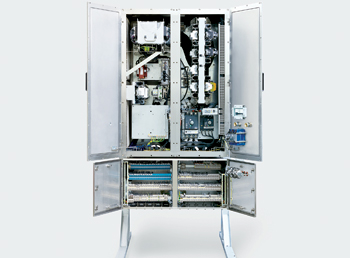
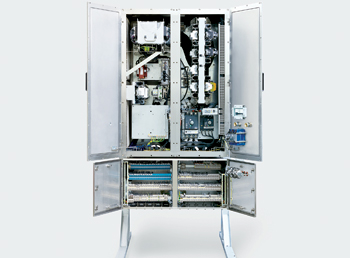
R STAHL's innovative EXpressure concept is a first in the field of enclosure engineering, and a superior solution to the existing enclosure encapsulation methods for many applications in the oil and gas industry
Quintessential
explosion protection requires comprehensive expertise especially with the increase in highly networked switching, control and communication systems that are incorporated in hazardous areas. This expertise is vital in order to safeguard against potential ignition hazards in these areas.In industrial environments where explosions can occur as a result of gas mixtures, mists, powders or dust, measures must be taken to ensure that a wide range of ignition hazards are safely eliminated.
The prescribed safety precautions to prevent these hazards are listed in IEC 60079 under the different types of protection. Electrical or electronic components without increased safety (Ex e) or intrinsic safety (Ex i) must not be used in Zones 1/21 and 2/22 unless additional design measures have been taken to ensure that they pose no risk of causing an explosion.
In principle, there are no restrictions on which type of protection you can choose and this grants a great deal of freedom to tailor the protection concept to the customer’s requirements.
In order to devise a solution that is not only a perfect fit for the customer’s technical specifications but also optimised in terms of initial acquisition and operating costs, the expertise that specialist manufacturers possess must, therefore, span the entire spectrum of Ex protection technologies.
INNOVATION IN ENCLOSURE ENGINEERING
R STAHL’s new EXpressure technology for Ex-protected enclosures is a solution that boasts a whole host of advantages over conventional enclosure encapsulation concepts.
The concept is a first in the field of enclosure engineering, and is a far superior solution to the existing enclosure encapsulation methods for many applications. This concept enables the construction of large yet lightweight Ex d switch cabinets that allow standard electrical and electronic components to be safely used in Zone 1.
Besides power distribution boards and control systems, EXpressure switch cabinets can also house large pieces of equipment, such as transformers or frequency converters, providing reliable explosion protection for everything installed within them.
PRESSURE RELIEF FOR ZONE 1
The new PTB- and DEKRA-certified EXpressure switch cabinet series features a unique pressure relief system. Special stainless steel wire mesh on both sides of the enclosure ensures that the pressure within the enclosure can be reduced effectively, serving as a flameproof barrier that allows for controlled flow of gas combined with heat absorption.
If an explosion occurs inside the enclosure, the energy released is absorbed swiftly, safely and effectively. Regardless of where the ignition source is located, only harmless incombustible and non-explosive gas/air mixtures are able to exit the enclosure.
The special mesh is also designed to absorb a significant amount of the heat energy that has been generated by the chemical reaction thereby safely lowering the internal pressure within the enclosure.
These features effectively reduce the internal pressure in the event of an explosion to a maximum value of less than 1 bar; sparks that might otherwise cause an explosion are safely contained inside the enclosure thanks to the special mesh structure.
The maximum surface temperature falls under temperature class T4. Covering the EXpressure enclosure’s pressure relief elements are explosion vent panels with a target pressure of 0.1 bar; these panels seal the enclosure and, under normal operating conditions, offer IP66 protection.
MORE CAPACITY, LESS WEIGHT
The Ex d-certified pressure relief technology offers up to 50 per cent space and weight savings compared to conventional Ex d solutions, and is a highly efficient, cost-effective alternative to Ex p pressurised enclosures.
Moreover, the new protection concept makes it much simpler to install switching and control units in Zones 1 and 2, near to the machinery that they control, rather than having to position them far away in a non-hazardous area.
The EXpressure technology comes in a choice of four enclosure sizes, ranging from 300 x 400 x 200 mm to 1000 x 1400 x 700 mm, and with either a single-leaf door or a double door. With walls just 2 mm thick, these stainless steel enclosures are extraordinarily light, making transportation, handling and installation much easier. Their optimised design also benefits from a smaller footprint.
