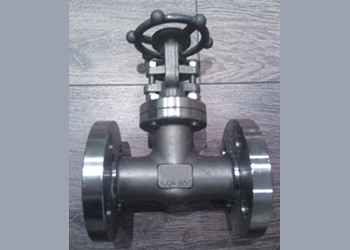
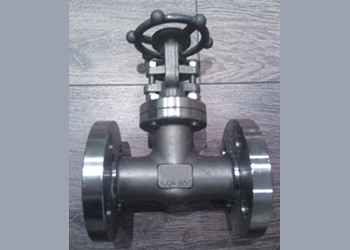
The valve requires minimum maintenance, adjustment and lubrication, and offers easy installation, low operating cost, long-term reliable operation, and no external leakage occurs
Flanged gate valve is considered the most mature on-off valve in the world and is widely used.
It is a more cost-effective choice for the industry because of the many advantages it offers, such as easy assembly, low failure rate and that it meets the automation needs of the industry.
Because of the use of general traditional pneumatic valves, it is inevitable to have piping, solenoid valves and compressors to match, while the flanged gate valve is driven by a motor, which is easy to install.
And the electric valve installation can be matched with the original automatic control circuit of the factory, which can save other costs.
In addition, the motor-driven way of opening and closing is relatively smooth, there is no shortcoming of excessive instantaneous impulse, and the failure rate can be greatly reduced.
According to industry people, in industrial processes, valves are mostly used to control the travel and flow of various fluids, such as water, oil, chemical liquids, etc, based on parameters such as temperature, pressure and flow.
The commonly used control valves in factories include pressure reducing valves, pneumatic constant temperature valves, solenoid valve constant temperature systems, proportional control valve constant temperature systems, and temperature control valves.
When selecting various types of automatic valves, factors such as the type of heat engine, the required accuracy, the quality of the control valve, the pressure drop, the flow rate and its structure, the failure rate, the manufacturer's credit and after-sales service should be considered in order to achieve economical and practical purposes.
CHARACTERISTICS OF FLANGED GATE VALVE
Flanged gate valve requires minimum maintenance, adjustment and lubrication. It offers easy installation, low operating cost, long-term reliable operation, and no external leakage occurs.
The valve body is welded, making the valve light and easy to insulate, and the adjustment mechanism is very simple. The operating handle can be detached and flipped.
![]() |
Flange gate valves have a wide application range |
Since the valve seat is composed of carbon fibre reinforced PTFE sealing ring and disc spring, it has strong adaptability to changes in pressure and temperature, and will not produce any sliding discharge in the pressure and temperature range on the label.
There are advanced computer detection and tracking detection in the process of sphere processing, so the processing accuracy of steel balls is high.
Since the material of the flanged gate valve body is the same as that of the pipeline, there will be no uneven stress, the pipeline will not be deformed due to earthquakes and vehicles passing through the ground, and the pipeline is resistant to aging.
In order to prevent static electricity, steel balls and springs are installed between the valve stem and the ball and between the valve stem and the stuffing box, which can maintain the conduction of all parts of the lined ball valve and the valve body, and discharge static electricity in the area where the current passes.
To prevent both fire and corrosion, temporary cutting is required for timely maintenance.
The valve stem anti-drop function is due to the total force generated by the valve stem affected by the pressure in the valve, so the design of the flanged gate valve stem is to prevent the structure from disconnecting.
ANTI-CORROSION WORK OF FLANGED GATE VALVE
In the process of valve production, the corresponding anti-corrosion work is indispensable, and the flanged gate valve is no exception; it anti-corrosion work is essential.
The anti-corrosion work of the flanged gate valve can be undertaken as following:
• The first is the selection of materials, which is the most important factor in preventing valve corrosion. Normally, cast steel valves are used for water, oil and gas.
If it contains corrosive media such as acid and alkali, stainless steel should be selected.
Generally, the temperature should be controlled below 200 deg C. Stainless steel will produce a passive film in the medium to prevent further corrosion.
The highly corrosive medium needs to be used at a high temperature, so the super corrosion-resistant alloy material should be selected.
The medium is reducible, and the stainless steel material containing Mo is selected; the medium is oxidising, and the stainless steel material containing Cr is selected.
• Surface coating: Paint coating the valve surface is also a commonly used anti-corrosion method. Spraying epoxy resin paint on the surface of the elastic seat flanged gate valve is such a treatment method.
• The medium is isolated from the flow channel of the valve body by using lining materials, which include engineering plastics, natural rubber and various synthetic rubbers, generally only at lower pressures and reduced operating temperatures.
• Surface electroplating valve surface chrome-plating, nickel-plating, copper-plating can also effectively achieve the effect of preventing corrosion.
MAINTENANCE OF FLANGED GATE VALVES
When a flanged gate valve is repaired, it is necessary to learn the relevant methods. If not, it should be carried out by professionals, otherwise it will easily lead to the damage of the flanged gate valves.
To carry out maintenance, first remove the pressure before and after the ball valve. The ball valve can then be disassembled and differentiated.
When the ball valve body is reinstalled, it is necessary to tighten the bolts symmetrically, gradually and evenly.
The cleaning agent should be compatible with the rubber parts, plastic parts, metal parts and working medium (such as gas) in the flanged gate valve ball valve.
When the working medium is gas, the metal parts can be cleaned with gasoline, and the non-metal parts can be cleaned with pure water or alcohol.
The differentiated individual parts can be cleaned by dipping. Non-metallic parts should be removed from the cleaning agent immediately after cleaning, and should not be soaked for a long time.
After cleaning, it needs to be installed after the cleaning agent on the wall to be washed has evaporated (it can be wiped with a silk cloth not soaked in the cleaning agent), but it should not be put on hold for a long time, otherwise it will rust and be polluted by dust.
The new parts also need to be cleaned before installation. When installing the flanged gate valve, no metal debris, fibers, grease (regularly used), dust, other impurities, foreign objects, etc, should be polluted, adhered or stayed on the surface of the parts or into the lumen.