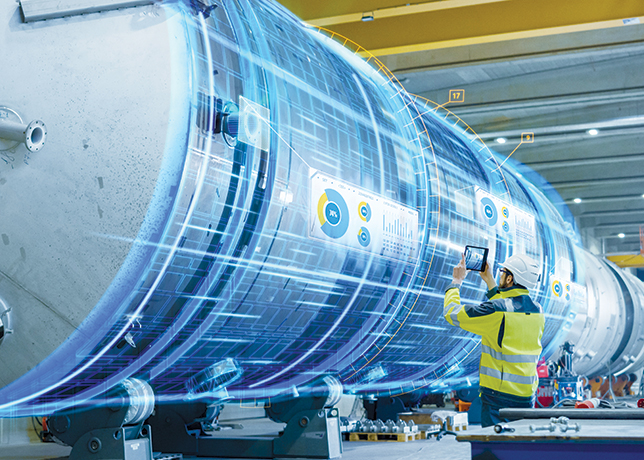
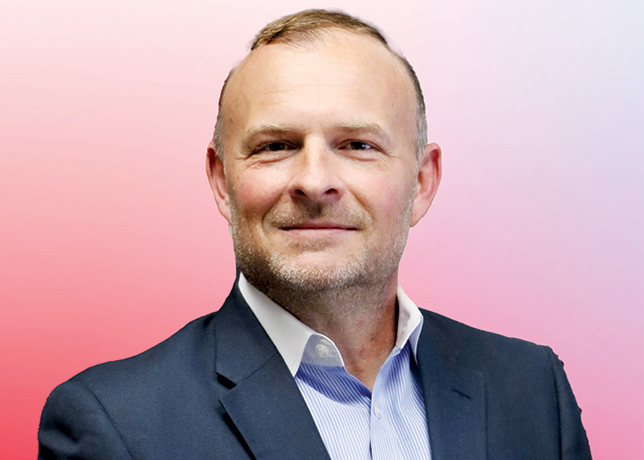
Developments in remote technology are helping to take the time, cost and potential risks out of remotely verifying instruments in dispersed desert fields, John Green of ABB Measurement and Analytics, tells OGN
The need for accurate measurement in oil and gas applications is critical as producers seek ways to maximise output and profitability whilst meeting regulatory, environmental and sustainability goals.
While the emergence of green power technologies is seeing a transition away from conventional fossil fuels, there is a continuing need for oil and gas, with an estimated growth in demand of around one million barrels per day in 2025[1].
For producers, the challenge is to strike a balance between efficient, profitable extraction whilst adhering to stringent regulatory and environmental requirements.
Producing around 31 per cent of global oil supplies[2] and 23 per cent of natural gas[3], the Middle East is home to some of the world’s largest oil and gas fields.
Covering areas spanning thousands of square kilometers, these fields are populated by hundreds of oil and gas wells using thousands of measurement instruments and analysers, each of which needs to be meticulously managed, monitored and maintained to ensure optimum performance.
As two of the world’s largest oil and gas producing areas, spanning 8,400 sq km and 560,000 sq km respectively, the Ghawar and Rub’ al Khali fields highlight the scale of the challenges faced by operators when it comes to the management of measurement devices.
In many cases, key tasks such as collecting data, configuring devices and performing checks and maintenance have traditionally involved physical visits to instruments in dispersed locations, with engineers travelling long distances to carry out the work.
![]() |
An ABB Ability™ Verification for measurement device |
Aside from the time, cost and safety implications involved, this approach also increases the scope for potential errors.
An operator must travel from their location to each device to carry out maintenance, relying on them having the correct parts and tools to carry out the work.
The process of retrieving data can also be time consuming, involving making the connection, retrieving the data, downloading the data to a computer system, generating a report, and correctly filing it in the company's reporting system where it can be accessed.
The distances that need to be travelled, coupled with the extreme conditions inherent in desert locations can also pose a risk to safety.
In a recent example, two telecommunications engineers responding to a service call in Al Ahsa province lost their lives due to dehydration after their ran out of fuel and their GPS signal failed[4].
TACKLING THE
CHALLENGES
These issues are being addressed by developments in remote digital technologies that are increasingly enabling centralised management of fleets of measurement devices.
