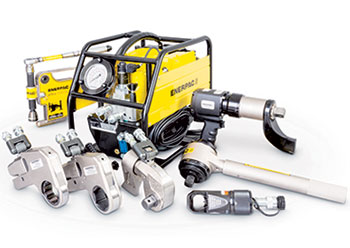
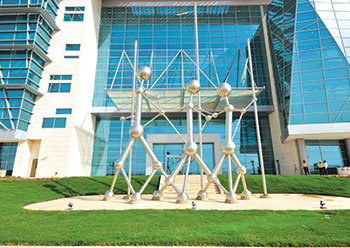
Additive manufacturing’s ability to accelerate the design and prototyping process, without the expense of tooling, is one of its key benefits
Sabic showcased capabilities in additive manufacturing, glazing and carriage interiors that can help rail carriage engineers and interior designers and their suppliers expand engineering and design horizons while helping to reduce weight and maintenance, as well as capitalise on new production processes at the American Public Transportation Association (APTA) Expo 2017 from October 9 to 11, 2017.
The potential end benefits can make a significant difference to members of the rail industry’s value chain in terms of greater efficiencies in energy use and overall system costs.
Additive manufacturing’s ability to accelerate the design and prototyping process, without the expense of tooling, is one of its key benefits, as is the potential for part consolidation and the development of commercial components.
Sabic, long recognised as a global leader in thermoplastic technology, has heightened its focus on advancing additive manufacturing from prototyping to full-scale production. In May 2017, Sabic had launched six filaments for fused deposition modeling and a new family of reinforced compounds for large format additive manufacturing to help customers capitalise on the potential of additive manufacturing as a production process.
As an example of the capabilities of additive manufacturing for rail, Sabic’s booth featured a bracket created using Ultem AM9085F filament, designed for use with Stratasys Fortus printers.
The bracket, typically made from sheet metal, is used in rail carriage hidden spaces to mount ceiling components. Ultem AM9085F filament is made from Sabic’s Ultem resin, offering the same composition as the company’s injection molding grades. This polyetherimide (PEI) material is desirable for applications that require high heat resistance, high strength and low flame, smoke and toxicity.
"The bracket is one small example of the way Sabic is eager to partner with the rail industry to help customers make the leap from prototyping to full-scale additive manufacturing production," said Lori Louthan, director, Mass Transportation, Sabic.
"We’re enabling this evolution by creating a range of high-performance additive manufacturing materials – even industry-specific grades to meet regulatory requirements – and are supporting customers with our extensive expertise and resources for testing, design and application development."
Also on display was a passenger rail car side window component constructed by Total Plastics, Intl from Sabic’s Lexan FRA 25C sheet.
The dual-pane side window consists of two .25 inch panes, CNC routed and assembled with a gasket spacer. Lexan FRA 25C sheet is a coated, flame retardant polycarbonate sheet that passes ASTM E162 for flame spread; ASTM E662 for optical smoke density and ASTM E1354 for heat release.
The sheet offers high impact resistance, with up to 70 times the impact resistance of laminated glass. The sheet has been developed for rail glazing applications.
Railway coach manufacturers now have a new material to inspire a fresh approach to design and coach aesthetics while addressing key safety regulations, thanks to an innovative polycarbonate sheet solution from Sabic being introduced today. Visitors to Sabic’s booth watched new Lexan DH65011 sheet’s versatility in a seat back shell manufactured by Khrome Product Transport.
Lexan DH65011 sheet is a thermoformable opaque, solid, low-gloss polycarbonate/acrylonitrile-butadiene-styrene (PC/ABS) material that can be used for interior walls, ceiling components and for back and base shells of passenger seats. Lexan DH65011 sheet is also compliant with the US Federal Railroad Administration (FRA) fire safety standard for passenger rail car interior walls, ceilings and seat frames, NFPA 130.
This new high-performance material solution is well-positioned to help railway interior designers and manufacturers create attractive components via the nearly unlimited decorative customisation options that the new Lexan DH65011 sheet provides. Overall fuel efficiency of mass transit systems can also be improved, as this lightweight material can help manufacturers to reduce the weight of railway interiors.