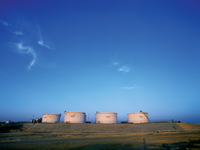
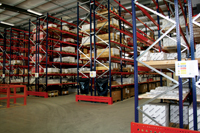
HI-FORCE, the UK-based manufacturer of high pressure hydraulic tools, has taken the delivery of a new multi-million pound purpose-built facility, located at the rear of its existing UK manufacturing plant.
The new facility comprising almost 20,000 sq ft of built-up area, plus a 15,000 sq ft secure yard area, houses the company’s complete UK logistical operation from raw materials through to finished product. In addition, the facility also accommodates a 1,500 sq ft ECITB (Engineering Construction Industry Training Board) approved training school.
The new building is virtually self-sufficient in terms of electricity requirements thanks to its integral solar paneling within the roof area. Any unused electricity generated by the solar panels is pushed back into the national grid.
Since handover of the building, Hi-Force UK logistics manager Dave Summerfield has been busy organising relocation of all stock and raw materials from the existing facility to the new expanded logistics centre. Summerfield comments: “Moving over £5 million ($7.4 million) of raw materials, components and finished goods to a new facility, whilst still satisfying our global customers’ product and spare parts needs has not been an easy job! With over 1,800 different product lines, over 10,000 different component parts, plus raw materials and packaging, the job of relocating them to specific new warehouse locations and monitoring these changed locations through the company ERP system, has certainly not been without its challenges. Thankfully the new facility has more than quadrupled the available space and racking capacity that we previously had, so at least we had plenty of lay down space during the move. The relocation of the stock has taken best part of a month to complete, but the extra investment made in materials handling equipment, personnel and storage capacity has already starting to reap dividends in terms of time savings and improved efficiency.”
Alongside the relocation of the logistics centre, business development manager Pat Wright and training manager Steve Wakelin have been busy equipping the new purpose built Training School, which comprises of a fully equipped classroom, product practical training and demonstration area and product service and repair facility. Hi-Force has already been approved by the ECITB to carry out Mechanical Joint Integrity Training as per ECITB training standards MJI10, MJI18 and MJI19. Plans are also already in place to expand the Hi-Force ECITB approved training courses to other product and application areas. Commenting on the Training School, Wright advises: “We believe that this new training facility is amongst the best available in the industry and delegates attending the training not only have the opportunity to be trained to the highest, independently approved, level available, they also get the opportunity to view firsthand the entire Hi-Force manufacturing process, from raw materials to finished product all on one site.”
Construction and equipping of the training school has cost in excess of £200,000 ($297,000), which has ensured that everything necessary to deliver training of the highest quality is exclusively available as part of the training school tooling and equipment. Training manager, Steve Wakelin comments: “Having the new training school located in the logistics centre means that trainers and delegates can be entirely focused on the training, without the distractions we previously faced in the earlier much smaller training room located close by to the production area. We have already had tremendous interest in our new ECITB approved training programmes and of course our standard product sales, service and repair training courses will be even better in this much improved new facility.”
Commenting on the expansion, group managing director, Kevin Brown adds: “Whilst the primary need for a new logistics centre was required for us to better handle our ever increasing volume and range of products and components, what this expansion has done is freed up a further 7,000 sq ft in the main building, for further expansion of our manufacturing and assembly facilities. Now that the stock has been moved, we can use up the space available to house additional manufacturing capability. We received and commissioned another Mori Seiki 4 axis CNC machine at the end of May, bringing our total fleet of machines up to 11.”
Feasibility studies have already started for ordering machine number 12, a long bed 3-axis machine for manufacturing high tonnage and long stroke cylinders, for which the group board has already approved a budget of over £600,000 to purchase later in the year, he says.
“We have also completed the relocation of our Quality Control Department to a new much larger, self contained area, including the purchase of additional state-of-the-art measuring equipment. Next on the agenda is to relocate the assembly shop to the area previously used for storage and to build a fully equipped, test cell for finished products, close by the finishing and packing area.
“As a growing company it is vitally important that we ensure our facilities cope with growth without compromising on quality, delivery and price,” he adds.