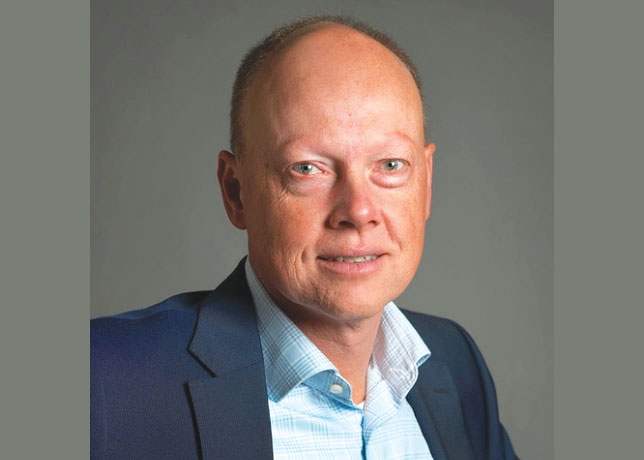
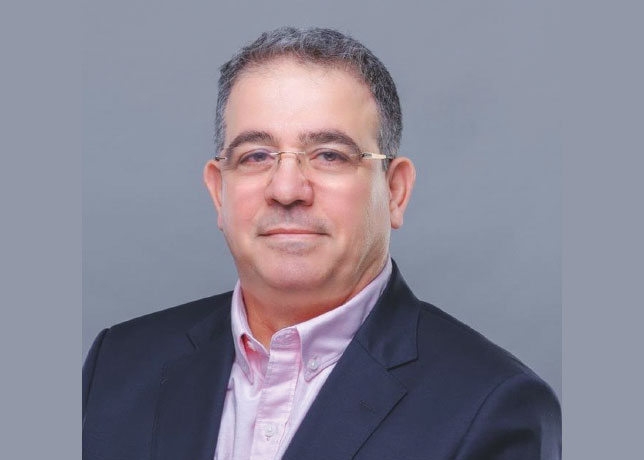
Sulzer Chemtech leads in mass transfer solutions to reduce CO2 emissions, improve energy efficiency, and drive innovation in sustainable energy solutions across various industrial sectors, Dr Rafic Traboulssi tells OGN
Sulzer Chemtech’s mass transfer and process technologies are used in various carbon capture (CC) and energy efficiency process solutions to help the industry reduce CO2 emissions.
The company, a division of Sulzer a Swiss technology corporate based in Switzerland, is a world leader in the design and supply of mass transfer technologies for separation processes such as distillation and absorption.
"These processes are at the heart of industrial plants across oil and gas processing, oil refining, manufacturing of petrochemicals, chemicals, specialty chemicals, and pharmaceuticals," Dr Rafic Traboulssi, Director – Strategic Business Development, Sulzer Chemtech Middle, tells OGN energy magazine.
In 2019 Sulzer acquired GTC Technologies, a process technology licensor, to extend its capabilities to support customers with licensed technologies targeted at aromatics extraction, process intensification, such as Dividing Wall Distillation Columns (DWCs), and technology for pushing thermal efficiency of fired heaters to above 95 per cent, as well as process technologies for manufacturing renewable fuels such as sustainable aviation fuel (SAF) and renewable diesel (RD).
With industrial countries committing to net-zero carbon policies, carbon capture has gained increased attention.
![]() |
Sulzer's MellapakTM CC |
Several process technology solutions have been developed that are specialised in different applications depending on the source of the CO2 stream (for example, pre/post combustion) or low/high CO2 concentrations.
These process solutions utilise technologies like are absorption (solvent-based process), adsorption, membrane technologies, mineralisation, and others.
The captured CO2, as a source of carbon, has the potential to be used as a raw material in the manufacturing of fuels, carbonates, polymers, fertilisers, and chemicals, or as a recovery agent in techniques such as enhanced oil recovery or enhanced coal bed methane recovery (ECBM), depleted oil gas fields, and deep saline aquifers.
Sulzer Chemtech offers several technologies for carbon capture.
• Sulzer MellapakTM CC: The main challenge in removing CO2 from large volume flue gas streams with CO2 concentration of typically 3.5 – 14 vol per cent - such as for in post-combustion flue gas - using solvent-based approaches is the requirement for large absorber columns.
Hence, this renders the specific pressure drop an important cost factor specifically for the operation of such absorption columns.
Structured packing offers an excellent solution in terms of both reducing the column’s dimensions (capex) and providing a low pressure drop (opex) over the absorber.
