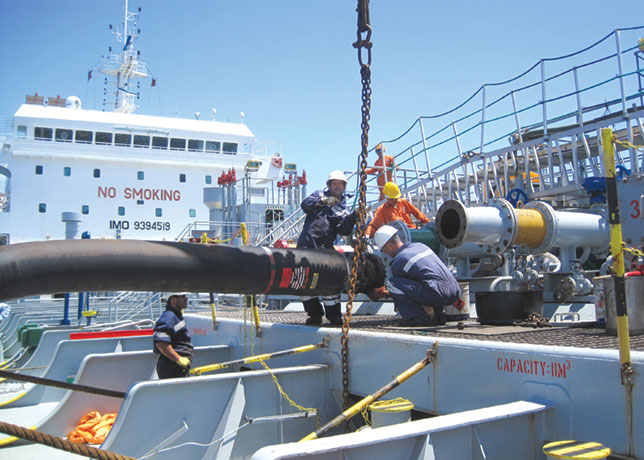
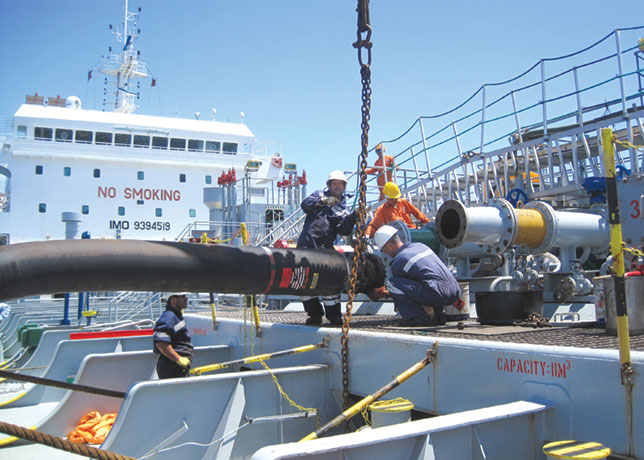
Re-evaluating marine hose selection can realise operational and cost benefits in STS transfer operations, Raphael Poquet from Trelleborg tells OGN
In the ever-evolving backdrop of the changing oil markets and environmental expectations, energy companies and operators are exploring operational efficiencies that are both responsible and dependable for meeting safe, cost-efficient operations.
This is happening in the Middle East, where the growing use of floating production storage and offloading (FPSOs) logistics solutions like ship-to-ship (STS) transfers are integral to flexible, reliable energy supply chains.
STS transfers enable vessels to exchange liquid cargo offshore. This is particularly useful for large vessels, such as very large crude carrier (VLCC) and ultra large crude carrier (ULCC) which could face draft restrictions in some ports.
It also saves the cost of vessels berthing and mooring at jetties, particularly if a ship has multiple unloading points throughout its journey. The process also enables vessels to avoid port congestion.
The use of marine hoses highlights some intricacies within STS transfer processes. Representing a key component of the process between two tankers, the performance of marine hoses in these unconventional and challenging environments can significantly impact the process's safety, speed, and reliability.
Looking more holistically at STS transfer hoses provides an opportunity to re-evaluate thinking around their function.
Safety and reliability are a given, but there can also be untapped potential to reduce operational costs over a hose’s lifetime to maximise overall value.
WALKING THE OPEX & CAPEX TIGHTROPE
STS operations are caught between balancing capital expenditure (capex) and operating expenditure (opex) within energy projects. This can create a familiar balancing act of meeting objectives to minimise upfront costs whilst still managing equipment’s opex over a period of time.
Putting too much of an emphasis on keeping capex down can lead to unpredictable and escalating opex costs over a hose’s total lifetime.
Looking beyond the industry to put this into context, according to McKinsey, maintenance alone can account for 20 to 60 per cent of overall opex, highlighting the importance of product quality and preventative maintenance programs to offset the unexpected costs of corrective maintenance or replacements.
In STS transfer, there can be a perception of hoses being relatively short-term consumables. However, purchasing a hose on the basis that it will last two to three years, rather than up to ten years with the proper maintenance, could eventually overshadow any capex savings.
In fact, it is not just the cost of the hose that should be considered but wider performance factors such as reliability, repair frequency, reduced operational interruptions, service costs, and procedural disruptions.
