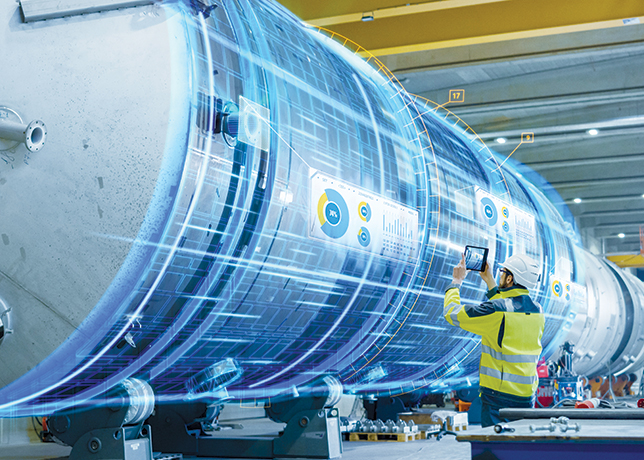
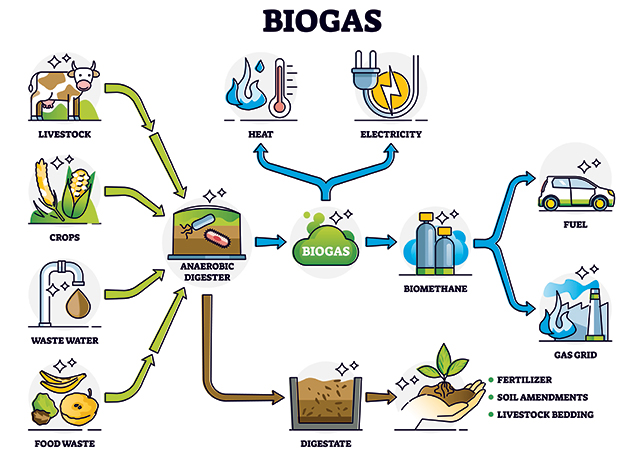
Process analysers ensure quality, regulatory compliance, and environmental sustainability while enhancing efficiency and methane output in the growing biogas energy sector, Harry Burton and Michael Gaura tell OGN
The creation of fuels and energy from various sources is a constantly evolving process. Economic considerations drive the use of inexpensive feed stocks and lower operational expenditures.
Safety nets exist to protect the workers and facilities, and environmental regulations or societal pressures are introduced to minimise the impacts on nature and global climate.
Satisfactorily balancing these often competing objectives requires constant evaluation of energy production activities.
'Thankfully, a useful tool exists to assist in plant operation management – process analytics. Process analytics combines the direct measurement of temperature, pressure, flow, chemical composition, and other variables with sophisticated algorithms,' Harry Burton and Michael Gaura from AMETEK Process Instruments, in Newark, Delaware, tell OGN energy magazine.
The output of this information gathering and processing drives automated activities such as management of heater temperatures, incoming and process throughput flows and mixing, and pressurisation activities.
The result is economically viable, safe, and environmentally responsible operations with a final product that meets or exceeds established quality specifications.
In most instances, a process analyser is the most crucial contributor of critical information, as it is measuring specific component concentrations throughout the production process.
The process analyser is used to ensure incoming, in process, and final products contain the correct components, at the appropriate concentrations, to support the plant’s production capabilities and capacities.
In this article, we specifically focus on analytical measurements in Biogas production, as this sustainable energy is of increasing importance as attempts are made to balance increasing energy demands with the health of the global ecosystem.
Biogas and bio-methane have seen a surge in production rates over the last few decades.
Biogas reached nearly $68 billion in 2022, with projections showcasing can increase of 4.7 per cent between 2023 and 2028.1
Key to this growth will be the assurance of large quantities of methane gas product.
![]() |
Figure 2 ... gas chromatograph elution process. Gas is injected into the elution column, which is heated to a high temperature such that it vapourised. Carrier gas is used to push these vaporised molecules through the column, which is measured by a detector and analysed |
This demand drives technological growth in the industry, but also sees additional challenges in meeting environmental regulations from worldwide governments.
A directive issued by the European Union (EU) expects a targeted reduction in greenhouse gas (GHG) emissions of 40 per cent by 2030.2
As biogas becomes a more reliable energy source, it will also be expected to adhere to these same targets.
Biogas industries will need to maximise the carbon capture footprint for both methane (CH4) and carbon dioxide (CO2), to meet these challenges, while also ensuring they have stable process control mechanisms to deliver high quality product.
All of which is intended to keep this industry centered as a reliable – and renewable – energy source.
To ensure these industry leaders can meet their targets, both economically and regulatory, process analysers can serve as a key instrument in biogas treatment units.
These instruments provide the benefit of consistent gas composition monitoring, but also ensure that harmful contaminants that may degrade product quality or pose corrosion concerns are removed.
Prior to detailing the elements of a process analyser, it is important to first detail the process by which biogas is produced.
A central mechanic to biogas production is through Anaerobic Digestion (AD), which is the degradation and stabilisation of organic substances in an oxygen-less environment.
Intrinsically, this is of great benefit in biogas production as it aids in the retention of both CH4 and CO2.
