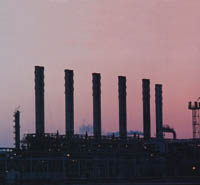
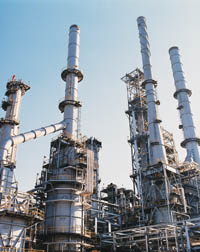
the newly-constructed South Refinery Upgrade Project Plants at the Ras Tanura refinery faced a severe problem because incorrect welding consumables had been used to make some of the welds.
Thermowell 212 had cracked during a catalyst sulphidation operation. The sulphidation involved approximately 20,000 ppm of hydrogen sulphide gas at 2,150 prig and 260¡C (500¡F).
The cracked Thermowell was sent to the Consulting Services Department/ Materials Engineering Unit for evaluation.
The failure analysis determined that it had failed due to sulphide stress corrosion cracking because the weld and heat-affected zone had not been properly postweld heat-treated and were too hard.
The weld and heat-affected zone of this 11/4 chromium, 12 molybdenum alloy had an average hardness of Vickers 320, equivalent to a Brinell 300, while the project specification required a hardness of Brinell 225 or less.
The failure analysis report concluded that this weld was undersized and contained rejectable welding defects. Because of this failure and observed problems with this weld, the refinery decided to take a closer look at all 1,500 and 2,500 prig rated process piping in the J80 Hydrocracker.
The initial investigation consisted of sizing all high-pressure socket welds, dye checking all welds for surface defects, radiographing all socket welds, taking ultrasonic thickness readings on all high-pressure piping components (particularly all smallbore branch connections), taking hardness readings of all alloy welds and performing positive -material identification (PMI) on all alloy piping.
Each of these tests found many problems with the existing construction work. Some of these defects were so severe that if they had not been corrected, catastrophic failures would have occurred soon after the plant was started.
During PMI on low-pressure alloy piping, a weld was found that contained a mixture of carbon steel and 11/4 chromium, 1/2 molybdenum.
This mixed-metallurgy weld, or ''rogue weld,'' was an unexpected find.
Normally, when PMI work is performed, a wrong weld may occasionally be found, but less rare is the finding of a mixed-metallurgy weld.
This weld was cut and sent to the Consulting Services Department/Materials Engineering Unit, where they confirmed that a mixed-metallurgy butt weld had been installed.
This finding drastically changed the focus of the post-construction inspection investigation. Until this find, it had been expected that the rectification effort in the J80 Hydrocracker would take three months.
However, the search for rogue welds is difficult, and this became the critical path for getting the plant ready for start-up. When the search for rogue welds was extended to carbon steel welds, the work lasted for 10 months.
Integrity
As part of the rectification efforts at the hydrocracker, a contract with Plant Integrity Ltd., a TWI Company, was signed to study the effects of incorrect welds at the Ras Tanura Refinery.
At the start of this contract, it was expected that the incorrect welds would all be of the same metallurgy and not mixed-metallurgy welds. However, after the first rogue weld was found, several others were found and these findings were incorporated into the study.
Plant Integrity Limited issued a report titled ''Potential Effects of Incorrect Additions to Butt Welds at the Ras Tanura Refinery: Failure Modes and Effects Analysis''.
Conclusions about mixed-metallurgy welds were:
Procedures
Surface PMI
The surface of a weld can be analysed using a portable metal analyser to determine the concentration of specific elements.
This metal analyser uses x-ray fluoresces to determine the presence and amount of selected elements. In the case of the J80 Hydrocracker, the materials of most interest were the mixing of carbon steel and chromium-molybdenum alloys.
The metal analyser can detect only what is on the surface. In the case of an incorrect filler metal being buried in a weld - for instance, a 5 chromium, 1/2 molybdenum filler being used in a carbon steel weld - the metal analyser can detect this alloy filler only if it is within three passes or 0.89 cm of the surface. As some of the larger-diameter high pressure piping in J80 are more than 3.8 cm thick and have many weld passes, other techniques were needed to detect an incorrect filler metallurgy in these welds.
Because the surface PMI was finding mixed-metallurgy welds, mostly where repairs had been made to part of the weld, the surface PMI procedure was changed to take multiple readings on each weld to find these repairs.
Boat sampling
This was the first destructive or invasive technique considered and used to analyse thick-walled-pipe alloy welds.
A circular saw blade cuts out a piece of boat-shaped metal. By carefully adjusting the angle of this cut, it is possible to sample all the passes in a weld. A special boat-sampling machine is required, of which only four could be located and job-sited in the short time required for this job.