A good illustration of how this technology is being applied is the remote verification of Coriolis flowmeters.
Coriolis flowmeters are widely used in midstream and upstream oil and gas applications. With the ability to measure mass flow, density and temperature, they eliminate the need for multiple instruments and provide accurate real time flow data.
This makes them ideal for applications including allocation metering, custody transfer, and assessing the extraction ratios of oil to gas to ensure wells are economically viable.
![]() |
An ABB CoriolisMaster |
Typically deployed in the thousands across extensive operating areas such as those characterised by the Ghawar and Rub al Khali fields, the meters will require regular verification of their performance to meet allocation meter requirements. These requirements are aimed at ensuring the meters are delivering accurate measurements.
Carrying out regular meter verifications is important as the arduous nature of oil and gas applications means that Coriolis meters can be susceptible to the effects of wear and tear.
High levels of particulate matter present a particular problem, with erosion or fouling of the meter tubes causing a frequency shift that affects the meter’s measurement accuracy.
Verification allows the user to identify if the meter is still operating within the bounds of its accuracy statement or if damage is severe enough to warrant replacement.
By itself, the task does not necessarily present a major challenge, as verifying a meter is a relatively small effort that can be carried out within minutes.
However, once the scale of oil and gas production is introduced into the equation and the numbers are multiplied to reflect the quantity of installed meters, the implications of the time and resources needed to perform regular verifications becomes obvious.
This is further compounded by the fact that at least three measurements will need to be made at each well for oil, gas, and produced water.
Operators commonly use a combination of different flow technologies – Orifice or Vortex meters for gas, electromagnetic flowmeters for water and coriolis flowmeters for oil.
In the case of ABB’s CoriolisMaster, VortexMaster and ProcessMaster electromagnetic flowmeters, the need for engineers to visit every installed meter is now replaced by a digital verification tool that can perform all the necessary tests remotely.
Called SRV500, the tool can be integrated into the operator’s network, enabling them to perform tasks including verification testing, accessing and retrieving data and generating reports without the need to dispatch an engineer to site.
Existing communications infrastructures can be used to relay data between the SRV500 tool and the device being verified. As all processing happens within the tool, the data can be relayed as a very small packet with minimal impact on network performance.
![]() |
As well as the verification process itself, the tool can also be used to check device status, make configuration changes and software updates and perform troubleshooting.
THE COST-EFFICIENT PATH TO COMPLIANCE
As a labour-intensive process, physical verification of flowmeters has traditionally been resource-intensive and represented a significant operational cost.
By eliminating much of the effort required to visit and test meters, remote verification offers a cost-effective way to achieve compliance whilst also enabling smarter resource utilisation by releasing engineers to perform other tasks.
The example in table 1[5] is based on oil and gas operations in the remote desert locations in the Permian Basin in the US.
It highlights how remote verification can open the opportunity for massive savings in the costs associated with physical verification, as well as significant reductions in the time needed to verify an installed base of meters.
SUMMARY
Remote verification offers the opportunity for greatly enhanced cost efficiency and safety whilst ensuring fully compliant measurement of oil, gas and produced water flows.
By digitalising the tasks involved in verifying their field devices across their production sites, operators can streamline verification processes, reduce the need for extensive fieldwork, and minimise safety risks in challenging environments.
By enabling centralised management of measurement devices, technologies like ABB’s SRV500 can help operators realise new possibilities for accessing real-time data, efficient reporting, and enhanced resource utilisation.
This shift not only reduces operational costs but also empowers engineers to focus on higher-value activities, supporting the industry’s goals of maximising efficiency, profitability, and sustainability while meeting regulatory requirements.
REFERENCES
• International Energy Agency (IEA): Oil Market Report – November 2024.
• International Energy Agency (IEA): Oil Market Report – August 2022.
• International Energy Agency (IEA): Gas market Report, Q4-2022.
• Kuwait Local: Indian Technician Dies in Rub' al Khali Desert Following GPS
Malfunction
• ABB.
* John Green has dedicated his 18-year career at ABB to enhancing production and operations efficiency, collaborating with leading oil and gas companies to economically provide energy for the modern world.