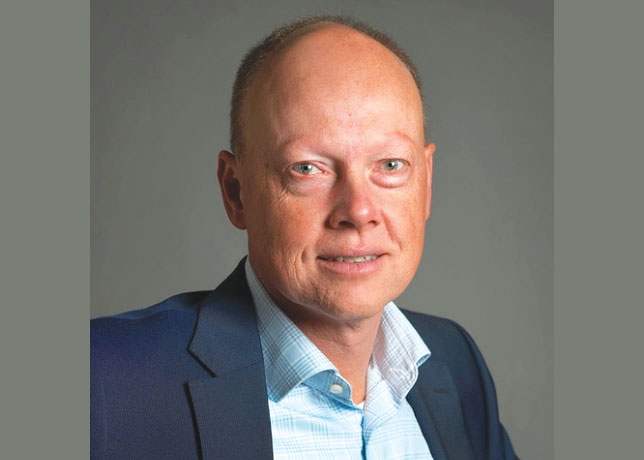
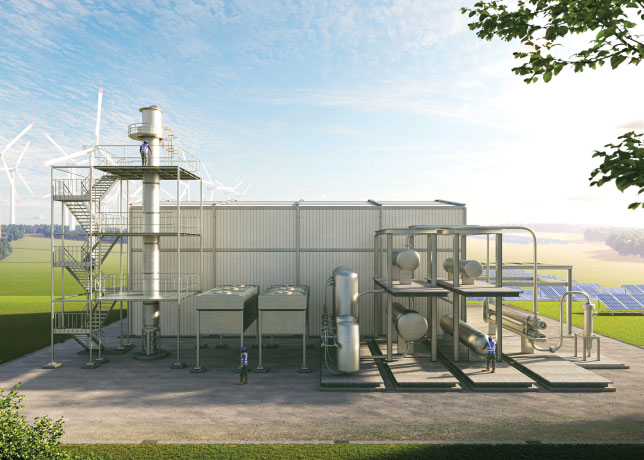
Stamicarbon is developing new technologies to address global food demand by enhancing agricultural productivity and reducing environmental impact, focusing on fossil-free feedstock alternatives in the nitrogen fertiliser industry, Deepak Shetty tells OGN
The production of nitrogen fertilisers with a lower carbon footprint is high on the agenda due to the global efforts to reduce greenhouse gas (GHG) emissions and the industry’s aim to decrease dependence on fossil fuels.
Green ammonia, produced using renewable energy sources, is currently seen as one of the most promising pathways to provide a sustainable energy carrier or fuel for a wide range of industries.
'When integrated with cutting-edge fertiliser technology, it presents a viable solution to address the increasing food supply demand while safeguarding the planet for future generations.,' Deepak Shetty, Nikolay Ketov, Stamicarbon (MAIRE), The Netherlands, tells OGN energy magazine.
In regions abundant in renewable energy resources and equipped with a robust fertiliser infrastructure, investing in a green fertiliser complex can be more than just a step toward sustainability.
It can serve as a catalyst for economic growth, supporting the development of new skills and expertise critical for the emerging green economy.
This approach not only addresses immediate environmental and economic challenges but also lays the groundwork for a resilient, future-proof industrial landscape.
A STRATEGIC OPPORTUNITY FOR THE GULF REGION
Currently, global ammonia production depends on fossil fuels, leading to substantial greenhouse gas emissions.
Nonetheless, there is a viable way to direct the industry towards sustainability. The most promising path, as seen by the industry leaders and regulators in most of the world, involves green hydrogen and, down the line, green ammonia.
Both can be produced using renewable energy sources such as wind, solar, geothermal, or hydroelectric power.
![]() |
Figure 1 ... The NX Stami Green Ammonia process diagram |
This process involves splitting water into hydrogen and oxygen, resulting in a carbon-free feedstock.
This production path that utilises proven and readily available technology is increasingly recognised as one of the most practical routes for transitioning to carbon-free solutions.
Overcoming the key hurdles in decarbonising the ammonia and fertiliser industry requires addressing several critical factors, including economics, infrastructure, and the availability and storage of renewable energy.
The Gulf region stands out as uniquely positioned to tackle these challenges effectively. With its abundant solar energy resources, strong policy support, advanced infrastructure, and established proficiency in chemical processes, the Gulf region has the potential to emerge as a global hub for low-carbon fertiliser production.
For example, the UAE, Saudi Arabia, and Oman have the lowest levelised cost of electricity (LCOE) for solar photovoltaic (PV), between $19 and $26 per Mwh, thanks to a capacity factor of more than 35-40 per cent.
Additionally, onshore wind LCOE is also among the cheapest in Saudi Arabia, ranging between $20 and $25 per Mwh.
Moreover, the region’s strategic location, connecting major markets in Asia, Africa, and Europe, enhances its potential to build a sustainable and efficient fertiliser supply chain.
By leveraging these advantages, the Gulf region can not only transition beyond fossil fuels but also establish itself as a pioneer in shaping the future of the industry.
