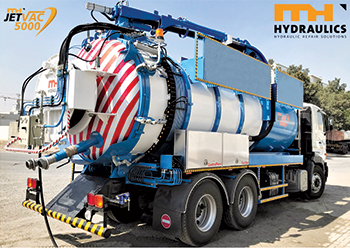
MH Hydraulics, a leading hydraulic solutions provider in the Middle East, provides guidance on how to measure contamination and highlights the importance of knowing your asset’s oil contamination level
Hydraulic equipment loses its usefulness primarily because pf surface degradation, mainly due to mechanical wear (50 per cent) and corrosive wear (20 per cent) caused by particle moisture contamination, respectively.
The international standard used to test and measure oil cleanliness levels for the fluid power industry in ISO 4406:1999. Another standard often used is National Aerospace Standard (NAS) 1638. Both NAS 1638 and ISO 4406 focus on the methods for calculating particle counts or solid contamination levels within a fluid. However, ISO 4406 gives a greater amount of useful data and is usually the preferred method.
Contamination can either come from external sources (ingestion) or is generated from within (ingression). Even if no immediate failure occurs, contamination can dramatically decrease operating efficiency and can accelerate component wear, which in turn leads to inefficient operation, seizure of parts, higher fluid temperatures, leakage, and loss of control.
Analysing the oil will indicate how the system is performing, prompting proactive maintenance to ensure performance and reliability. Samples taken initially will provide a benchmark while further routine samples will ensure the oil is in top condition and provide early warning of abnormalities so preventative action can be taken. When to take samples and what results should one look out for will be entirely dependent on the application and the Target Cleanliness Level (TCL) of a system. It is best to take a sample from the return line before passing through a return filter. For the powerful hydraulic applications that are running regularly at high pressures, secondary sampling points around the hydraulic components are recommended. This will allow to diagnose accurately where the build-up of debris/particle contamination occurs.
Once the asset’s lubricant condition is determined, a contamination control strategy must be drawn up and here it is important to set a target; and take action by installing desiccant breathers and adequate additional filtration systems.
It is vital to measure or take samples on a regular basis to ensure that the equipment is working safely and to be able to evaluate the effectiveness of one’s actions. It must be noted that it is mostly the tiny amounts of water and micron-sized particles – microscopically small that cannot be seen with our eyes – that cause the failures in assets like hydraulic systems, gearboxes, reducers, and pumps. The remaining life of the asset and lubricant is seriously jeopardised when systems are operating with contaminated oil or not operating with the required cleanliness level.
Implementing the right strategy to keep oil clean will result in increased overall equipment reliability, reduced downtime and maintenance costs; reduced environmental footprint; fewer breakdowns and oil changes, longer life of components and oil; and ultimately, higher returns on investment. So how often should one aim to analyse oil and what are the way to measure the contamination? The technical article in our online edition's Tech Talk section provides the answers.