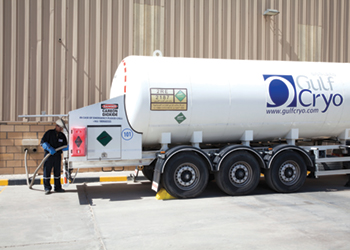
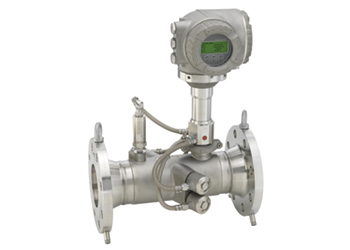
Whether natural or processed gas, or gas mixtures, the robust ultrasonic gas flowmeter with integrated pressure and temperature sensors offers highly accurate, real-time measured values
Tremendous gas reserves are still being discovered and tapped into owing to state-of-the-art drilling technology. It is expected that the demand for natural gas as a fuel or energy source will continue to increase in the future. This requires systems that can offer accurate and reliable measurement.
Whether natural or processed gas, or gas mixtures, either in the offshore or onshore sector: the new Prosonic Flow G from Endress+Hauser is the ideal flowmeter for demanding applications.
This flowmeter combines tried-and-tested ultrasonic flow measuring technology with decades of experience in the oil and gas as well as chemical industries. The Prosonic Flow G measures both dry and wet gases with high reliability. It ensures precise measured values (±0.5 per cent) with unmatched repeatability, even when process and ambient conditions fluctuate significantly.
Together with the extensive functionality of the Proline 300/500 transmitters, this opens up new options for process control and monitoring.
![]() |
Prosonic Flow G 500 ... remote version, DN 100/4 inch for harsh applications |
The robust industrial design makes it possible to operate the device over a long term without requiring maintenance, thus saving time and money for the user.
The Prosonic Flow G operates at process temperatures of up to 150 deg C (302 deg F) and pressures up to 100 bar (1,450 psi). It can also be ordered with built-in temperature and pressure sensors.
The input from these sensors can be combined with the measured sound velocity to calculate a great number of additional gas properties that are important for process control.
• Comprehensive process monitoring: The Prosonic Flow G 300/500 can be supplied with an ‘Advanced Gas Analysis’ function package for special applications or for increased process control requirements.
Depending on the selected gas type (pure gases, gas mixtures, coal gas, natural gas, customer-specific gases, etc), this function enables the calculation of additional parameters and process variables. Some examples include volume flow, corrected volume flow, mass flow, energy flow, calorific value, Wobbe index, molar mass, methane content, density or viscosity.
![]() |
Prosonic Flow G 300 ... compact version, DN 300/12 inch for petrochemical applications |
• Robust and industry-optimised: The Prosonic Flow G 300/500 stands out for its high degree of robustness. All wetted parts are made of stainless steel and titanium Grade 2 and are compliant with the stringent requirements of NACE MR0175/MR0103. As a result, the measuring system features high corrosion resistance and is ideally suited for applications in the oil and gas and chemical industries.
Since the entire sensor housing surface consists of corrosion-resistant stainless steel as well, Prosonic Flow G is especially suited for harsh ambient conditions.
The Prosonic Flow G also features maximum robustness when measuring moist or wet gases. The innovative sensor concept is equipped with a special drainage system that immediately dissipates any condensate that forms in the sensor pocket area. The ultrasonic measurement, therefore, remains unimpeded, that is, without any negative effects on the signal quality.
• Process reliability around the clock: Since the Prosonic Flow G measuring system has been developed in accordance with IEC 61508 (SIL), it can also be used in safety-related applications.
Additional security is provided thanks to a permanently installed rupture disk for controlled release of overpressure in the event of potential leakage. Any device or process errors that may occur are clearly categorised and indicated in accordance with Namur NE107. This makes it possible to take fast and targeted corrective actions.
• Heartbeat technology: Heartbeat Technology is another highlight. This testing function is integrated into all Proline measuring devices and enables permanent self-diagnostics with the highest diagnostic coverage (over 95 per cent) as well as a TÜV-certified, metrologically traceable device verification without process interruption. All of this reduces complexity and hazards in a plant and increases its reliability as well as availability.
• Direct access in the field: Proline 300/500 transmitters include a web server as standard. Using a standard Ethernet cable and a laptop – or wireless via WLAN – users have direct access to all diagnostic, configuration and device data without additional software or hardware. This enables targeted and time-saving maintenance and service.
• HistoROM: This one-of-a-kind data storage concept ensures maximum data security before, during and after service. All calibration data and device parameters are stored securely on the HistoROM data storage module and are automatically reloaded after maintenance work. Installing spare parts is easy, saves time and thus reduces unnecessary downtimes.
• Transmitters for seamless system integration: The Prosonic Flow G can be combined with two different transmitters: as a compact version (Proline 300) or as a remote version (Proline 500) with up to four inputs and outputs.
Proline transmitters make no compromise in terms of performance and accuracy. The digital signal processing begins in the intelligent sensor and is the basis for a real multivariable measurement. This means that the Prosonic Flow G can simultaneously detect multiple measured values that are important for process control, for example, flow velocity, sound velocity, pressure, and temperature, and forward these values to a process control system. Full access to all measurement data, including diagnostic data acquired by Heartbeat Technology, is possible at any time thanks to digital data transmission via HART or Modbus RS485, as well as via WLAN or the freely combinable inputs and outputs.