Starting early in the shift toward green ammonia and fertiliser production offers significant benefits. By acting now, the key players in the industry aim to build expertise and cultivate a skilled workforce capable of managing and innovating in low-carbon production methods.
Conventional fertiliser majors are seeking opportunities to complement their established conventional projects with low-carbon hydrogen and ammonia production projects in the Gulf region.
Early adoption also enables the gradual modernisation of existing infrastructure, allowing facilities to align with new sustainability standards without causing major disruptions.
This phased approach spreads investment costs over time while ensuring infrastructure and supply chains can adapt to evolving environmental regulations and market demands.
Shipping fertiliser from the Gulf region to Europe is efficient due to the relatively low logistical costs associated with bulk fertiliser transport.
Further, the European market presents a significant opportunity, especially with the impending enforcement of the Carbon Border Adjustment Mechanism (CBAM) in 2026, which will include carbon taxes on fertilisers.
By taking proactive steps today, the Gulf region can secure a competitive position in the global market, ensuring long-term growth and sustainability.
START SMALL, THINK BIG
While the idea of immediately embarking on a global-scale green transition is appealing, it is not yet possible due to numerous bottlenecks.
The limited availability and high cost of renewable electricity, coupled with a shortage of immediately available electrolysers, make large-scale implementation challenging.
However, beginning with medium- or small-scale sustainable ammonia production provides a feasible starting point for reducing the environmental footprint of fertiliser facilities.
Stamicarbon, the nitrogen technology licensor of NEXTCHEM (MAIRE Group), offers a proven solution to the low-carbon ammonia challenge with its high-pressure NX STAMI Green Ammonia technology.
Applicable for capacities ranging from 50 to 500 metric tonnes per day (MTPD), this technology is optimised for operations reliant on green feedstock.
Designed to address the intermittent nature of renewable energy sources, NX STAMI Green Ammonia incorporates a high-pressure ammonia synthesis loop operating at approximately 300 bar (Figure 1).
This design ensures efficient production while accommodating the variability inherent in renewable energy supply.
The ammonia converter used in the NX STAMI Green Ammonia process is a single-bed axial-flow converter with a tubular design.
The feed is pre-heated using the exothermic ammonia synthesis reaction on the catalyst side to a temperature required for adequate catalytic activity. The start-up heater is integrated into the ammonia converter to ensure optimal heat integration during start-up.
Due to the high pressure, the reactor and catalyst volume can be reduced compared to larger-scale technologies.
An electrically-driven multi-service reciprocating compressor is responsible for compressing the make-up gas, recompressing the recycle stream containing the unconverted gas, managing the refrigeration loop, and, if necessary, conditioning the process stream to meet the required specifications.
The high pressure of the synthesis loop allows for single-stage ammonia condensation using cooling water.
This eliminates the need for a dedicated refrigerating compressor, thus minimising equipment count, leading to about 25-30 per cent capex savings, essential to offset the lack of economies of scale. Depending on the capacity, the plant uses about 25–250 MW of power, and its footprint is about 15 × 30 m for smaller scales and 50 × 50 m for larger scales (see Figure 2).
INTEGRATION OF TECHNOLOGIES IN A GREEN FERTILISER COMPLEX
The NX STAMI Green Ammonia technology offers a competitive solution and can be applied in combination with Stamicarbon’s nitric acid, available in mono-pressure and dual-pressure designs, and urea technologies to produce green nitrate fertilisers.
In combination with the use of recycled or recovered CO2, it reduces the carbon intensity of urea fertiliser production.
This complex might include a urea solution plant, an ammonium nitrate solution plant, and a UAN mixing plant.
NX STAMI Nitrates portfolio offers a set of technologies with optimal energy recovery and reliable operation, and due to the efficient tail gas treatment system, greenhouse gas emissions are minimal.
Having a portfolio of proprietary technologies, Stamicarbon can improve the integration between plants and consequently optimise different technologies to make the complex more attractive from an economic point of view.
Stamicarbon is also ready to apply its green ammonia and fertiliser technologies to other industries, such as steelmaking, to help make them more sustainable.
CONCLUSION
The rising global food demand presents a critical challenge for the nitrogen fertilisers industry: How to meet the growing demand while simultaneously reducing environmental impact.
In response to these challenges, we are developing new technologies to shift towards more productive agriculture and the adoption of fossil-free feedstock alternatives.
Major players in the fertiliser industry worldwide are already taking significant steps towards this goal. The move towards sustainable practices in the fertiliser industry is not just a response to environmental concerns but also a strategic adaptation to the changing demands of global agriculture.
The green fertiliser market is emerging gradually, driven by the shift to zero-carbon hydrogen in products such as Ammonium Nitrate or CAN (calcium ammonium nitrate).
Stamicarbon’s technology package offers a competitive option for local production of a high-value product with significant potential in a carbon-free economy.
A green fertiliser plant under a single licensor can streamline the integration of processes to reduce emissions, simplify maintenance, and, ultimately, maximise efficiency. This integrated approach is essential for succeeding in the challenging journey towards sustainable fertiliser production, ensuring that the industry can meet the dual demands of increasing productivity and environmental stewardship.