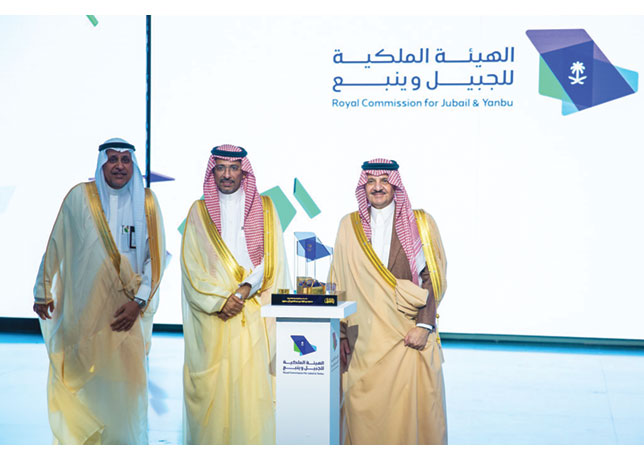
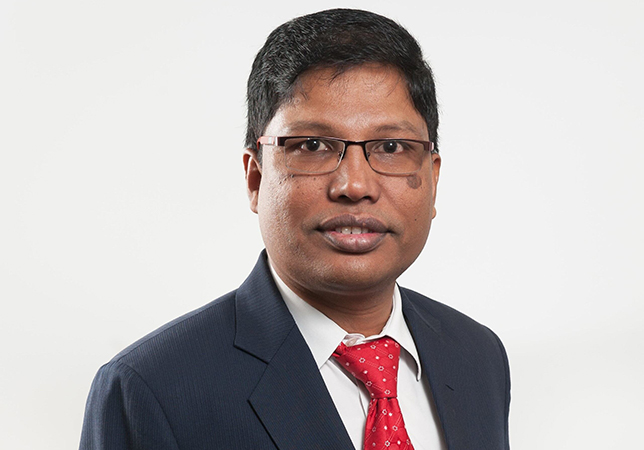
Endress+Hauser’s TempC membrane diaphragm seal provide more accurate performance when measuring lower pressures, without the need to increase the size of the process membrane, writes Sivaji Nemalipuri, Product Manager - Level and Pressure
Pressure measurement is extensively used in the petrochemical and oil and gas industries to measure the process pressure of a vessel, equipment, or pipeline for surveillance purposes.
In more complex scenarios, pressure measurement can be employed to calculate a compensated level measurement in a sealed and pressurised vessel, or to measure the flow by combining with primary elements like orifice plate, Venturi, etc.
![]() |
Pressure transmitters fitted with capillary lines (left) and extension pieces for cooling purposes (centre and right) |
However, application conditions can be often challenging, demanding special precautions to protect pressure transmitters from harsh process conditions.
These harsh process conditions could be high process temperatures, aggressive media, or high vibrations.
The diaphragm seal will be employed to manage such severe conditions, effectively isolating, and protecting the pressure transmitter.
Serving as a secondary line of defence, positioned between the pressure transmitter and the process, a diaphragm seal offers an additional process membrane ahead of an oil-filled, sealed system linked to the sensing membrane of the pressure transmitter.
The addition of this secondary membrane allows for more flexibility in the build specifications to tackle harsh process conditions.
![]() |
A conventional symmetric membrane (top) compared with a TempC asymmetric membrane (bottom) |
For aggressive media, a broader selection of process membrane materials, such as Monel, Tantalum and gold-plated, can be considered to provide a more abrasion-resistant or chemically compatible measuring surface.
For high-temperature applications, an extension piece can be added between the process and sensitive transmitter electronics to ensure that transferred temperatures from the process have sufficiently reduced before impacting the sensor element and associated electronics.
For applications that involve high vibrations, a flexible extension segment, also referred to as a capillary tube or line, can be utilised to mitigate or completely remove any vibration that might be transmitted from the process to the transmitter.
The flexibility of capillary tubes makes them a popular choice for dealing with other installation issues related to pressure measurement.
![]() |
For example, in installations where space is limited, a capillary tube can be beneficial by enabling a smaller physical attachment to the process and allowing the related transmitter to be remotely mounted in a more suitable location.
However, diaphragm seals, in any form, can introduce their own factors into pressure measurement.
For lower pressures, like those in millibar ranges, a bigger process membrane is necessary to ensure appropriate sensitivity and hence accuracy in measurement.
![]() |
This larger membrane often necessitates a bigger process connection, which typically requires the use of mechanical fittings like adaptors for installation.
Not only do these adaptors add to the cost, but they also take up extra space around the fittings and increase the number of potential leak points in the installation, thereby decreasing on-site safety.
Diaphragm seals can encounter problems due to environmental temperatures, particularly those with capillary system designs.
Each capillary system contains a fill fluid that can be affected by the ambient temperature. If the fill fluid becomes sufficiently heated, it can expand and apply pressure on the inner walls of the filled system chamber.
The process and sensing membranes, being the only flexible parts of the chamber walls, naturally flex to accommodate the increased fluid volume. This deflection is interpreted by the sensing membrane as a pressure measurement, which can result in a false reading.
TEMPERATURE COMPENSATORY MEMBRANE
![]() |
TempC diaphragm seals with 3-inch, 2-inch and 1-inch sizes |
Advancements in membrane design aim to tackle issues such as those previously mentioned.
Innovations like Endress+Hauser’s temperature compensatory (TempC) membrane are designed to create a non-axisymmetric deflection mode, resulting in an asymmetric movement in the process membrane.
By increasing the material's thickness and altering the pattern imprinted on the membrane, the behaviour of the process membrane is modified to produce a different response when pressure is applied.
This results in increased sensitivity from the diaphragm seal, providing more accurate performance when measuring lower pressures, without the need to increase the size of the process membrane.
This removes the need for adaptors during transmitter installation, thus reducing potential leak points around the on-site fitment.
The increased flexibility of this type of process membrane also helps correct inaccuracies caused by fill fluid expansion.
![]() |
Gold-plated TempC diaphragm seals for hydrogen services |
As aforementioned, this expansion happens when an external heat source (like sunlight heating the capillary attached to a vessel's top) causes a volume increase in the diaphragm fill fluid, leading to an internal pressure increase that pushes against the sensing membrane, resulting in an error.
By using a more flexible process membrane with improved deformation properties, this increase in fluid volume is physically absorbed, diverting the impact away from the sensing membrane, and thereby reducing any potential error.
![]() |
A cross-sectional view of a pressure transmitter fitted with a diaphragm seal |
The advantages TempC diaphragm seals offer over traditional diaphragm seals include:
• Highest accuracy and process safety.
• Minimised influence of process and ambient temperature fluctuations.
• Smaller dimension process connections with the same or superior accuracy.
• Replace DN80/NPS 3-inch diaphragm seal flange with DN50/NPS 2 inches.
Regardless of their design, diaphragm seals are recognised for their decreased sensitivity to measured pressure and increased sensitivity to external heat sources.
These characteristics should be considered along with the substantial advantages that diaphragm seals provide.
However, with modern advancements from specialists in the instrumentation field and the ensuing technological progress, the effects of these issues can be mitigated. This enhances the reliability and safety of this measurement method, while also lowering installation costs.