Drilling
When carbon steel welds were added to the list of welds that had to be sampled for rogue welds, the number of welds increased from 238 alloy welds to more than 8,500 carbon steel welds. This increased the work by a factor of 33. At the rate that the boat sampling machines were cutting the alloy welds, it would have taken 3.8 years to complete all the carbon steel welds.
To expedite the sampling of carbon steel welds, a second invasive technique was developed. This involved using a drilling press to remove core samples from a weld at 3 mm depths using a pattern based on the thickness of the weld.
The core drillings were bagged, labelled and later compressed, and the resulting disks were analysed with a metal analyser. The advantages of drilling versus boat sampling were speed and number of units placed in the field. All that was needed was a modified drill press stand mounted on a pipe.
Flat grinding
To further increase the rate of welds sampled, a third invasive technique was developed.
Welds that were less than 1.9 cm in thickness were flat-ground so the metal analyser detection limit of 0.89 cm was met, then were surface PMIed.
The number of welds was around 7,400. However, the work progress using this procedure was much slower than expected, and finally, it did not address the last remaining problem, which was how to test the welds on 2,300 Sockolet fittings.
Vee notching and etching
The final invasive technique developed involved grinding a vee notch in the weld to the root pass and then applying a 10 per cent solution of Nitol on the notched portion of the weld.
If the weld contained either a 5- or 9-chrome rogue filler metal, the Nitol etchant would result in the chromium metal showing up as white against the rust color of the rest of the carbon steel weld.
Findings
Surface PMI
Approximately 220,000 readings were taken during the rectification work at J80 Hydrocracker along with the J06 Hydrogen Plant, J85 Visbreaker, J78 Sour Water Stripper Plant and J72 Sulphur Plant.
Of this, 160,000 were taken on existing installed components and welds and the other 60,000 covered all repair work. During this PMI effort, slightly more than 1,600 components and welds were found to have incorrect metallurgies versus required design specifications.
Most of the mixed-metallurgy welds found with surface PMI were repairs made to an existing weld where an incorrect filler electrode was used during the repair.
The first rogue weld found was the result of carbon steel being mixed with a 11/4 chromium, 1/2 molybdenum butt weld.
The next rogue welds found were 316 and 309 stainless steel welds used to repair 347 stainless steel butt welds. Also, several 11/4 chromium, 1/2 molybdenum welds where found with high chromium using surface PMI, but the results were not confirmed until the welds were boat sampled.
Another rogue weld was where a 316 stainless steel weld was used to repair a 10.16 cm carbon steel butt weld.
Boat sampling
A total of 238 welds were selected for boat sampling. These welds were on the large-bore (25.4 cm and above) 11/4 chromium, 1/2 molybdenum alloy pipes that were in 1,500 psi service.
Eight welds were found in which higher chromium molybdenum welding electrodes were used in 11/4 chromium, 1/2 molybdenum welds.
Drilling
Approximately 1,100 high-pressure heavy-wall carbon steel welds were drilled. One rogue weld was found using this procedure and consisted of a 5 chromium, 1/2 molybdenum root pass in a carhop steel weld.
Flat grinding
Only a couple of hundred welds were analysed using the flat grinding procedure before the vee notching and etching procedure was implemented. No mixed-metallurgy welds were detected with flat grinding.
Vee notching and etching
Approximately- 11,100 butt welds and 2,300 Sockolet welds were ultimately analysed using the vee notching and etching procedure.
One carbon steel Sockolet weld was found in the J06 Hydrogen Plant with chromium-molybdenum filler metal.
Ten months were spent correcting the deficiencies noted. More than 1,600 incorrectly installed materials were found during this rectification project.
Three weeks after the J80 Hydrocracker was started, several welds started leaking in the J80-F-310 Debutaniser Furnace.
This furnace had been constructed at a subcontractor's shop and was not checked as part of the rectification work done at the J80 Hydrocracker because it was felt that shop work should have had better quality control.
The failed welds were removed from this furnace and sent to the Consulting Services Department/Materials Engineering Unit for failure analysis.
The failure analysis determined that each leaking weld failed due to sulphide stress corrosion cracking because the repaired areas had not been heat treated after the repairs were made and were very hard. Even more surprising was a finding that the root pass on each of these 9 chromium, 1 molybdenum welds had been made with carbon steel.
Quality control is critical during plant construction. Since the J80 Hydrocracker and the J85 Visbreaker were constructed from both carbon steel and chromium-molybdenum alloy components, quality control should have been very carefully set up and implemented.
In this case, the quality control programme did not work and numerous problems occurred. This project was a Lump Sum Turnkey (LSTK) project, with the contractor responsible for its inspection.
Hixson is a corrosion engineer in Ras Tanura Refinery's Inspection Unit.