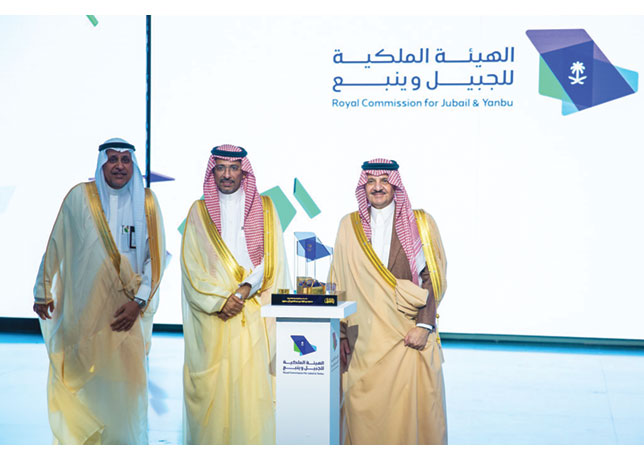
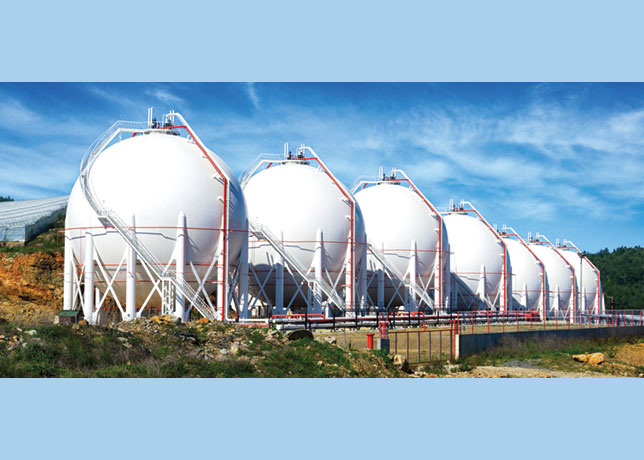
Honeywell has announced a transformational new naphtha to ethane and propane (NEP) process that will enable regions across the world to improve the efficiency of light olefin production and lower CO2 emissions per metric ton of olefin produced.
Ethane and propane are the ideal feedstocks for producing ethylene and propylene – important petrochemicals used in the production of chemicals, plastics and fibers.
This innovation demonstrates Honeywell's alignment of its portfolio with three compelling megatrends, including the energy transition.
The NEP technology generates a tunable amount of ethane and propane from naphtha and/or LPG feedstocks.
In a typical NEP-based olefin production complex, the ethane will be fed to an ethane steam cracking unit and the propane will be fed to a propane dehydrogenation unit.
This approach generates more high-value ethylene and propylene with reduced production of lower-value byproducts compared to a traditional mixed-feed steam cracking unit directly processing the same quantity and composition of feedstock.
This new approach results in net cash margin increases from 15-50 per cent.
An NEP-based olefins complex also reduces CO2 intensity per metric ton of light olefins produced by 5-50 per cent versus a traditional mixed-feed steam cracker.
Honeywell’s latest technology expands our portfolio of offerings to help meet growing demand for efficient petrochemical solutions.
"The petrochemical industry faces strong competition and challenges in obtaining raw materials globally," says Matt Spalding, Vice-President and General Manager of Honeywell Energy and Sustainability Solutions in MENA.
"Our technology helps to enable more efficient production of ethylene and propylene, two chemicals which are in high demand, while also helping our customers lower their carbon emissions."
This new solution is a part of Honeywell’s Integrated Olefin Suite technology portfolio – a first of its kind in the industry that creates differentiated offerings to enhance the production of light olefins.