
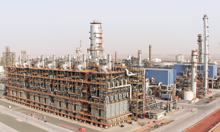
BOROUGE is a leading provider of innovative, value creating plastics solutions. A joint venture between the Abu Dhabi National Oil Company (Adnoc), one of the world’s major oil and gas companies, and Austria-based Borealis, a leading provider of chemical and innovative plastics solutions, Borouge is a groundbreaking international partnership at the forefront of the next generation of plastics innovation.
Borouge has its headquarters in the UAE and Singapore, employs approximately 3,000 people representing more than 40 nationalities and serves customers in more than 50 countries across the Middle East, Asia-Pacific, Indian subcontinent and Africa.
Building on Borealis’ unique Borstar technology and experience in polyolefins for more than 50 years, Borouge provides innovative, value creating plastics solutions for the infrastructure (pipe systems, and power and communication cables), automotive and advanced packaging markets.
In 2010, Borouge tripled the annual production capacity of its plant in Abu Dhabi to 2 million tonnes, and with further expansion to 4.5 million tonnes in 2014, Borouge and Borealis will have a combined annual production capacity of approximately 8 million tonnes of polyethylene and polypropylene. With this expansion, Borouge will create the world’s largest integrated polyolefins plant.
The two companies continue to invest to ensure that their customers throughout the value chain, around the world, can always rely on superior products and security of supply.
BENEFITS
The project involved an upgrade from old Logic Manager System to FSC Blue system. The upgrade solved the issue of Logic Manager obsolescence and support at the Borouge PE1 plant. The newly installed FSC Blue system will increase plant safety. FSC is a proven safety system for more than 20 years for different oil and gas customers all over the world.
Honeywell and Borouge enjoy a good working relationship built over years of working together on multiple projects at the site.
Borouge engineers are therefore well-acquainted with all aspects of Honeywell’s systems from operation to maintenance. This simplified the training process because the FSC Blue System IO modules are the same as the existing SM systems installed for Borouge 2. Inventory management is also therefore simplified.
FSC Blue is also compatible with the existing Honeywell TPS system installed at the Borouge PE1 plant.
CHALLENGE
The main challenge was that the existing Logic Managers were obsolete. Spares were difficult to obtain, and there were very few skilled resources available to support these products.
An additional challenge was the tight schedule, with only a small and fixed shutdown window available, during which the Logic Managers could be replaced with the FSC Blue system.
It helped that the customer had confidence in Honeywell’s expertise and experience to perform the upgrade in the limited shutdown window.
Logic Manager upgrade at Abu Dhabi Polymers Borouge Polyethylene Plant 2.
SOLUTION
The Honeywell solution installed at the Borouge PE1 plant comprised the following elements:
• Three redundant FSC Blue systems with non-redundant FSC Blue I/O’s and two system extension cabinets;
• Engineering and configuration;
• Conversion of Logic Manager Ladder logic to Functional Logic Diagrams in the FSC Blue system;
• Modification of related graphics and reports;
• Factory acceptance test;
• Supervision of site installation activities; and
• Commissioning and site acceptance test
Honeywell managed the whole project successfully, arranging for all necessary materials for system staging in a very short timeframe, and implementing reverse engineering of Logic Manager logic to build FSC logic. The decommissioned Logic Manager modules are being maintained at Borouge as spares for the remaining Logic Managers at this site.
The Honeywell team also conducted extensive logic testing during Factory Acceptance Testing with the Borouge operations and maintenance team, and connected prefabricated cables from field terminal assemblies to terminal blocks.
Key to the success of the project was the detailed site schedule plan, which ensured a smooth upgrade of the system within the fixed shutdown window. The Honeywell and Borouge project teams worked very closely and smoothly together and equally contributed to the success of this project.