The correct choice of gas and liquid distributors is also critical in the economic operation in such large-scale industrial applications.
With deep understanding of the fundamentals of mass transfer and reaction kinetics in CO2 chemisorption, Sulzer has developed the Mellapak™ CC structured packing family to address various challenges in a broach range of carbon capture applications, including post-combustion flue gas at atmospheric pressure and process streams at high pressures.
MellapakTM CC, which is specifically suited for carbon capture using solvent-based absorption processes offers optimum mass transfer performance at the lowest possible specific pressure drop.
It reduces pressure drop by up to 60 per cent compared with conventional structured packings used in post-combustion CO2 capture.
In high pressure applications like fertiliser plants, MellapakTM CC offers significant improvement in both efficiency and capacity compared to commonly used random packings which yield up to 20 per cent reduction in energy consumption.
Due to its technical benefits MellapakTM CC is now the industry-leading choice for CO2 absorber columns proven in some of the largest carbon capture projects in the world, and most recently in the GCC region.
• Dividing Wall Column (DWC) distillation technology: This technology enables more energy efficient solution by integrating two or more distillation columns into one and thus lead to reduced energy consumption but also lower equipment costs as well as to a lowered plant footprint, ultimately leading to lower conversion costs whilst improving the carbon footprint of a process.
Sulzer offers licensed DWC technology for various processes including naphtha splitters, Food Grade Hexane (FGH) production, and LPG recovery.
For instance, the GT-LPG Max™ column is a top dividing wall column which enables achieving 99 per cent propane recovery without the use of external refrigeration.
• Heater 95+ Technology: Sulzer Heater 95+ technology offers further opportunities towards decarbonisation of industrial plants by improving fired heater thermal efficiency to above 95 per cent.
The patented process solution not only reduces CO2 abut also, SOx, and NOx emissions can be applied in grassroots plant but also be implemented as revamp in existing plants.
In traditional fired heaters, the heat efficiency is limited due to the sulfuric acid’s dew point and related corrosion and fouling.
As a result, the maximum efficiency is capped at 89-92 per cent even with various materials of APH.
Typically, in oil refineries, fired heaters are designed to operate at above 150 deg C flue gas temperature. In practice, those units often operate at 180–200 deg C, which results in thermal efficiencies of only 89–92 per cent.
Sulzer’s 95+ Fired Heater technology enables operating the fired heater at a much lower temperatures, as low as 100 deg C, and thus enhances the thermal efficiency to above 95 per cent by eliminating the sulfur-induce corrosion problems in traditional heaters.
Some of the applications include reforming heaters, CDU/VDU heaters, cylene column heaters, coker heaters, hydrotreating heaters, and some chemical heaters.
• Renewable process technologies: Sulzer is at the forefront of innovation in process technologies for renewable feedstocks. From oleo-chemicals to biofuels (SAF and RD), bio-chemicals, and biopolymers, the company is committed to sustainable solutions.
Sulzer continues driving advancements in plastic recycling and battery materials for a low-carbon future.
Our offering covers fully customisable separation technologies, mass transfer solutions, and polymerisation expertise for businesses keen on developing or producing sustainable materials.
• VoltaSplitTM Technology: VoltaSplitTM is the latest technology announcement by Sulzer for electrified distillation. VoltaSplitTM exemplifies Sulzer’s dedication to innovation.
This technology marks a major advancement in Sulzer’s efforts to reduce the energy consumption and CO2 emissions from industrial plants, particularly distillation plants.
Traditionally the steam to heat distillation units Is generated using fossil fuels. With VoltaSplitTM, the energy consumption can be reduced significantly by introducing heat pump technology using electricity as energy source.
VoltaSplitTM uses vapour recompression to achieve this remarkable efficiency. By recompressing distillation column overhead vapours, the stream can be used as heating medium in the column’s reboiler.
This almost eliminates the need for cooling water for and heat as utilities. These savings lead often lead to payback periods of less than two years for the implementation of the technology, all while saving significantly reducing CO2 emissions.
VoltaSplitTM is versatile and thus can be adapted to a wide range of industrial processes. For applications where direct vapour recompression is not feasible, VoltaSplitTM can be adapted using indirect vapour recompression (heat-pump systems).
This flexibility ensures that VoltaSplitTM can meet the specific needs of various industries, including chemicals, biofuels, and pharmaceuticals.
The control system for the compressor and distillation column can be optimised to maximise efficiency and ensure stable operations.
This fine-tuning enhances the performance of distillation units, allowing them to deliver reliable and consistent results across different process conditions.