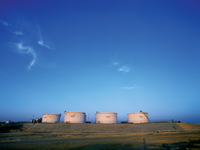
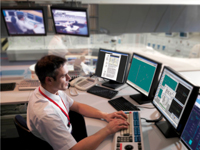
HONEYWELL has provided dynamic modelling and operator training for Petroleum Development Oman (PDO) using its UniSim design.
PDO’s Lekhwair Production Station (LPS) in the North-East of Oman is about 110 km from the the Yibal Government Gas Plant and its associated network. In 2011 the plant was upgraded with new (double train) sour gas treatment facility.
At the same time, the Lekhwair team committed to a project to develop a dynamic simulation model of LPS to help with troubleshooting and process optimisation.
The project would cover all new facilities as well as existing units, and included in this, plan was an operator training station (OTS) to help staff prepare for an upgrade of the Distributed Control System (DCS) from Honeywell DT3000 to Experion during 2013, and boost operators’ efficiency and proficiency.
PDO chose Honeywell to deliver all aspects of the project, using the UniSim Design Suite of process modelling tools, says a Honeywell case study.
The dynamic simulation model and OTS developed by Honeywell have brought significant benefits in the operational and control strategy, verification of logics for new units, and operator competence. Unanticipated benefits include the identification of loop holes in upgraded logics for sour gas conditioning and pinpointing an incorrectly calibrated flow transmitter. Honeywell’s suggestions for improvements to the upgraded DCS logic have also been implemented in the actual plant.
In particular, the dynamic mode has been used for a vital process safety study of brittle fracture of metallic materials across LPS, as well as continual troubleshooting and optimisation. Its findings have been widely disseminated among other PDO teams.
Similarly, the OTS that has been used to boost confidence of central control room operators is also being shared with other PDO sites.
![]() |
The Suite offers mutifarious applications |
Finally, a steady-state model of LPS, which proved vital to deliver the project, has also proved valuable. It enabled a new Enhanced Oil Recovery (EOR) study and has been used for annual updates of winter and summer case heat and mass balance (H&MB) documents. This has ensured accurate process data for all other LPS studies and projects. Again, this has benefited other PDO teams as well.
Yerbol Seifullin, PDO process engineer, says: “We’re now able to simulate operating scenarios and optimizing processes, as well as improve the team’s competences, especially among younger members of the operating team.
“More fundamentally, it is helping us move from a reactive approach to operating the facility to proactive operation using different monitoring and modeling tools. Unisim Design is the perfect tool for that.”
“Unisim is helping us move from a reactive approach in the facility to proactive operation using monitoring and modeling tools. It’s the perfect solution for that.”
The initial challenge faced by any project of this type is to get buy-in from the management. To do so, it was necessary to show the training solution would also address the process engineering needs and demonstrate a solid return on investment.
A significant complication soon emerged, however: although utilities were not part of scope of the process model, these were discovered to be essential to the OTS scope to train operators on those units’ controls. That meant the hot oil system, fuel gas and flare systems, for example, also needed to be modelled.
With no reliable H&MB, the project was expanded to include building a steady state model based on running plant data. An additional 70 instructor graphics to match the plant’s Experion PKS graphics were also added to the scope.
The processes requiring modelling for an effective dynamic model and training station were wide ranging:
• Bulk separators, six of which separate the crude gas and oil from the wells into gas and water-oil phases;
• Gas lift compressors – Five trains compress the gas from the bulk separators;
• A gas sweetening unit (GSU) that treats this gas with amine to remove the H2S and CO2;
• Sweet and sour gas conditioning units to dry gas from moisture;
• Dehydration tanks and oil export pumps; and
• Skim tank and water injection pumps.
Since PDO was already a user of Unisim Design (USD), it was natural to employ the solution for the dynamic simulation model for the process and concept engineers, and this engineering model is also the heart of the training station.
The dynamic model underlies the OTS, which uses Honeywell’s Unisim Operations process training programme: The plant’s Experion DCS screens run on top of USD model so trainees face an interface that looks identical to and responds in the same way as that of the central control room.
An instructor station and OTS model server are connected to the PDO corporate network, enabling any number of trainees to connect using standard PCs.
Despite the additions to the scope of the project, the solution was delivered in a tight timeframe. Gathering the process data required for modelling began in August 2011. By the end of December, a steady state model had been built to provide the reliable H&MB required for dynamic modeling.
In total it was just nine months from the initial meeting with the project team to site acceptance testing at Lekhwair in June 2012.
Since then, Honeywell has held an additional training session at the site, and use of the OTS continues to evolve; a new training programme in March 2013 to optimise start-up of station after major shutdown, for example, is expected to improve start-up times by 2-3 hours.
Longer term, PDO is working on implementing a corporate-wide training solution. It is hoped the OTS in Lekhwair will come to represent just the first, very successful step.