The large, undivided space inside the enclosure provides easy access for installing and wiring switching components and for performing maintenance and inspection work. The volume available within the enclosure for installing equipment is comparable to that of many conventional industrial switch cabinets and control boxes, and allows the switchgear layout used for non-hazardous areas to be used unchanged for hazardous areas without any additional engineering work.
Thanks to the futureproof design of the enclosure concept, even last-minute changes to the order can be accommodated with little difficulty at the commissioning and SAT stages.
Cable entries can easily be retrofitted at any point in time, and new components can be added to pre-installed equipment. Control elements that have been approved for use with Ex d solutions, for example, rotary switches, pushbuttons, mushroom buttons, key-operated switches and control lamps, can all be used without modification. Additional accessories include Ex e connection shafts and inspection windows that are available in six different sizes.
LIGHT AND EASY
In terms of weight and size, as well as the amount of maintenance, conversion and retrofitting work required, EXpressure enclosure combinations are often a better choice than conventional Ex d enclosures.
The most widely used type of protection are the flameproof enclosures. These are usually incredibly bulky structures, which are built this way to withstand extreme explosion pressures in the region of 7-12 bar. To achieve the necessary pressure resistance properties, very thick walls of 10 to 20 mm are required.
Realistically for economic and for technical reasons, this limits the enclosure capacity to not more than around 500 litres. Large, complex electrical control panels and distribution boards must, therefore, be divided between a number of smaller flameproof enclosures.
Compliance with the applicable explosion protection requirements complicates the production and installation processes for these flameproof bushings, which are required in order to establish the necessary electrical connections.
All joints running through the enclosure wall must be flameproof. This is to ensure that sufficient energy is removed from any flames or hot gases in the area to prevent them from causing an explosion.
Any subsequent changes to the internal electrical wiring inevitably require extensive, time-consuming and costly modifications, which must normally be accepted by an explosion protection expert before the equipment can be put back into service.
With the advent of the new EXpressure technology, complete switchgear assemblies and distribution boards can now be housed in a single enclosure, saving significant amounts of space and cost, and making maintenance a whole lot easier. The amount of planning required is also considerably less. Additionally, components can be retrofitted, modified or replaced quickly and without additional costs.
NO PRESSURISATION REQUIRED
In order to house complex control and distribution systems within an explosion-protected enclosure alongside large-scale equipment and special machinery, solutions using pressurised enclosures (Ex p) have been required to this date.
Enclosures with this type of protection have air or an inert gas forced through them. The positive pressure created prevents explosive gases from entering the enclosure. To start operation inside Ex p pressurized enclosures, inert gas must be flushed through the enclosure to force out gas mixtures that have entered from hazardous areas and to create the positive pressure required for operation.
This takes time: frequent maintenance, replacement and conversion requires significant down time. However, installing equipment in line with EN 60079 2 requires various inspections and tests for positive pressure, leakage, test gas supply and pre-flushing time, which makes Ex p structures particularly complex.
Compared to this protection concept, the EXpressure is by far the more cost-effective alternative. Firstly, it eliminates the need for many expensive design and test steps. Secondly, the Ex protection remains intact at all times – during equipment start-up and after maintenance and retrofitting work – without additional time consuming procedures. And, of course, there is no need of equipping Ex p enclosures with a control unit, a feed air station and a pressure monitoring system.
For many applications, R STAHL’s EXpressure protection concept is an excellent alternative to the conventional Ex d and Ex p solutions used in hazardous areas; it is more cost-effective and more flexible than conventional solutions.
The pressure relief technology it uses makes retrofitting and conversion easier, which in turn makes it a particularly futureproof product. Last-minute changes to the order and upgrades can be accommodated with little difficulty. Their lightweight construction, large internal capacity and compact dimensions, combined with the simplicity that has been designed, makes workers’ lives easier and EXpressure enclosures the perfect choice for both tight spaces and offshore environments.
In addition, the project engineering plans used for non-hazardous areas can be used unchanged for Zones 1 and 2.
Control panels often have to be installed far from the system that they control. But now, with the explosion protection that the EXpressure enclosures provide, these control panels can be positioned in situations where the production process is taking place.
This means that the production process can be monitored much more reliably and enables the production rate to be increased. The amount of cabling and connection work is also considerably reduced with this new technology.