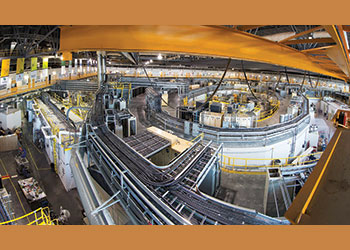

The oil and gas sector is losing significant sums annually to valve reliability issues in harsh environments. The introduction of self-cleaning components combining multi-stage labyrinth and cascade technology could prove a game changer in terms of plant safety, productivity, and profitability, says an industry expert.
'Clearly, the growing costs and frequent interruptions associated with valve shutdowns present an unacceptable situation for plant operators. Consequently, new innovations are required that solve the issue of clogging and seizing due to dirty contaminants at the source,' says Karl Wonisch, Head of Europe Control Valves at IMI Critical Engineering.
IMI Critical Engineering has developed EroSolve Metamorphic Trim (MMT), which uses a unique self-cleaning design and velocity control methodology throughout the whole fluid passage, reducing the risk of damage and clogging.
The trim, which is custom-designed to fit existing valve bodies and actuators, also benefits from the gradual divided pressure drops associated with cascade-style solutions, as well as reduced installation costs.
The EroSolve MMT was demonstrated at a glycol dehydration installation of a multinational oil and gas producer in the North Sea. With the application proving challenging due to high pressure drops, very low flow, solid particles and sludge in the fluid, material was regularly collecting at the bottom of the contactor, impeding passage through the control valve.
This resulted in unplanned downtime and annual production losses totaling £2 million. However, by implementing the EroSolve MMT, the high pressure drops, and small flow rates previously hampering performance could be mitigated.