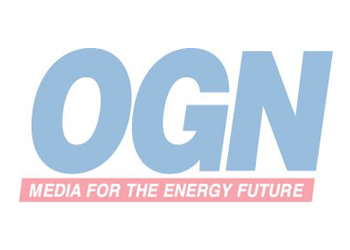

Saudi Aramco has reaffirmed its unique and internationally renowned capability to construct and operate mega projects by bringing the expanded Qatif Producing Plants Project on line to produce hundreds of millions of additional barrels of crude annually.
As with previous award-winning mega projects such as Shaybah, Hawiyah and Haradh, the company delivered on the Qatif project ahead of schedule and under budget, along with setting new industry standards for design, efficiency, safety and innovation.
As with previous award-winning mega projects such as Shaybah, Hawiyah and Haradh, Saudi Aramco delivered on the Qatif project ahead of schedule and under budget, along with setting new industry standards for design, efficiency, safety and innovation.
The Qatif project, the largest crude increment built in recent times, adds 650,000 barrels per day (bpd) to the 150,000 bpd already produced from the Abu Sa'fah field.
At 800,000 bpd, Qatif becomes the world's largest crude production facility. In addition, it produces 370 million standard cubic feet per day (scfd) of associated gas and 40,000 bpd of high-value condensate.
This massive project was commissioned and started production in August, three months ahead of schedule.
The project, which took three million man-hours to design and 70 million man-hours to construct, brought with it the latest technological advancements to increase operational efficiency as well as environmental safety, from an onshore smokeless flare system to a new, 99 per cent-effective sulfur-recovery system at Berri Gas Plant that uses new technology to make it the cleanest operating plant of all Saudi Aramco facilities.
At the peak of construction, more than 15,000 labourers, craftsmen and professionals of various nationalities worked on the project at different work sites, in and out of the kingdom.
'Detailed engineering was completed in 21 months, which is a remarkable achievement for a program of this size,' Zaid M Al-Hazmi, manager of the Ras Tanura Producing Department, told members of Saudi Aramco's Board of Directors. 'To expedite the procurement of long-lead materials, purchasing activities were started early during the engineering cycle. Construction was completed by July 2004 - a record time for a project of this magnitude.'
In describing the three phases of the project - engineering and procurement, construction, and commissioning and startup - Al-Hazmi explained that the team always looked ahead to the phases and activities that would follow. 'Throughout the programme, there was seamless integration between team members working on the different phases, ' he said.
'The team members were empowered to make decisions, and communicate the information to teams working in parallel on the other phases of the programme. Close interaction between team members resolved many design, construction and commissioning issues promptly and effectively.'
The expanded Qatif Producing Plants Project was commissioned and in production three months ahead of schedule.
And that foresight extended from construction to operation. Nearly two years in advance of startup, commissioning team members were assembled and sent to other Saudi Aramco plants and to the vendors who were manufacturing equipment for the project.
'The team recognised early in the programme that training on the new systems would be essential for a safe and early plant startup,' Al-Hazmi said.
'This early training allowed team members to do their jobs more effectively, and commissioning was completed ahead of schedule,' he said. 'Innovation applied to all parts of the project, and the close interaction of all parties involved led to new ideas that saved both time and money.'
Al-Hazmi also said the company is proud that this major milestone 'was achieved by a competent Saudi Aramco workforce. The programme development, project management and commissioning team were more than 98 percent Saudi nationals.'
From the beginning, Saudi Aramco was determined to build on its world-class mega project experience with the Qatif and Abu Sa'fah Projects. That was the theme for every phase of the programme.
'One of the most important features of the project was developing new construction methods, which helped us a lot,' said Maurizio D'Ambrosio, project engineering manager of Snamprogetti.
'For instance, instead of excavating single foundations for the main pipe rack, we excavated a long trench. It may have been more work, but it allowed construction to proceed at a faster pace. We precasted the foundation slabs one by one and then put them in place with a large crane. This saved almost two months; we were already ahead of schedule.' Such activities put the team ahead of the game.'
Although time was of the essence, the commitment to design and build best-in-class facilities was always put first.