It also aids in the reduction of unneeded waste products and potential pathogens.
At the start of this process is waste collection, typically food, plant, manure, wastewater, and sewage; all of which are separated into their own lots and serve as biogas feedstock.
Each waste material will undergo its own form of size reduction and/or contaminant removal. Once this process has completed, these feedstocks will be mixed and stored for digestion (Figure 1).
The method in which AD is fostered in biogas production is varied. This can include lagoons which rely on polypropylene covers to trap CH4 gas.
A more common approach is the inclusion of mixers, which utilise hydraulic mixing systems that blend the various feedstocks and promote the growth of microorganisms (including methanogens) to break down these feedstocks and respirate the desired biogas product.
Bacterial hydrolysis is central to digestion, as it allows feedstock monomers–such as glucose–to be broken down into simple sugars and amino and fatty acids.
The subsequent processes of acidogenesis, acetogenesis, and methanogenesis all culminate in the production of CO2 and CH4:
C6 H12O6 ---> 3CO2+3CH4
Once digestion has completed, the biogas is transferred to a gas treatment system which separates any remaining contaminants. These include moisture, siloxanes, ammonia, oxygen, carbon monoxide, or nitrogen.
Key to this contaminant separation is the removal of hydrogen sulfide (H2S) before entering the energy grid.
Each country relies upon its own environmental safety standards to control emissions of harmful chemicals that may be introduced to the public.
This also includes infrastructure, such as each nation’s respective energy grid.
Limits are often imposed on such chemicals to ensure hazardous conditions are mitigated.
The American Biogas Council states that CO2 must be less than 2 mol per cent, H2S at 9 ppm, and total sulfur at 35 ppm3, before biogas is injected into the energy grid.
There is relative equivalency in European markets, with H2S limitations of 0–10 ppm.
Given these constraints, biogas end-users will find it necessary to monitor the chemical compositions of their biogas streams during compression to ensure efficiency and to uphold regulatory standards.
For this reason, it is ideal that biogas producers consider an analytical instrument for monitoring gas composition during both compression and treatment processes.
When needing to monitor process characteristics at the high- and low - pressure sides of biogas treatment, process analysers are proven instruments for the job.
A common mainstay in the biogas industry is the use of electrochemical sensors as tools for monitoring methane.
These sensors use porous membranes which allow the chemical to permeate the electrode attached to the sensor. This oxidises the gas and produces a charge (or current).
The degree of current output measured is intrinsically tied to the concentration of the gas.
More notably is how these sensors operate with high linearity at low concentrations. A secondary benefit of these sensors also lies in their ability to operate in high-pressure environments common with biogas compression.
The monitoring of upsets during biogas upgrading is also feasible with both UV (ultraviolet) process analysers and gas chromatographs (GC).
Both analyser types can measure at the low-pressure side, and are resistant to corrosion caused by sulfur chemicals, unlike electrochemical sensors.
For GCs, biogas is injected into the instrument, and carrier gas (such as N2) is used to push the gas through an elution column.
Within the column, the gas is vapourised and each chemical species within the gas is separated through the column at different time intervals.
The GC will then measure each chemical, comparing its spectral qualities and time of arrival against a database.
The final output is a concentration response that is highly accurate, even at low concentrations. Figure 2 provides a view of this process.
UV analysers used in measuring sulfur components implement spectroscopic techniques for measurement.
UV light is transmitted through the biogas, with certain wavelengths of the light being absorbed in the UV-C spectrum (< 280 nm), which is a common absorbance region for sulfur-bearing species.
Using Beer’s Law, it’s possible to link the absorbance response of the sulfur species to its concentration.
When calibrated properly, these UV analysers provide the capacity for measuring multiple sulfur species simultaneously.
It is even possible to combine the UV spectroscopic capabilities, along with the elution column separation approach, to provide faster response times than that of a GC while still gaining the low concentration specificity of a GC.
If required, CO2 can also be monitored with IR-capable analysers, such as those using IR emitters or Fourier transform IR (FTIR).
To provide an illustration, Figure 3 showcases examples of H2O, CH4, and CO2 IR spectra. Several analyser options are open to biogas producers in meeting their needs, whether it be for process stability and quality, or meeting environmental standards.
The biogas industry is a growing market, but it is also one that is reliant upon meeting worldwide demand for natural gas product while also ensuring adherence to environmental code.
This market exists today, at a time when multiple instruments are available to help meet both of these criteria.
Process analysers are becoming an increasingly important mechanism for process control and carbon capture and have proven themselves across several industries for decades (and more to come). These instruments provide not only peace of mind for many end-users but are valuable in providing efficient cost savings during their operation.
LITERATURE CITED
1 IMARC, 'Biogas market: Global industry trends, share, size, growth, opportunity and forecast 2023–2028,' 2023, online: https://www.imarcgroup.com/biogas-market
2 EU, 'A policy framework for climate and energy in the period from 2020 to 2030,' 2014, online: https://eur-lex.europa.eu/legal-content/EN/ALL/?uri=celex per cent3A52014DC0015
3 American Biogas Council, 'Purity recommendation,' online: https://americanbiogascouncil.org/resources/rng-purity-recommendation-american-biogas-council/
By Abdulaziz Khattak