Ultimately, taking a different view on the cost of ownership could outweigh the initial upfront cost savings at the point of purchase.
We have seen mounting recognition of this as companies re-examine STS transfer hoses more broadly.
Today, owners and operators are increasingly benefitting from the operational reliability and efficiency of high-performance marine hoses in STS operations, as well as further strengthening their environmental credentials.
For example, as the sustainability of energy supply chains is being scrutinised, advanced hose technologies can help operators meet increasingly stringent environmental regulations, such as MARPOL and contribute towards the UN Sustainable Development Goal 14.
Replacing hoses less frequently also reduces the associated environmental impact of waste disposal and recycling.
DIFFERENT HOSES PROVIDE DIFFERENT RESULTS
Choosing the right STS transfer hose can unlock opportunities to optimise performance and reduce costs throughout the asset’s lifecycle.
Hoses that are selected with proven reliability can significantly lower operating expenditures and enhance operational viability without compromising safety.
These STS transfer marine hoses are put under pressure in operations, unlike other applications using marine hoses with different configurations.
For STS transfers, various types of products can be transferred throughout the life of a hose. These include sweet crude and more aggressive fluids like biodiesel (FAME) or Methyl tert-butyl ether (MTBE).
As a result, the quality of the rubber liner is a priority for these hoses. At Trelleborg, we formulated our rubber compound in-house to ensure that we can test and develop outstanding chemical resistance for STS transfer applications.
The KLEINE STS hose incorporates this formulation into its unique design. Additionally, the nippleless design with the continuous inner liner prevents fluid exposure.
This includes the connector or bonding agent between the connector and the liner. Therefore, avoiding the risk of liner delamination from chemical exposure.
Meanwhile, frequent and variable handling, including derrick and deck storage, means STS hoses endure wear beyond their primary function of containing product flow.
Loaded hoses on vessel rails require robust external construction due to the weight, while unloaded hoses face different stresses due to the absence of internal pressure.
In response to these challenges, KLELINE STS's dual carcass technology incorporates two independent steel cable layers within a compact flange, allowing continuous, homogeneous curvature despite the short distance between vessels.
Each carcass addresses different functions: internal pressure resistance and external load management, ensuring fluid containment is always guaranteed, even under severe damage.
Then there is the importance of meeting standards, such as the GMPHOM 2009, EN 1765:2016 / L15 and OCIMF, which is essential for hose suitability.
However, when considering the standards, one should remember that these are the minimum requirements, and exceeding them can offer distinct commercial benefits in the long run.
The Trelleborg KLELINE STS offers improved performance than required by EN 1765 with a +25 per cent higher safety factor on burst pressure and +60 per cent higher adhesion between layers compared to some alternative hoses, improving resistance to the impact of demanding STS operations to protect its longevity.
Recently, we also introduced another instrument to help with intelligent hose management. The KLELINE STS app is able to provide detailed data on each KLELINE STS hose.
The app enables comprehensive hose management and performance monitoring, supporting an optimised cost strategy in the flexible logistical environment typical of STS operations.
This highlights how digitalisation can enhance physical processes within STS operations. By providing operators with real-time data on hose performance, wear, and maintenance schedules, it can enhance operational efficiency while extending the lifespan of hoses.
The results mean that operators can pre-emptively address potential issues and maintain uninterrupted service.
Effective preventative maintenance depends on accurate, valuable information, including hose history and performance, to achieve the longest and most reliable service life.
These attributes combine to position KLELINE STS as a robust choice for STS operations, particularly due to its ability to deliver predictable maintenance costs for the lifecycle of the hose.
SUPPLIER’S RESPONSIBILITY
From a supplier’s perspective, we must continuously work to develop proven solutions that safely extend hose life and deliver operational and cost efficiencies.
This commitment should involve collaborating between supplier and customer; to share maintenance schedules supported by performance insights.
Openly sharing information and advice can help customers achieve increasingly improved operational performance and unlock cost efficiencies.
Today, STS hoses are playing an important role in an increasingly agile energy infrastructure. In combination with talented personnel, there is a tangible opportunity to work together to significantly enhance the performance of STS operations.
Doing so, can improve competitiveness, reduce environmental impact and increase profitability.